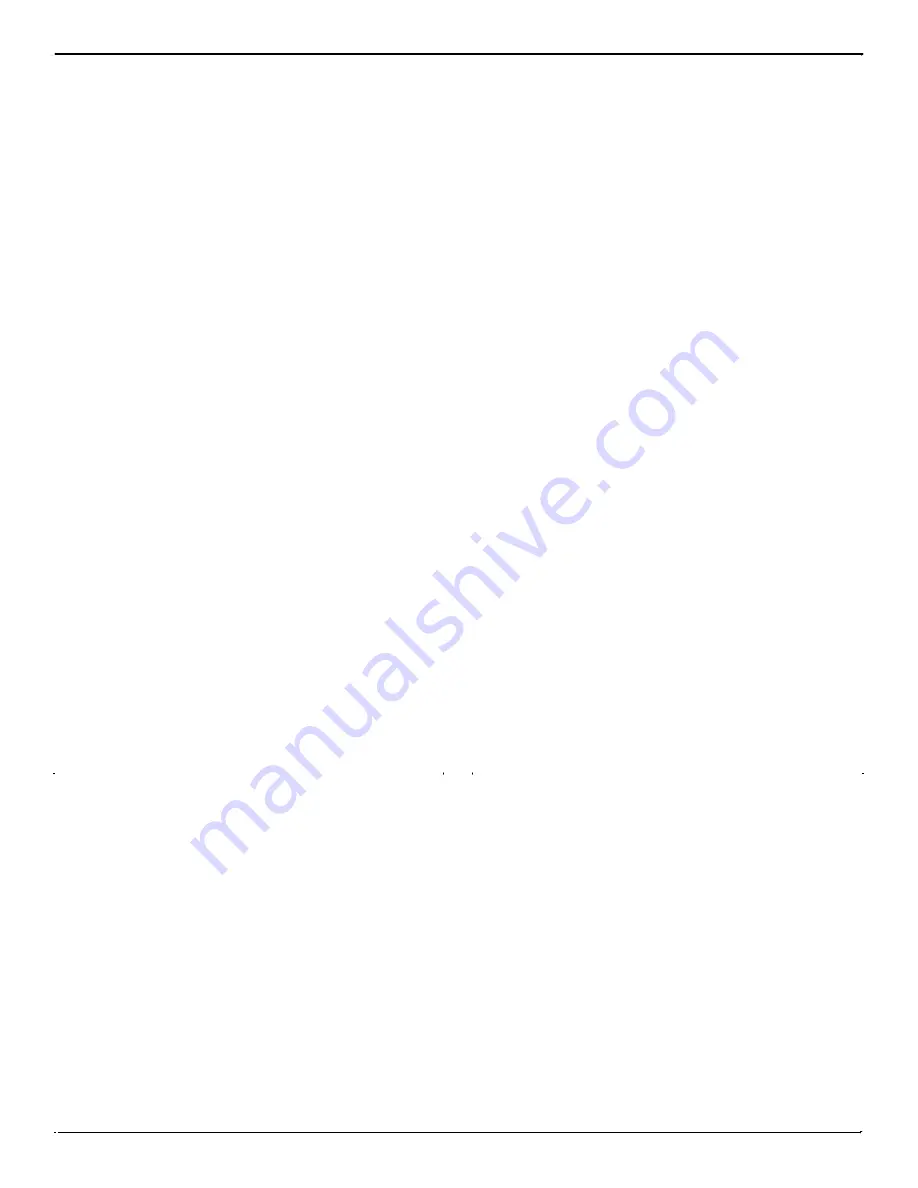
4. Drive tool PT-6 out with permanent rocker arm pin
(33). Place washer over small end of pin and spread pin
end with ball peen hammer or round nose punch.
5. Place valve and cage gaskets (13) in recesses provided
in fuel cover (6). Inlet valves must have three-legged
spider facing out of cover, and outlet valve must have
three-legged spider facing into cover. Secure valve
assemblies with retainer (14), and screw (3).
6. Install strainer screen (7), bowl gasket (8), bowl (9),
bowl screw gasket (10) and bowl screw (11) in the
order named. Install air dome (14) in threaded hole
in projection of casting for outlet.
7. Install fuel cover on body, making sure that file marks
on cover and body line up. Push on rocker arm until
diaphragm is flat across body flange. Install cover
screws and lock-washers loosely until screws (16) just
engage lock-washers. Pump the rocker arm three or four
full strokes and tighten cover screws alternately until
secure.
8. Diaphragm must be flexed before tightening cover
screws, or pump will deliver too much pressure.
9. Place two gaskets (26) and two valve and cage
assemblies (27) in cover (25). Inlet valve must have
three-legged spider facing out of cover, and outlet
valve must have three-legged spider facing into cover. Secure
valve and cages with retainer and screw.
10. Turn cover over and set screen (22) in recess over valve
hole. Set screen retainer (21) on screen. Place cover
gasket (20), cover (19), cover screw gasket (18), and
cover screw (17) in position in. the order named and
tighten cover screw.
11. Assemble oil seal on vacuum diaphragm pull rod in the
following sequence: oil seal spring (31), upper retainer
(34), oil seal washer (32),and lower retainer. Turn lower
retainer 90 degrees to lock in position.
12. Lift the pump body above eye level, facing the
vacuum diaphragm flange. The two vacuum links
will swing down so that the diaphragm pull rod can
be hooked to both links.
13. While holding vacuum diaphragm in position the
body should be clamped in a vise, vacuum side up.
Clamp by one of the mounting flange ears. The
vacuum diaphragm must be held level with body
flange during the following operations by inserting
a 3/32 " piece of metal between rocker arm stop and
body. This spacer can be made from piece of steel,
3/16" to 3/32" by 8 inches. Bend one end to form a
right angle hook, 3/8" from bend to end. (This tool
is available from your AC jobber as tool Pt-8.)
14. Place spring retainer (29) on riveted end of dia-
phragm pull rod, and place spring (28) on the
retainer. Place vacuum cover and valve assembly
over spring and align the file marks.
15. Insert two No. 10-32 x 1-1/2" screws in opposite
holes in cover flange. Turn these long screws down
as far as they will go without forcing, alternating a
few turns on each. Insert regular screws with lock
washers and tighten until screws just engage lock-
washers. Replace two long screws with regular
screws and lock-washers.
16. Remove 3/32" spacer from rocker arm position.
This allows the heavy vacuum spring to push dia-
phragm into a flexed position. Tighten all cover
screws alternately until secure.
17. Combination fuel and vacuum pump cannot be
bench tested because of the heavy vacuum spring.
Use a vacuum gauge and test pump while pump is
assembled to engine.
FUEL SYSTEM & EXHAUST 4 - 37
Summary of Contents for 1948 - 1952
Page 1: ...HUDSON SHOP SERVICE MANUAL 1 9 4 8 1 9 5 2...
Page 2: ...This manual courtesy of Hudson Essex Terraplane Club member Drew Meyer...
Page 10: ...VIII...
Page 12: ...1 2 LUBRICATION FIGURE 1...
Page 13: ...LUBRICATION 1 3...
Page 14: ...1 4 LUBRICATION...
Page 46: ...3 4 ENGINE FIGURE 1...
Page 52: ...3 10 ENGINE FIGURE 8...
Page 70: ...3 28 ENGINE FIGURE 32...
Page 71: ...ENGINE 3 29 FIGURE 33...
Page 76: ...3 34 ENGINE FIGURE 40...
Page 78: ...3 36 ENGINE FIGURE 41...
Page 81: ...ENGINE 3 39 FIGURE 44...
Page 119: ...FUEL SYSTEM EXHAUST 4 35 FIGURE 106...
Page 148: ...6 12 ELECTRICAL SYSTEM FIGURE 10...
Page 149: ...ELECTRICAL SYSTEM 6 13...
Page 152: ...6 16 ELECTRICAL SYSTEM FIGURE 12...
Page 180: ...8 2 TRANSMISSION FIGURE 1...
Page 198: ...8 20 TRANSMISSION FIGURE 10...
Page 209: ...OVERDRIVE 9 1...
Page 215: ...OVERDRIVE 9 7 FIGURE 10...
Page 238: ...9 30 OVERDRIVE REFERENCE Source of Information Date Subject...
Page 260: ...11 18 REAR AXLE FIGURE 25...
Page 286: ...12 18 FRONT SUSPENSION REFERENCE Source of Information Date Subject...
Page 306: ...14 8 SPRINGS SHOCK ABSORBERS STABILIZERS REFERENCE Source of Information Date Subject...
Page 322: ...15 16 BRAKES REFERENCE Source of Information Date Subject...
Page 330: ...REFERENCE Source of Information Date Subject...
Page 331: ......
Page 332: ......
Page 333: ......