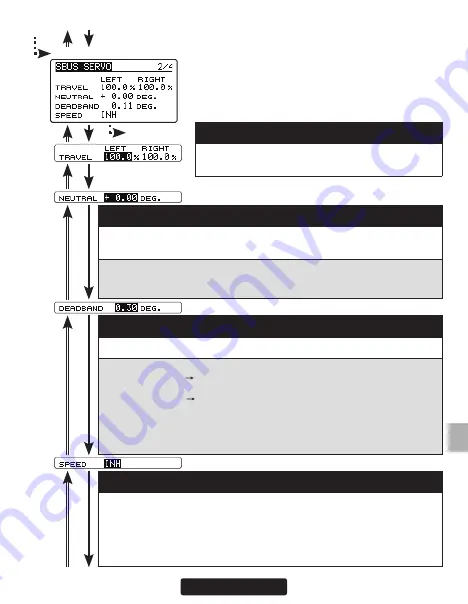
99
SBUS SERVO screen 2/4
From 1/4
Go to 3/4 from any
cursor position
(3) TRAVEL (LEFT / RIGHT)
The left and right travels centered about the neutral
position can be set independently.
(4) NEUTRAL
The neutral position can be changed. When the neutral offset is large
value, the servo's range of travel is restricted on one side.
If the servo CH setting is 1 to 16 CH, you can set it while checking the position
of neutral, but in the case of DG 1 and DG 2, you can not check the position of
neutral.
(6) SPEED
Speeds can be matched by specifying the operating speed. The speed of
multiple servos can be matched without being affected by motor fluctua-
tions. This is effective for load torques below the maximum torque.
However, note that the maximum speed will not exceed what the servo is
capable of even if the servo's operating voltage is increased.
(5) DEADBAND
The dead band angle at stopping can be specified.
[Relationship between dead band set value and servo operation]
Small Value Setting Dead band angle is small and the servo is immediately oper-
ated by a small signal change.
Large Value Setting Dead band angle is large and the servo does not operate at
small signal changes.
Note: If the dead band angle is too small, the servo will operate continuously
and the current consumption will increase and the life of the servo will be
shortened.
Summary of Contents for CGY755
Page 112: ......