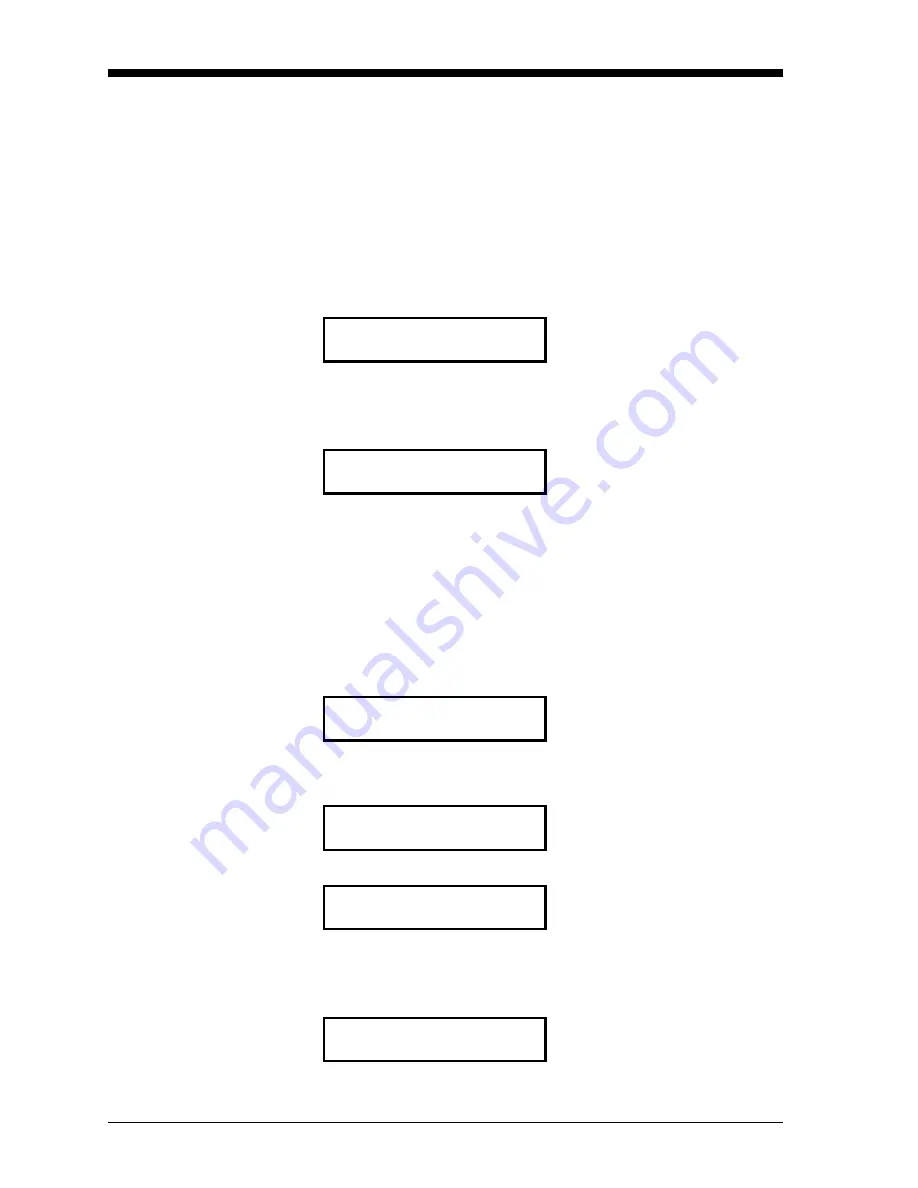
September 2007
3-8
Startup & Operation
Changing the 4-20 mA
Analog Output Range
The XMO2
Calibration Sheet
shipped with the unit lists the 4-20 mA
analog output range that was set at the factory. To change this range
using RS232 digital communication, perform the following steps:
1.
If the XMO2 is not set up for
Easy Menu Entry
, enter the XMO2
Basic Menu
by slowly keying in
[Shift]+[1]
or
[Enter], [1], [2], [3]
.
Refer to the menu map in Figure C-1 on page C-1 for the options
available in this menu.
2.
Press
[N]
repeatedly until the following display appears:
Note:
The
low input value
is the %O
2
in the sample gas that will
generate an analog output current of 4.00 mA.
3.
At the above screen, do one of the following:
•
Press
[Y]
or
[Enter]
to accept the current low input value (0.00 in
the above example). Then, go to Step 5.
•
Use the numeric keys to enter a new low input value (5.00 in
the example that follows). Then, go to Step 4.
4.
If you entered a new low input value:
5.
Continue the procedure as follows:
Note:
The
high input value
is the %O
2
in the sample gas that will
generate an analog output current of 20.00 mA.
BASIC MENU
Press
[Y]
or
[Enter]
to set the low
(4 mA) input value.
Set Low Input Value?
mA Output 4 mA Value
%O2 [0.00]:
mA Output 4 mA Value
Press
[Y]
or
[Enter]
to accept the
new low (4 mA) input value.
%O2 [0.00]:5.00
BASIC MENU
Press
[N]
to move to the next
Basic Menu
option.
Set Low Input Value?
BASIC MENU
Press
[Y]
or
[Enter]
to set the high
(20 mA) input value.
Set High Input Value?
mA Output 20 mA Value
%O2 [100.00]:
Summary of Contents for XMO2
Page 8: ...Chapter 1 ...
Page 18: ...Chapter 2 ...
Page 30: ...Chapter 3 ...
Page 41: ...Chapter 4 ...
Page 52: ...Chapter 5 ...
Page 66: ...Chapter 6 ...
Page 114: ...Chapter 7 ...
Page 146: ...Chapter 8 ...
Page 159: ...Appendix A ...
Page 165: ...Appendix B ...
Page 177: ...Appendix C ...