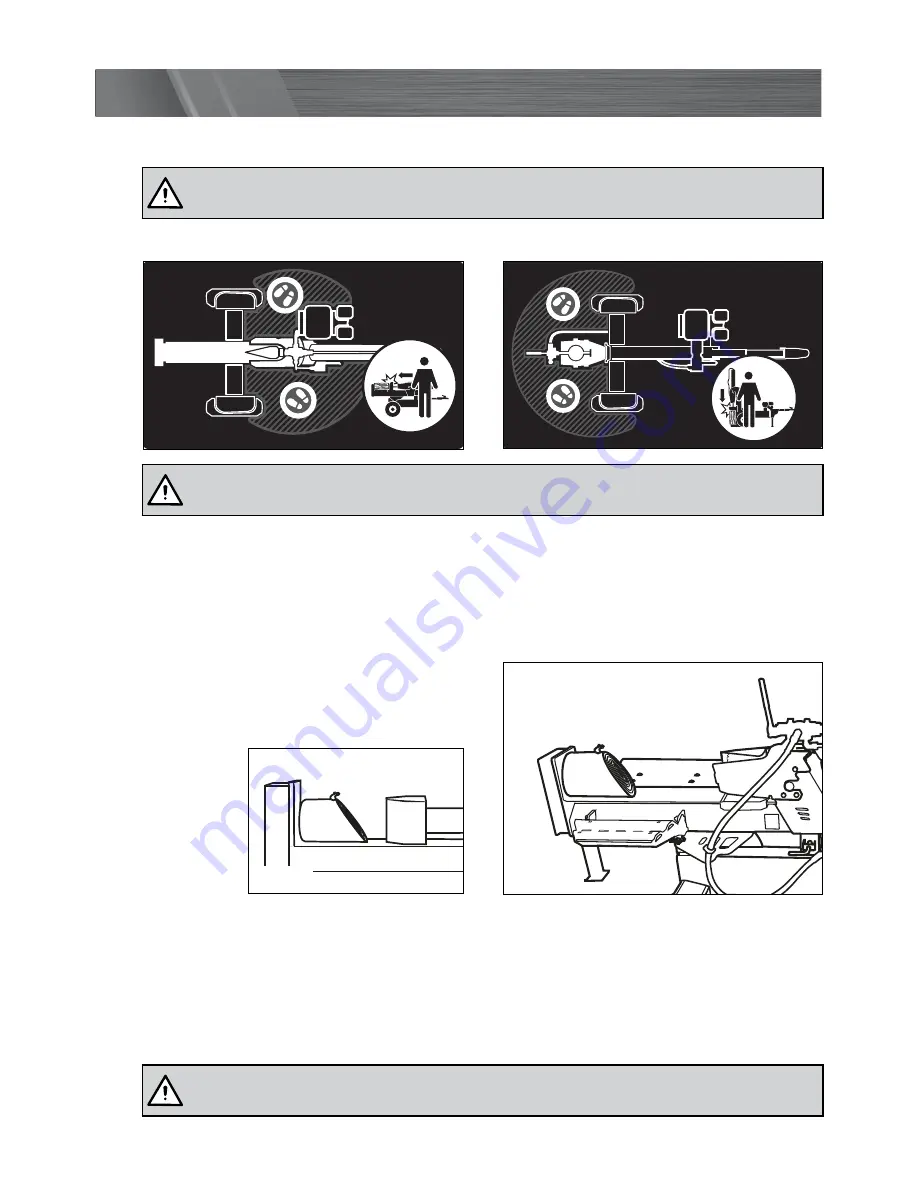
33
Stuck log procedure
If a log does not split completely and becomes stuck on the wedge (18), never attempt to
remove it by modifying the splitter or adding attachments to the splitter. Move the control
lever (1) to the Reverse position and allow the cylinder to retract until the stuck log contacts
the wedge cover guard (17). Continue to retract the cylinder until the log is dislodged from
the wedge (18).
OPERATION (cont.)
IMPORTANT!
Do not use the unit if the wedge cover guard (17) is bent or
damaged. Bent or damaged cover guard must be repaired or replaced before use.
WARNING!
Stand in safe working zone, so feet are not in the path of falling logs.
WARNING!
Do not hold wood in position to be split, with any part of your body
once the control lever is moved into the forward or reverse position.
¥ The splitting operation of the machine is designed to be activated by one person only.
Log placement (fig. 66 & 67)
¥ Load a log onto the beam and against the end plate (15). Log should be cut as square as
possible, to fit properly on the log splitter and against the end plate.
¥ If logs have an uneven end, it is best that
the uneven end is placed towards the
wedge (18), with the log edge facing down.
Horizontal lock latch
Horizontal lock latch
HORIZONTAL OPERATING ZONE
VERTICAL OPERATING ZONE
Fig. 66
Fig. 67