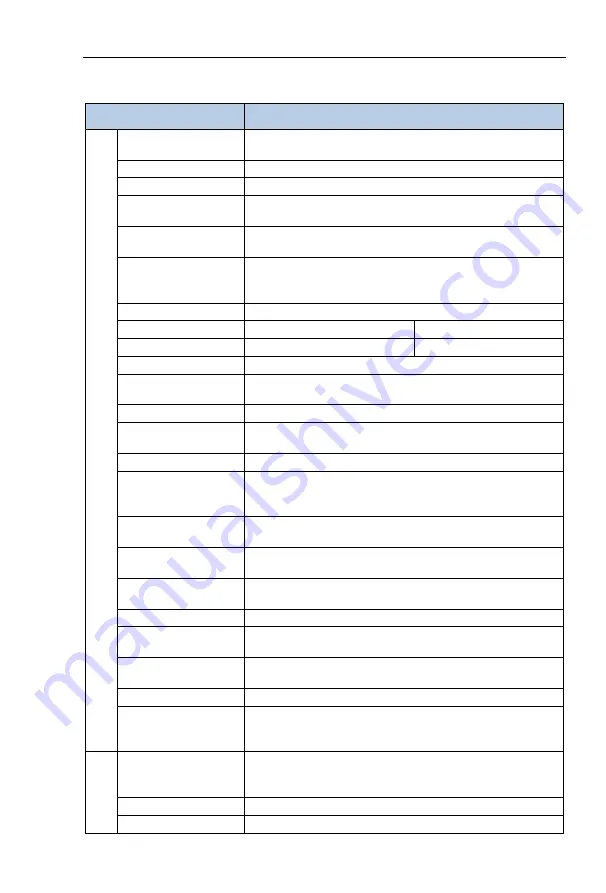
Section I.
Product Information
9
1
.
5 Standard specification
Item
Specifications
Basic fu
nction
Control system
High performance of current vector control technology to realize
asynchronous motor and synchronous motor control
Drive performance
High efficiency driving for induction motor and synchronous motor
Maximum frequency
Vector control
:
0~300HzV/Fcontrol
:
0~3200Hz
Carrier frequency
0.5k~16kHz;thecarrierfrequency
will
be automatically
adjusted
according to the load characteristics
Input frequency resolution
Digital setting
:
0.01Hz
Analog setting
:
maximum frequency ×0.025%
Control mode
Open loop vector control(SVC)
Closed loop vector control(FVC)
V/F control
Startuptorque
Type G
:
0.5Hz/150%(SVC)
;
0Hz/180%(FVC)
1
:
100(SVC)
Speed stabilizing precision
±0.5%(SVC)
Speed stabilizing precision
Torque control precision
±5%(FVC)
Over load capability
G type
:
rated current 150% -1 minute, rated current 180% -3
seconds;
Torque boost
Auto torque boost function
;
Manual torque boost 0.1%~30.0%
V/Fcurve
LinearV/F,Multi-point V/Fand Square V/F curve (power of 1.2, 1.4, 1.6,
1.8, 2)
V/F separation
In 2 ways
:
separation ,semi seperation
Acc. /deccurve
Straight line or S curve acceleration and deceleration mode.
Four kinds of acceleration and deceleration time. Acceleration and
deceleration time range between 0.0s to
65
00.0
s
DC brake
DC brake frequency
:
0.00Hz to maximum frequency,brake time
:
0.0s to 36.0s, and brake current value
:
0.0% to 100.0%.
Jog control
Jog frequency range
:
0.00Hz~50.00Hz. Jog acceleration/deceleration
time 0.0s~6500.0s.
Simple PLC and MS speed
running
It can realize at maximum of 16 segments speed running via the built-
in PLC or control terminal.
Built-in PID
It is easy to realize process-controlled close loop control system
Auto voltage regulation
(AVR)
It can keep constant output voltage automatically in case of change of
network voltage.
Over-voltage/current stall
control
It can limit the running voltage/current automatically and prevent
frequent over-voltage/current tripping duringthe running process
Quickcurrent limit
Minimize the over-current fault,protect normal operation of the inverter
Torque limit & control
"Excavators" characteristics,automatically limit torque during
operation,prevent frequent over-current trip;
Closed loop vector mode can realize the torque control.
Persona
lized
Instantaneous stop
non-stop
When instantaneous power off,voltage reduction is compensated
through load feedback energy,which could make inverter keep running
in a short period of time.
Rapid current limit
To avoid inverter frequent over-current fault.
Virtual IO
5 groups of virtual DI,DO to realize simple logic control
Summary of Contents for HV590 Series
Page 1: ...HV590 Series Frequency Inverter User Manual HNC Electric Limited ...
Page 189: ......
Page 192: ......