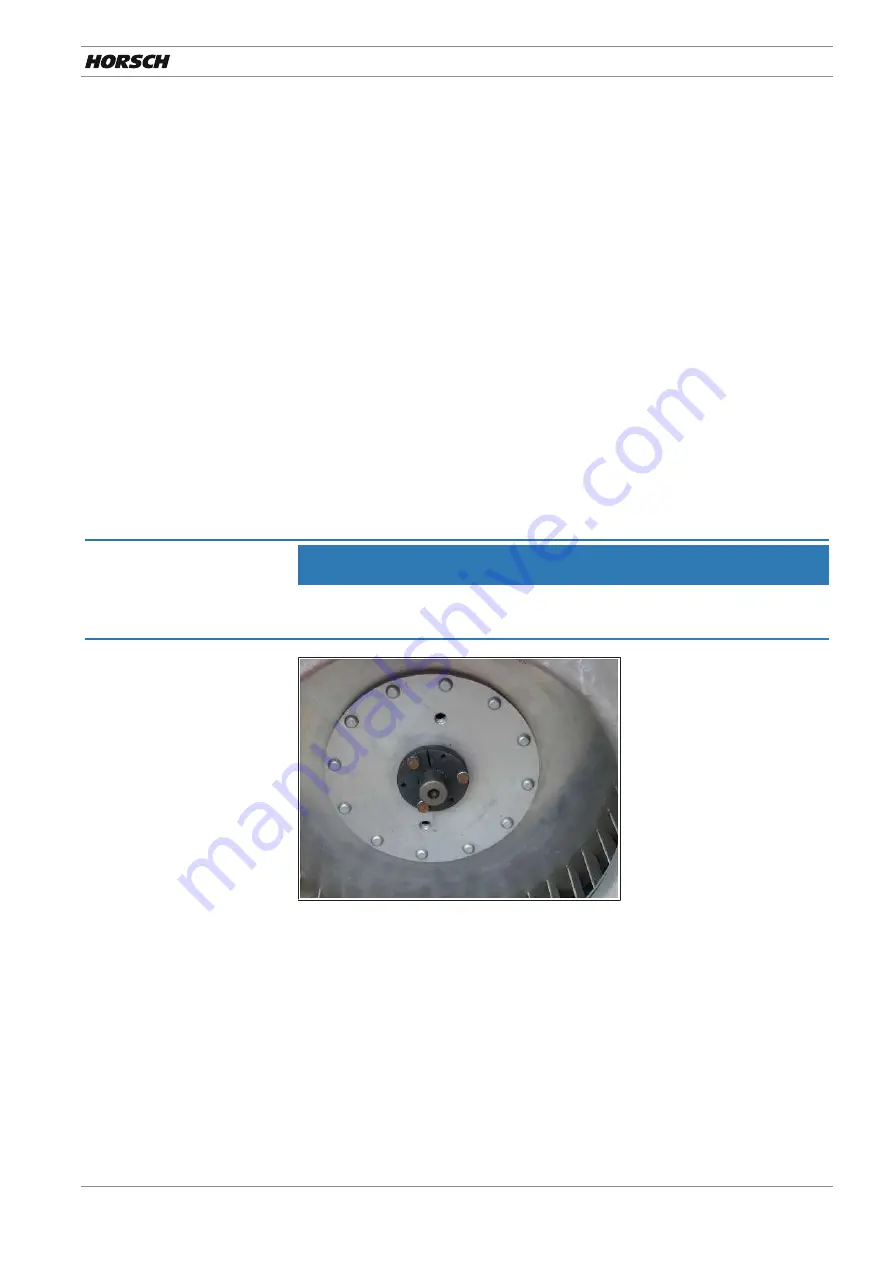
Pneumatic system | 7
60013444 • 01 • 01/2021 • en
73
Deposits on the protective grid restrict the air flow and thus lead to blockage in the
hoses.
Ø
Clean the protective suction grid at regular intervals to prevent a restriction in
air flow and resulting blockage.
Deposits on the fan impeller cause unbalance. The bearing will thereby be over-
loaded and can be damaged.
Ø
Clean any dirt or deposits from the fan blades to prevent unbalance and dam-
age to impeller and bearing.
The hydraulic oil could overheat if the radiator fins are soiled and cause clogging of
the fertiliser hoses.
Ø
Clean the radiator fins at regular intervals.
7.6.1 Retightening the fan flange
The clamping taper fixates the fan wheel and additionally clamps on the drive shaft.
The clamping taper on the fan drive may come loose. The impeller can thus move
along the drive shaft and damage the fan.
NOTE
After approx. 50 hours retighten the clamping taper on the fan flange and check it
annually.
Clamping taper
When tightening the screws, especially with a new assembly, the fan wheel will
move towards the housing in the direction of the protective grid.
1. Align a loose flange closer to the hydraulic motor, the gap between impeller
and intake side must remain as small as possible.
2. Clean the clamping faces from oil and grease.
3. The clamping screws must be tightened uniformly and in several steps. Use a
plastic hammer or hammer shaft in between to carefully knock on the flange
to facilitate pulling onto the cone.
4. The inch screws in versions no. 10-24 4.6 may be tightened with a torque of
max. 6.8 Nm.
5. After tightening check the impeller for free and even running.
Summary of Contents for Maestro CX
Page 2: ......
Page 29: ...Technical data 4 60013444 01 01 2021 en 29 Maestro 12 CX 5550 6390 5900 2990 3890 2960 6790...
Page 140: ...14 Optional equipment 140 60013444 01 01 2021 en 38 cm 66 cm...
Page 181: ...60013444 01 01 2021 en 181 Notes...
Page 182: ...182 60013444 01 01 2021 en...
Page 183: ......