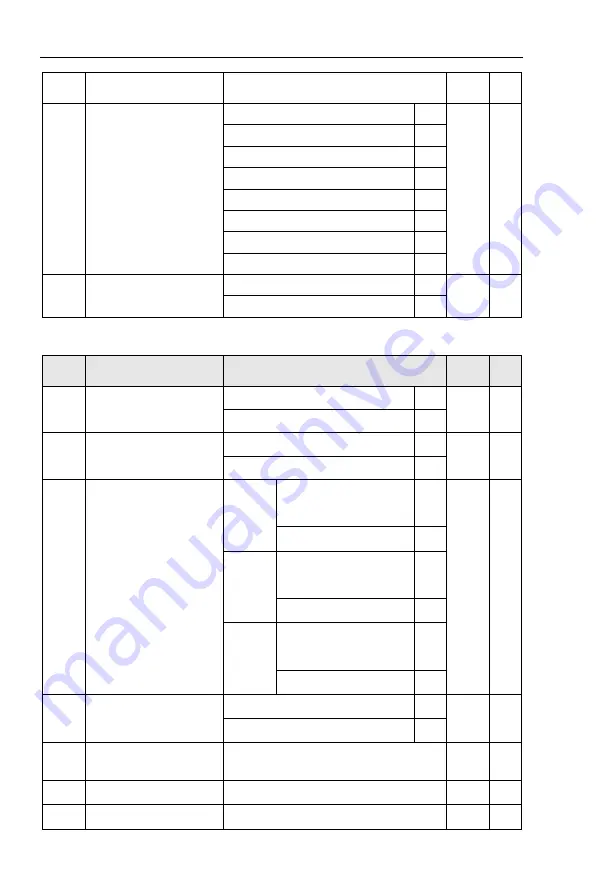
126
Section V.
Parameter Function Table
A7.07
Programmable card torque
setup
-200.0%-200.0%
0.0%
☆
A7.08
Programmable card
command setup
No command
0
0
☆
Forward command
1
Reverse command
2
Forward jog
3
Reverse jog
4
Free stop
5
Decelerate to stop
6
Fault reset
7
A7.09
Programmable card fault
setup
No fault
0
0
☆
Fault code
80-89
5.24 Point to point communication
:
A8.00-8.11
Code
Description/
Keyboard Display
Setting Range
Factory
Setting
Change
Limit
A8.00
Master slave control
function selection
Invalid
0
0
☆
Valid
1
A8.01
Master slave selection
Master
0
0
☆
slave
1
A8.02
Master slave information
exchange
0 bit
Do not follow the Master
command
0
011
☆
follow the Master command
1
10 bit
Do
not
send
fault
information
0
send fault information
1
100 bit
Do not warning when slave
off line
0
warning when slave off line
1
A8.03
Message frame selection
Master slave control frame
0
0
☆
Droop control frame
1
A8.04
Receive data zero
offsettorque
-100.00%
~
100.00%
0.00
★
A8.05
Receive data gain torque
-10.00
~
100.0
1.00
★
A8.06
Communication interrupt
0.0s
~
10.0s
1.0s
☆
Summary of Contents for HV590 Series
Page 1: ...HV590 Series Frequency Inverter User Manual HNC Electric Limited ...
Page 189: ......
Page 192: ......