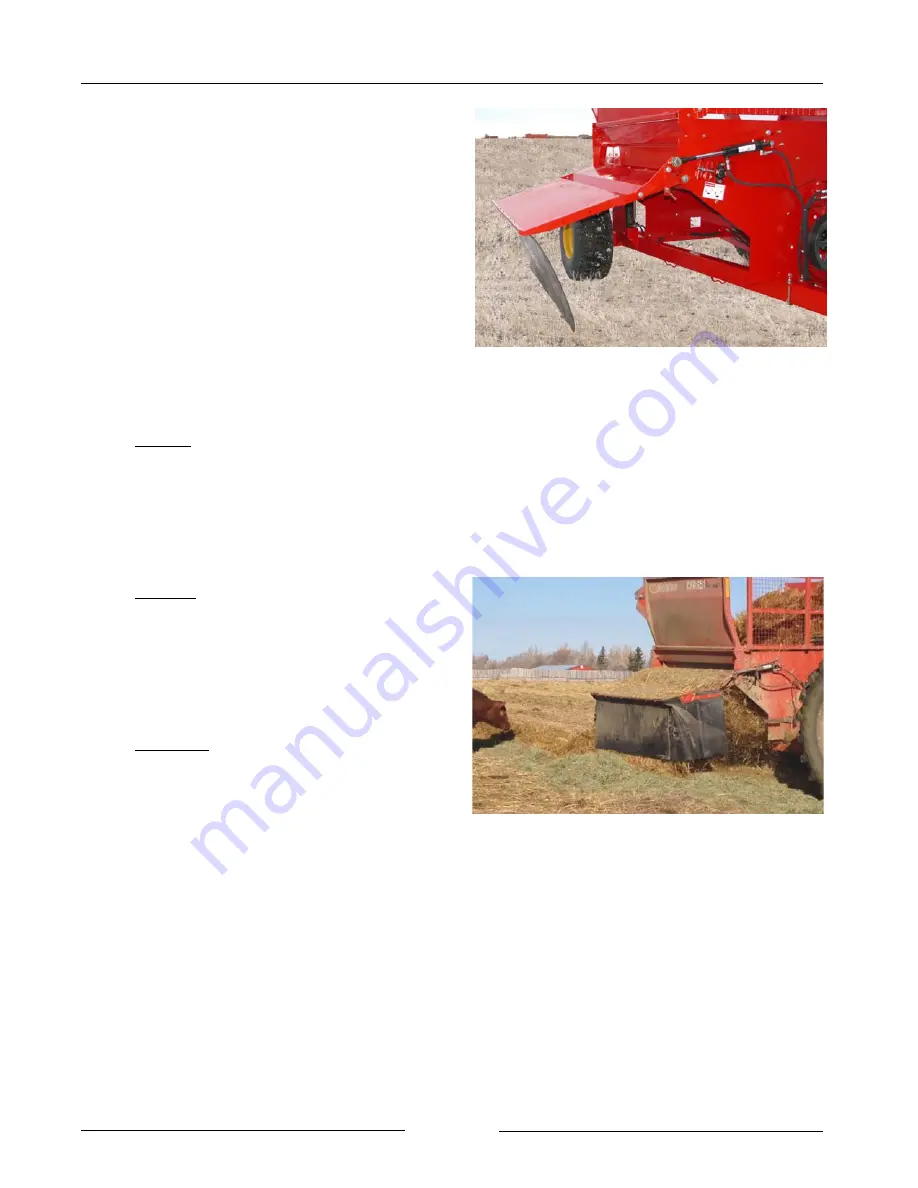
Section 4 - Operating the CFR 651
3. Set the upper deflector door.
-
Raise or lower the upper deflector
door to adjust the amount of
spreading of material.
-
Use the hydraulic cylinder to adjust
the door.
Note: If the 2 remote option is
installed, the door cylinder will be
linked to the bale lift hydraulic circuit
through an electric solenoid
- Move the electric selector valve so
the hydraulic flow goes to the door
cylinder.
Raised - material will be spread out
over a wide area - such as for bedding
materials.
-
Place the rubber deflector into the
tabs on the door.
Midway - deflector door will control the
height and distance of discharged
material.
-
Place the rubber deflector into the
tabs on the door.
Lowered - the material will be left in a
windrow or directed into a feed bunk.
-
Allow the rubber deflector to hang
down.
Set the Upper Deflector Door
(Windrowing Shown)
212005
Windrow Feeding
212121
Page 4-4
Summary of Contents for Bale Pro CFR651
Page 1: ...O p e r a t o r s M a n u a l E12033V3_A Bale Pro Complete Feed Ration CFR651...
Page 7: ...This Page Left Blank...
Page 17: ...Section 1 Safety 216197 SAFETY DECAL LOCATIONS Page 1 10...
Page 43: ...Section 3 Preparing the CFR 651 This Page Left Blank Page 3 18...
Page 71: ...Section 6 Storing the CFR 651 This Page Left Blank Page 6 6...