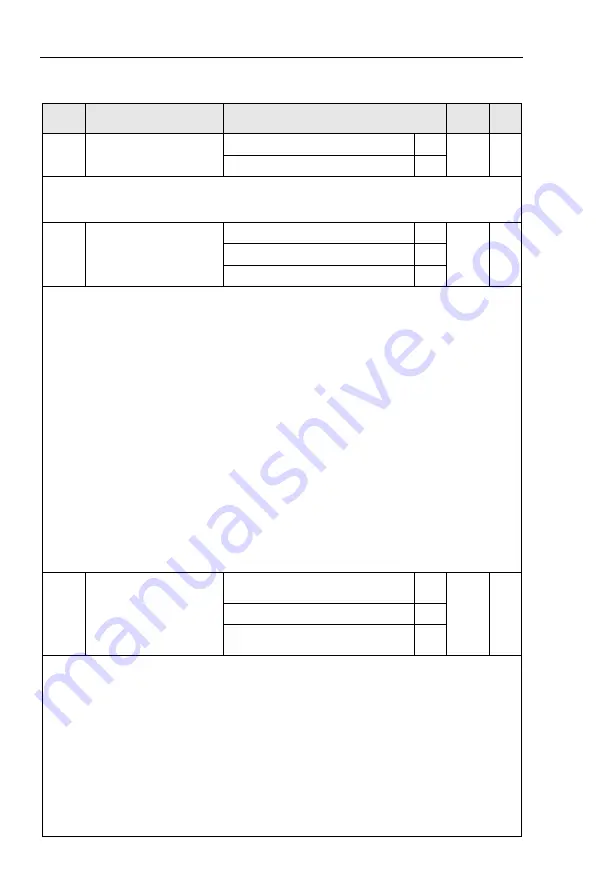
42
Section V.
Parameter Function Table
5.2
Basic function group
:
P0.00-P0.28
Code
Description/Display
Setting Range
Factory
Setting
Change
Limit
P0.00
GP type display
G type(constant torque load type)
1
-
●
P type(draught fan,pump load type)
2
This parameter is only for the use of viewing the factory model. It is can not be modified.
1
:
It is applicable to the constant torque load of specified rated parameter
2
:
It is applicable to the variable torque load of specified rated parameter(draught fan,pump load type)
P0.01
Motor 1 control mode
Speed sensorless vector control(SVC)
0
0
★
Speed sensor vector control(FVC)
1
V/F control
2
0
:
Speed sensorless vector control
It refers to the open-loop vector control that is generally applied to high performance control field. One
inverter can only drive one motor. E.g
:
machine tool, centrifugal machine, fiber drawing machine, injection
molding machine’ load etc.
1
:
Speed sensor vector control
It refers to the closed-loop vector control and encoder must be added to the motor end.Inverter must
be matching with the same type PG card of the encoder. This control mode is suitable for high precision
speed control and torque control field. One inverter can only drive one motor. E.g
:
high speed
papermaking machinery , hoisting machinery , elevator’load etc.
2
:
V/F control
V/F control mode is suitable for fields that load demand is not high or one inverter can drive multiple
motos. E.g
:
draught fan, pump’ load etc.
Tips
:
Motor parameters must be indentified before choosing vector control mode.Only accurate motor
parameters can play the advantage of vector control mode. Users can get better performance by adjusting
speed regulator group P2 parameters(motor 2,motor 3,motor 4 respectively for group A2,A3,A4)
FVC is generally used for permanent magnet synchronous motor, while part of the small power
applications can select V/F control mode. HV590 series support specific models of permanent magnet
synchronous motor sensorless vector control mode. Please refer to HV590 users manual and HV590S
dedicated users manual for using method.
P0.02
Command source selection
Operation panel command channel(LED
off)
0
0
☆
Terminal command channel(LED on)
1
Serial port communicationcommand
channel(LED flashing)
2
Inverter control commands include
:
run, stop, forward rotation (FWD), reverse rotation (REV),
forward jog (FJOG), reverse jog (RJOG), etc.
0
:
Operation panel command channel (“LOCAL/REMOT” LED off);
Perform running command control with RUN, MF.K and STOP/RESET keyson the operation panel.
1
:
Terminal command channel (“LOCAL/REMOT” LED on);
Perform running command control with multifunctional input terminals such as FWD, REV, FJOG,
RJOG, and so on.
2
:
Serial port communication command channel (“LOCAL/REMOT” LED flashing).
The running command is given by the host computer via the communication mode. When the item is
choosen,it must be equipped with communication card(Modbus RTU
、
ProfibusDP card
、
users
programmable control card or CANopen card and so on).
For the communication protocol, please refer to “PD group communication parameters”and
Summary of Contents for HV590 Series
Page 1: ...HV590 Series Frequency Inverter User Manual HNC Electric Limited ...
Page 189: ......
Page 192: ......