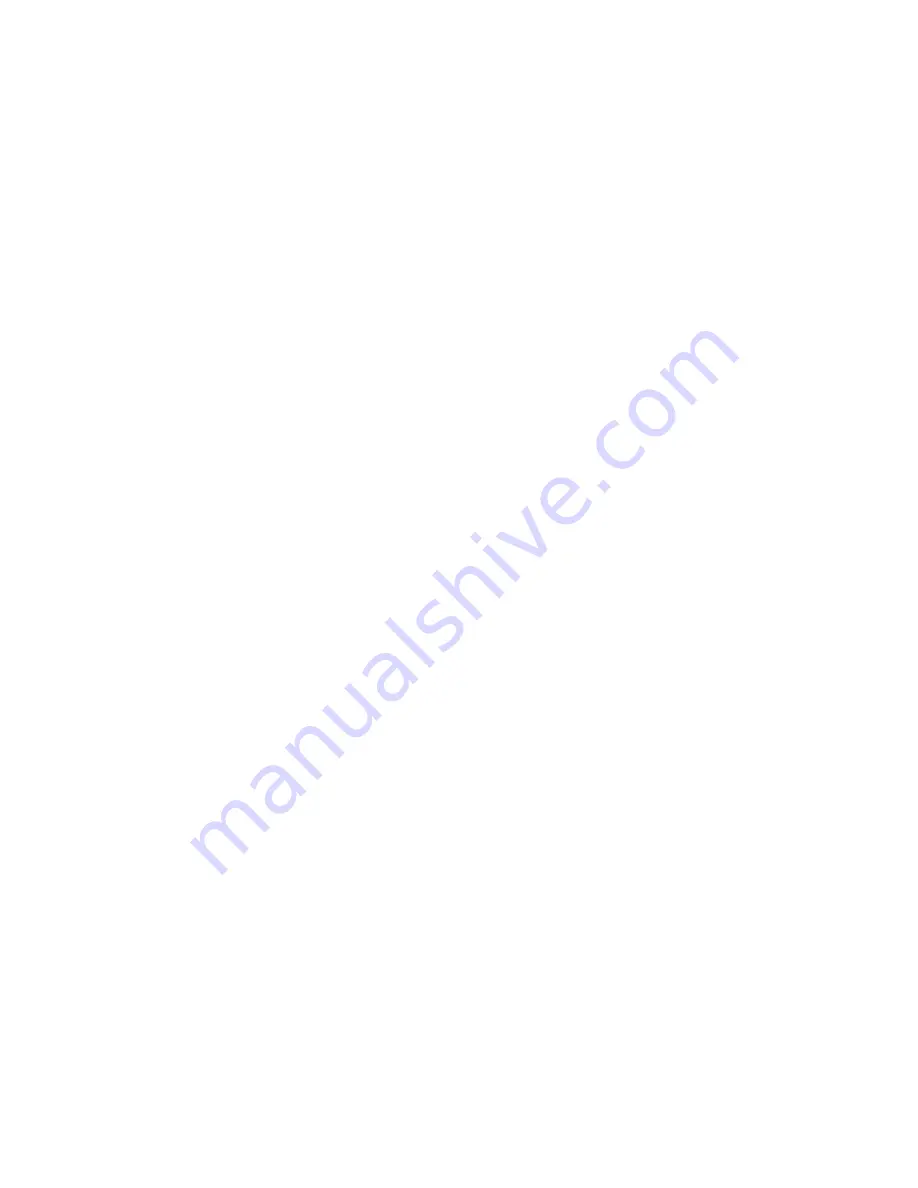
6 - 35
thermal shock, or excess speed and require system
investigation for cause and close inspection of end
cover, commutator, manifold, and rotor set.
7. Remove commutator ring (6). Inspect commutator
ring for cracks or burrs.
8. Remove commutator (5) and seal ring (3). Remove
seal ring from commutator, then discard seal ring.
Inspect commutator for cracks, burrs, wear, or
scoring. If any of these conditions exist, replace
commutator and commutator ring as a matched
set.
9. Remove manifold (7) and inspect for cracks,
surface scoring, or spalling. Replace manifold if
any of these conditions exist. A polished pattern on
the ground surfaces from commutator rotation is
normal. Remove and discard the seal rings (4) that
are on both sides of the manifold.
NOTE: The manifold is constructed of plates bonded
together to form an integral component that is not
disassembled for service. Compare configuration of
both sides of the manifold to ensure that same surface
is assembled against the rotor set.
10.Remove rotor set (8) and wearplate (9) together to
retain the rotor set in its assembled form,
maintaining the same rotor vane (8C) to stator (8B)
contact surfaces. The drive link (10) may come
away from the coupling shaft (12) with the rotor set,
and wearplate. You may have to shift rotor set on
the wearplate to work the drive link out of the rotor
(8A) and wearplate. Inspect the rotor set in its’
assembled form for nicks, scoring, or spalling on
any surface and for broken or worn splines. If the
rotor set requires replacement, the complete rotor
set must be replaced as it is a matched set. Inspect
the wearplate for cracks or scoring. Discard seal
ring (4) that is between the rotor set and wearplate.
NOTE: The rotor set (8) components may become
disassembled during service procedures. Marking the
surface of the rotor and stator that is facing UP, with
etching ink or grease pencil before removal from
Torqmotor will ensure correct reassembly of rotor into
stator and rotor set into Torqmotor. Marking all rotor
components and mating spline components for exact
repositioning at assembly will ensure maximum wear
life and performance of rotor set and Torqmotor.
NOTE: Series ME Torqmotors may have a rotor set
with two stator halves (8B & 8D) with a seal ring (4)
between them and two sets of seven vanes (8C & 8E).
11.Discard seal ring only if stator halves become
disassembled during service procedures.
NOTE: A polished pattern on the wear plate from rotor
rotation is normal.
12.Place rotor set (8) and wear plate (9) on a flat
surface and center rotor (8A) in stator (8B) so that
two rotor lobes (180 degrees apart) and a roller
vane (8C) center-line are on the same stator
center-line. Check the rotor lobe to roller vane
clearance with a feeler gage at this common
centerline. If there is more than .005 inches (0.13
mm) of clearance, replace rotor set.
NOTE: If rotor set (8) has two stator halves (8B & 8D)
and two sets of seven vanes (8C & 8E) as shown in the
alternate construction ME rotor set assembly view,
check the rotor lobe to roller vane clearance at both
ends of rotor.
13.Remove drive link (10) from coupling shaft (12). If it
was not removed with rotor set and wear plate.
Inspect drive link for cracks and worn or damaged
splines. No perceptible play should be noted
between mating spline parts.
14.Remove thrust bearing (11) from top of coupling
shaft (12). Inspect for wear, corrosion and a full
complement of retained rollers.
15.Check exposed portion of coupling shaft (12) to be
sure you have removed all signs of rust and
corrosion which might prevent its withdrawal
through the seal and bearing. Fine emery paper
may be used. Remove key (12A), nut (12B),
washer (12C), bolt (12D), lock washer (12E), or
retaining ring (12F).
16.Remove coupling shaft (12), by pushing on the
output end of shaft. Inspect coupling shaft bearing
and seal surfaces for spalling, nicks, grooves,
severe wear or corrosion and discoloration. Inspect
for damaged or worn internal and external splines
or keyway. Replace coupling shaft if any of these
conditions exist.
NOTE: Minor shaft wear in seal area is permissible. If
diameter wear exceeds .020 inches (0.51 mm), replace
coupling shaft.
NOTE: A slight “polish” is permissible in the shaft
bearing areas. Anything more would require coupling
shaft replacement.
17.Remove and discard seal ring (14) from housing
(18).
18.Remove thrust bearing (15) and thrust washers
(14).
NOTE: ME Torqmotors have a thrust bearing(15)
sandwiched between two thrust washers (14) that
cannot be removed from housing (18) unless bearing
(13) is removed for replacement.
19.Remove seal (16) and back up washer (17)
housing (18). Discard both. To remove seal (16)
back up washer (17) from large Frame Series MB
& ME Torqmotor housing, work them around
unseated thrust washers (14) and thrust bearing
(15) and out of the housing.
20.Remove housing (18) from vise, invert it and
remove and discard seal (20). A blind hole bearing
or seal puller required.
Summary of Contents for 950001
Page 1: ......
Page 11: ......
Page 15: ......
Page 16: ......
Page 19: ......
Page 65: ...8 65...
Page 66: ...8 66...