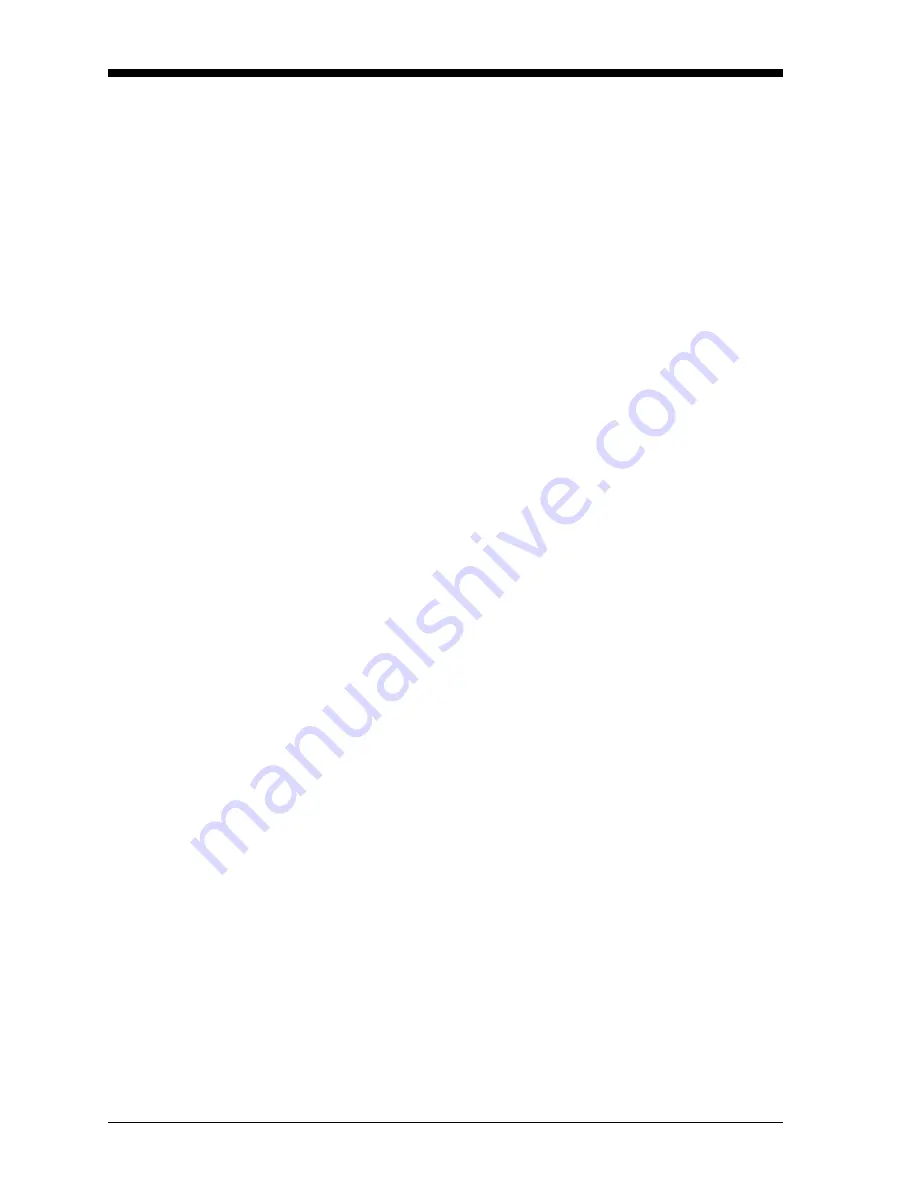
September 2007
A-4
Two Typical Applications
Equipment Used (cont.)
The sample system in Figure A-2 on page A-3 consists of:
•
inlet, outlet, and calibration needle valves
•
a filter/coalescer assembly
•
pressure gauges
•
flowmeters
All components are mounted on a painted steel plate in an enclosure
that is heated to 75±10°F.
Basic Operating
Procedure
The sample system should be mounted as close as possible to the
reactor inlet in order to minimize lag time. Air (20.93% O
2
) is used as
the source of O
2
, and the air/CH
3
OH vapor mixture is sampled at the
reactor inlet. The XMO2 continuously verifies that the optimal
amount of O
2
(typically 9.8%) is present for the reaction to proceed
safely to a maximized yield. Too low an O
2
level will decrease the
yield, while too high an O
2
level will create a safety hazard.
For this application the required calibration gases are:
•
Zero Gas:
N
2
(at least 99.95% pure - 0.0% O
2
)
•
Span Gas:
air (20.93% O
2
)
A typical XMO2
Calibration Sheet
for this application is shown in
Figure 8-1 on page 8-6.
Note:
Any compatible display device may be specified.
Previous Systems
Dumbbell-type paramagnetic O
2
sensors were once commonly used
for this application. However, such systems required extensive
maintenance and frequent manual calibration. In addition, the sensors
were easily damaged by condensable liquids, requiring frequent
sensor replacement. As the XMO2 provides continuous, accurate
monitoring of the reactor feed gas O
2
content with maintenance-free
operation and excellent calibration stability, it is now the system of
choice.
Summary of Contents for XMO2
Page 8: ...Chapter 1 ...
Page 18: ...Chapter 2 ...
Page 30: ...Chapter 3 ...
Page 41: ...Chapter 4 ...
Page 52: ...Chapter 5 ...
Page 66: ...Chapter 6 ...
Page 114: ...Chapter 7 ...
Page 146: ...Chapter 8 ...
Page 159: ...Appendix A ...
Page 165: ...Appendix B ...
Page 177: ...Appendix C ...