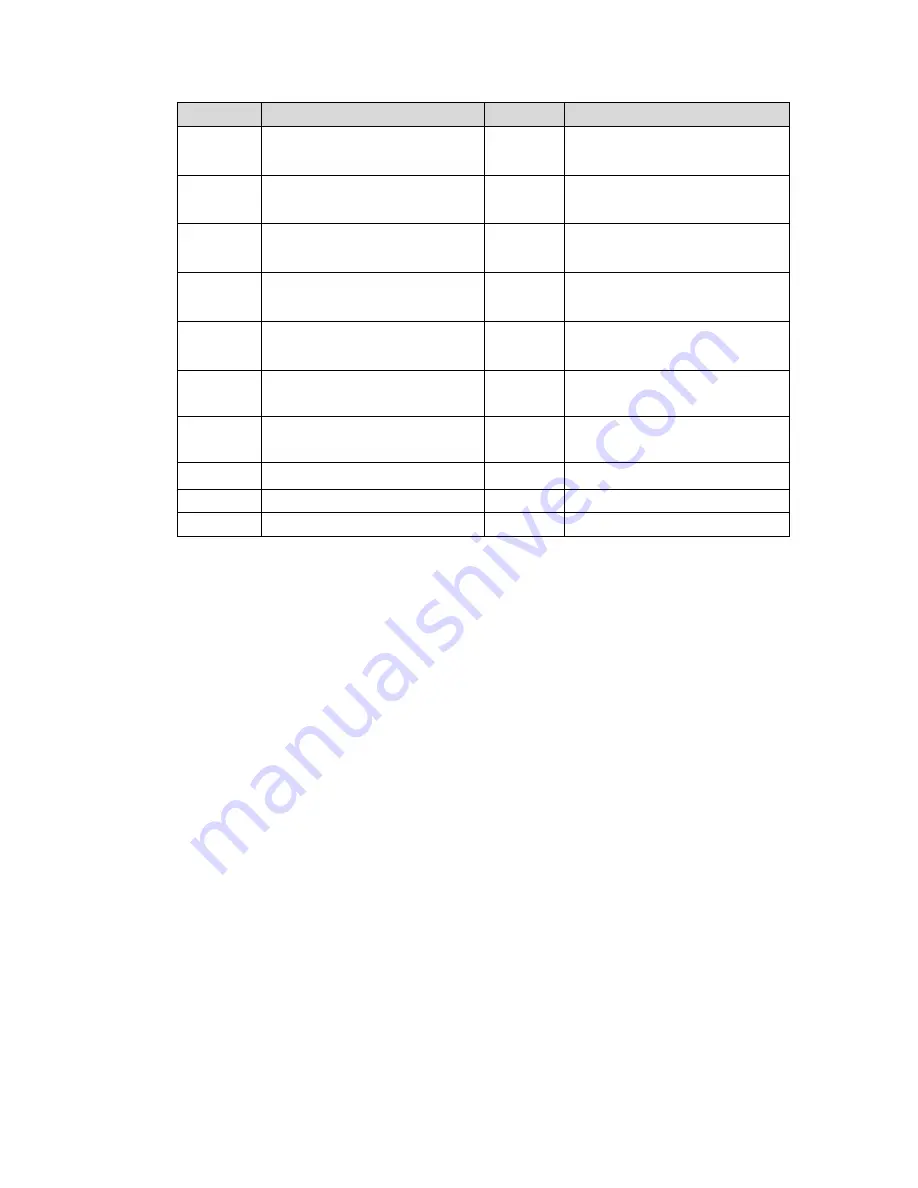
39
Table 6-8 Parameter Setting and Function of Output Terminals
Setting
Function
Setting
Function
0
Inverter running signal
(
RUN
)
1
Frequency arrival signal
(
FAR
)
2
Frequency detection
threshold
(
FDT1
)
3
Reserved
4
Reserved
5
Low voltage lock-up signal
(
LU
)
6
External stop command
(
EXT
)
7
Higher limit of frequency
(
FHL
)
8
Lower limit of frequency
(
FLL
)
9
Zero-speed running
10
Completion of simple PLC
operation
11
PLC cycle completion
indication
12
Preset counting value
arrival
13
Specified counting value
arrival
14
Inverter running state
15
Inverter is ready
(
RDY
)
16
Inverter fails
17
Extended function 1 of host
18
Reserved
19
Preset operation time out
The explanation of output signal is shown in Table 6-8.
0: Inverter running signal (RUN)
This signal will be given if the inverter is running.
1: Frequency arrival signal (FAR)
See F6.13.
2: Frequency detection threshold (FDT1)
See F6.14~F6.15.
3: Reserved
4: Reserved
5: Low voltage lock-up signal (LU)
The signal will be given when the DC bus voltage is lower than the low
voltage limit, and the LED displays “-LU-”.
6: External stopping command (EXT)
The terminal outputs the indicating signals if the inverter outputs tripping
signal caused by external fault (F.Ed).
7: Higher limit of frequency (FHL)
The signal is given if the preset frequency is higher than upper limit of
frequency and the operating frequency reaches the upper limit of frequency.
8: Lower limit of frequency (FLL)