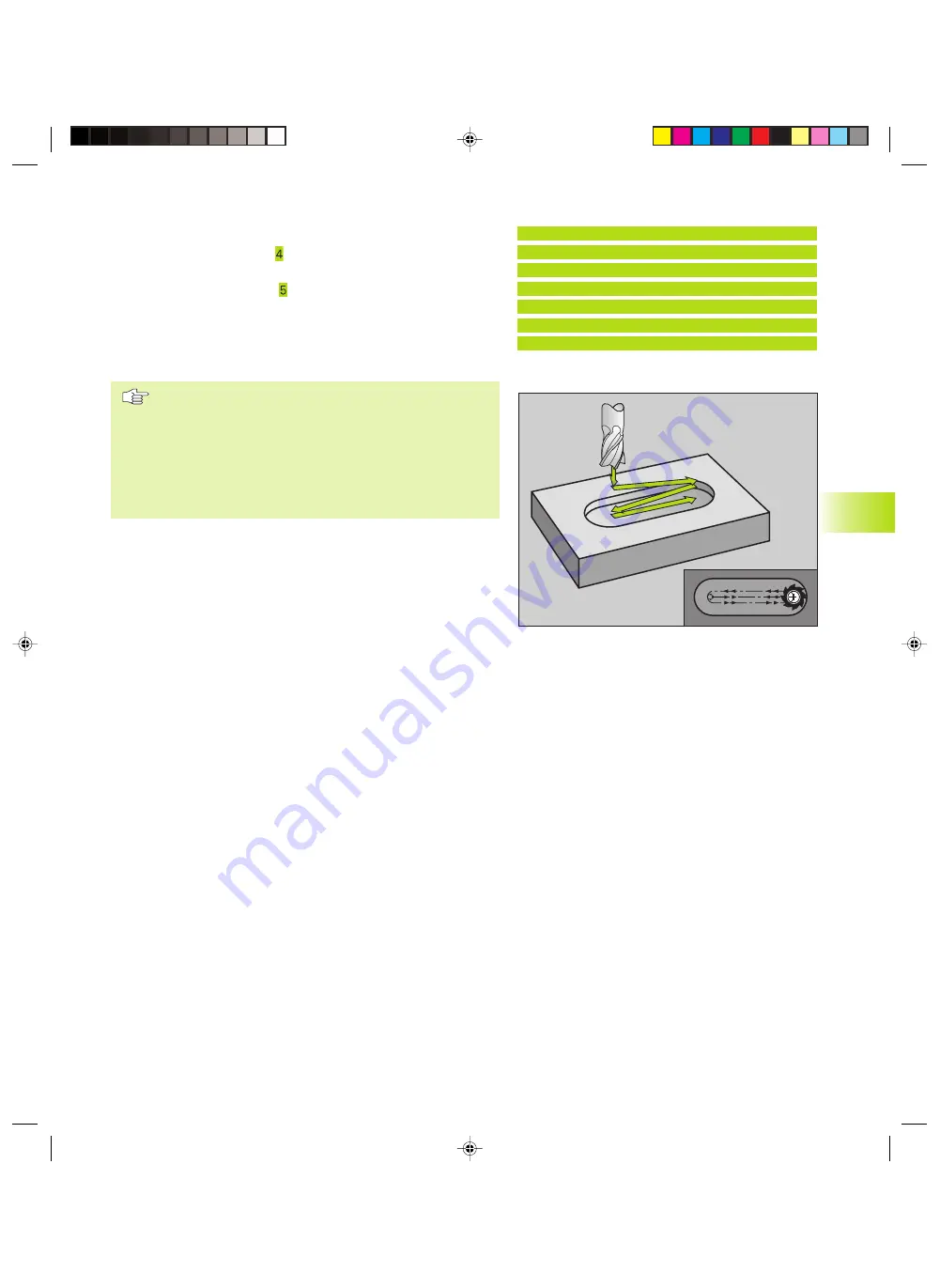
179
HEIDENHAIN TNC 426 B, TNC 430
ú
Feed rate for plunging: Traversing speed of the tool
during penetration
ú
1st side length : Slot length; specify the sign to
determine the first milling direction
ú
2nd side length : Slot width
ú
Feed rate F: Traversing speed of the tool in the
working plane
SLOT with reciprocating plunge-cut (Cycle 210)
Before programming, note the following:
The algebraic sign for the depth parameter determines
the working direction.
The cutter diameter must not be larger than the slot
width and not smaller than a third of the slot width.
The cutter diameter must be smaller than half the slot
length. The TNC otherwise cannot execute this cycle.
Roughing process
1
At rapid traverse, the TNC positions the tool in the tool axis to the
2nd set-up clearance and subsequently to the center of the left
circle. From there, the TNC positions the tool to set-up clearance
above the workpiece surface.
2
The tool moves at the feed rate for milling to the workpiece
surface. From there, the cutter advances in the longitudinal
direction of the slot — plunge-cutting obliquely into the material
— until it reaches the center of the right circle.
3
The tool then moves back to the center of the left circle, again
with oblique plunge-cutting. This process is repeated until the
programmed milling depth is reached.
4
At the milling depth, the TNC moves the tool for the purpose of
face milling to the other end of the slot and then back to the
center of the slot.
Finishing process
5
The TNC advances the tool from the slot center tangentially to
the contour of the finished part. The tool subsequently climb
mills the contour (with M3).
6
When the tool reaches the end of the contour, it departs the
contour tangentially and returns to the center of the slot.
7
At the end of the cycle, the tool is retracted in rapid traverse
FMAX to set-up clearance and — if programmed — to the 2nd
set-up clearance.
8.3 Cy
cle f
or Milling P
o
c
k
ets,
St
uds and Slots
Example NC blocks:
44 CYCL DEF 3.0 SLOT MILLING
45 CYCL DEF 3.1 SET UP 2
46 CYCL DEF 3.2 DEPTH -20
47 CYCL DEF 3.3 PLNGNG 5 F100
48 CYCL DEF 3.4 X+80
49 CYCL DEF 3.5 Y12
50 CYCL DEF 3.6 F275
kkap8.pm6
30.06.2006, 07:03
179
www.EngineeringBooksPdf.com
Summary of Contents for TNC 426 B
Page 3: ...BAUSKLA PM6 30 06 2006 07 03 2 www EngineeringBooksPdf com ...
Page 4: ...BAUSKLA PM6 30 06 2006 07 03 3 www EngineeringBooksPdf com ...
Page 6: ...CINHALT PM6 30 06 2006 07 03 2 www EngineeringBooksPdf com ...
Page 16: ...CINHALT PM6 30 06 2006 07 03 12 www EngineeringBooksPdf com ...
Page 17: ...Introduction 1 Dkap1 pm6 30 06 2006 07 03 1 www EngineeringBooksPdf com ...
Page 29: ...Manual Operation and Setup 2 Dkap2_3 pm6 30 06 2006 07 03 13 www EngineeringBooksPdf com ...
Page 83: ...Programming Tools 5 Fkap5 pm6 30 06 2006 07 03 67 www EngineeringBooksPdf com ...
Page 106: ...Fkap5 pm6 30 06 2006 07 03 90 www EngineeringBooksPdf com ...
Page 107: ...Programming Programming Contours 6 Gkap6 pm6 30 06 2006 07 04 91 www EngineeringBooksPdf com ...
Page 165: ...Hkap7 pm6 30 06 2006 07 03 150 www EngineeringBooksPdf com ...
Page 166: ...Programming Cycles 8 kkap8 pm6 30 06 2006 07 03 151 www EngineeringBooksPdf com ...
Page 253: ...kkap8 pm6 30 06 2006 07 04 238 www EngineeringBooksPdf com ...
Page 265: ...LKAP9 PM6 30 06 2006 07 04 250 www EngineeringBooksPdf com ...
Page 266: ...Programming Q Parameters 10 MKAP10 PM6 30 06 2006 07 04 251 www EngineeringBooksPdf com ...
Page 297: ...MKAP10 PM6 30 06 2006 07 04 282 www EngineeringBooksPdf com ...
Page 298: ...Test Run and Program Run 11 NKAP11 PM6 30 06 2006 07 04 283 www EngineeringBooksPdf com ...
Page 312: ...MOD Functions 12 Okap12 pm6 30 06 2006 07 04 297 www EngineeringBooksPdf com ...
Page 332: ...Tables and Overviews 13 Pkap13 pm6 30 06 2006 07 04 317 www EngineeringBooksPdf com ...