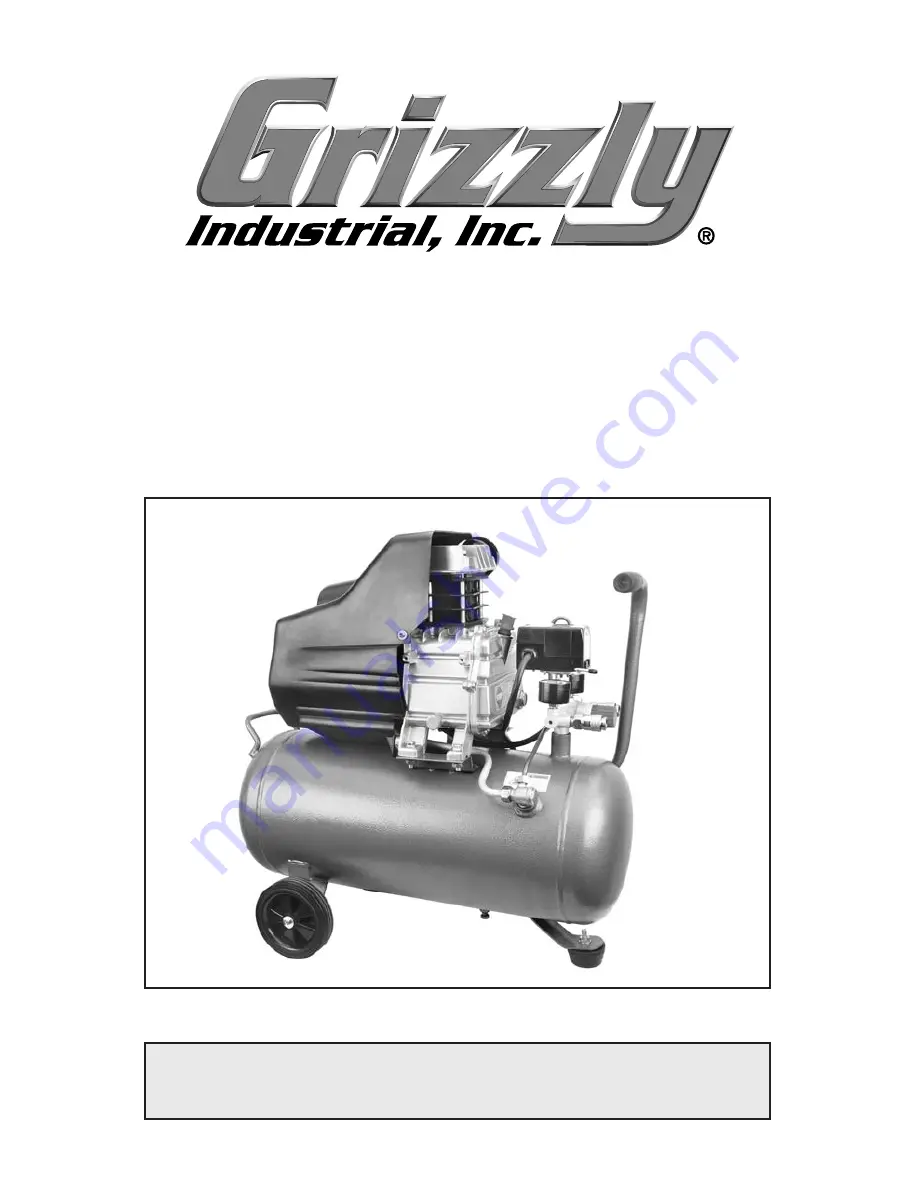
Copyright © FEBrUAry, 2010 By grizzly indUstriAl, inC.
Warning: no portion of this manual may be reproduced in any shape
or form Without the Written approval of grizzly industrial, inc.
For modEls mAnUFACtUrEd sinCE 02/10 #Cr12612 printEd in ChinA
model t21888
2.5 hp,
6.3 gallon compressor
instruction manual