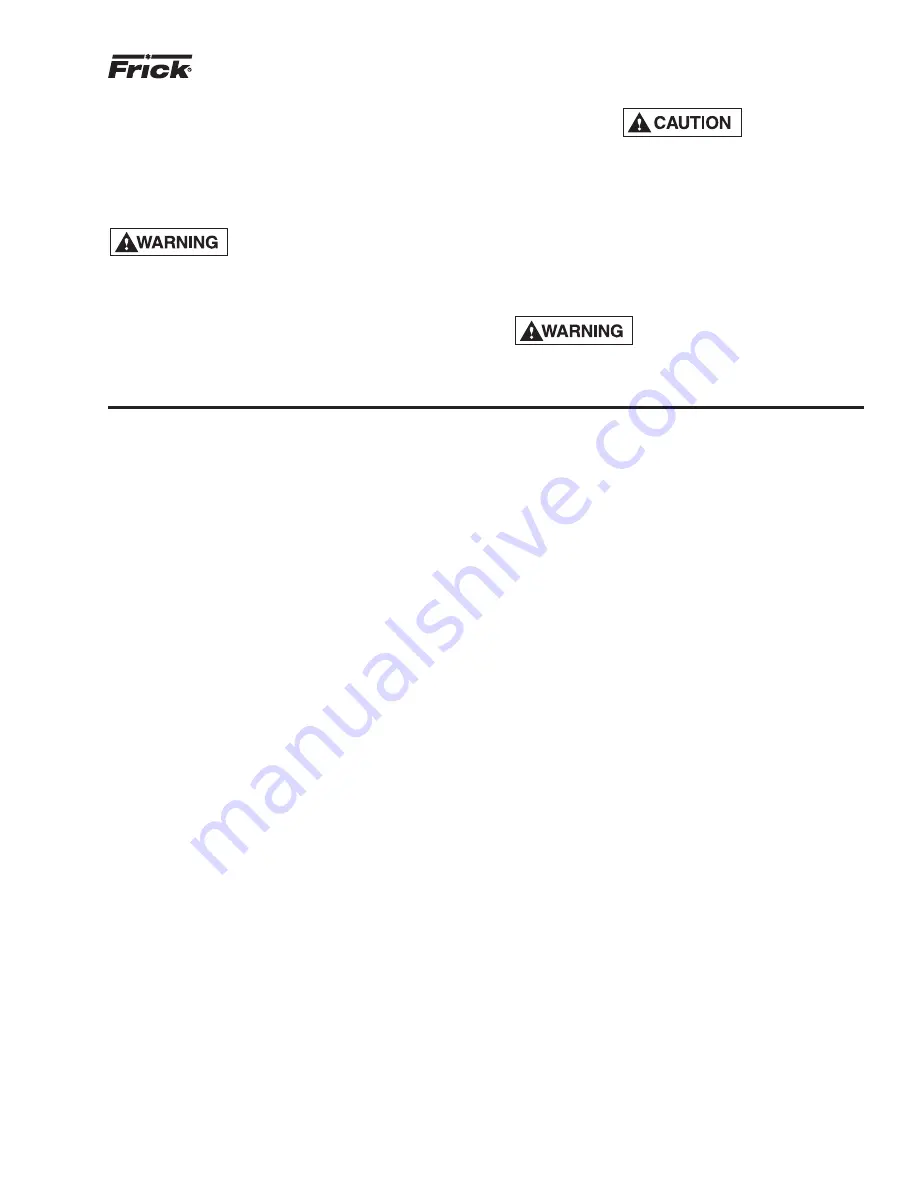
RWB II ROTARY SCREW COMPRESSOR UNITS
MAINTENANCE
S70-200 IOM
Page 25
GENERAL INFORMATION
This section provides instructions for normal main tenance,
a recommended maintenance program, troubleshooting and
correction guides, and typical P and I diagrams. For typical
wiring diagrams and control panel information, consult S90-
010 M (Quantum panel) or S70-200 OM (Plus panel).
THIS SECTION MUST BE READ
AND UN DER STOOD BEFORE AT-
TEMPT ING TO PER FORM ANY
MAIN TENANCE OR SER VICE TO THE UNIT.
NORMAL MAINTENANCE OPERATIONS
When performing maintenance you must take several precau-
tions to ensure your safety:
1. IF UNIT IS RUNNING, PRESS STOP KEY.
2. DISCONNECT POWER FROM UNIT BEFORE PER-
FORM ING ANY MAINTENANCE.
3. WEAR PROPER SAFETY EQUIPMENT WHEN COM-
PRES SOR UNIT IS OPENED TO ATMOSPHERE.
4. ENSURE ADEQUATE VENTILATION.
5. TAKE NECESSARY SAFETY PRE CAU TIONS RE-
QUIRED FOR THE REFRIGERANT BEING USED.
CLOSE ALL COMPRESSOR PACK-
AGE ISOLATION VALVES PRIOR TO
SERVICING THE UNIT. FAILURE TO
DO SO MAY RE SULT IN SERIOUS INJURY.
COMPRESSOR SHUTDOWN and START-UP
For seasonal or prolonged shutdowns the following pro ce dure
should be followed:
1. Reduce the system pressure to the desired condition.
2. Press [STOP] key to cease operation of the compres-
sor.
3. Open disconnect switches for compressor motor and oil
pump starters.
4. Turn on oil heater circuit breaker.
5. Close suction and discharge service valves, also liquid
injection and economizer service valves, if applicable. At-
tach CLOSED TAGS.
6. Shut off cooling water supply valve to oil cooler, if ap-
pli ca ble. Attach CLOSED TAG.
7. Protect oil cooler from ambient temperatures below freez-
ing or remove water heads.
To start-up after a seasonal or prolonged shutdown the fol-
low ing procedure should be followed:
1. Any water necessary for the operation of the system that
may have been drained or shut off should be restored and
turned on. If oil cooler heads were removed, reinstall and
remove tags.
2. Open suction and discharge service valves, also liquid
injection and economizer service valves, if applicable. Re-
move tags.
3. Close disconnect switches for compressor, motor and oil
pump starters.
4. Turn off oil heater circuit breaker.
5. Perform checkpoints on prestart check list, then start
unit.
GENERAL MAINTENANCE
Proper maintenance is important in order to assure long and
trouble-free service from your screw compressor unit. Some
areas critical to good compressor operation are:
1. Keep refrigerant and oil clean and dry, avoid moisture
con tam i na tion. After servicing any portion of the refrigera-
tion system, evacuate to remove moisture before returning
to service. Water vapor condensing in the compressor while
running, or more likely while shut down, can cause rusting
of critical components and reduce life.
2. Keep suction strainer clean. Check periodically, par ticularly
on new systems where welding slag or pipe scale could
fi nds it way to the compressor suction. Excessive dirt in the
suc tion strainer could cause it to collapse, dumping particles
into the compressor.
3. Keep oil fi lters clean. If fi lters show increasing pressure
drop, indicating dirt or water, stop the compressor and change
fi lters. Running a compressor for long periods with high fi lter
pressure drop can starve the compressor for oil and lead to
premature bearing failure.
4. Avoid slugging compressor with liquid refrigerant. While
screw compressors are probable the most tolerant to in-
ges tion of some refrigerant liquid of any compressor type
avail able today, they are not liquid pumps. Make certain
to main tain adequate superheat and properly size suction
ac cu mu la tors to avoid dumping liquid refrigerant into com-
pressor suction.
Keep liquid injection valves properly adjusted and in good
condition to avoid fl ooding compressor with liquid. Liquid can
cause a reduction in compressor life and in extreme cases
can cause complete failure.
5. Protect the compressor during long periods of shut down.
If the compressor will be setting for long periods without run-
ning it is ad vis able to evacuate to low pressure and charge
with dry nitrogen or oil, particularly on systems known to
contain water vapor.
6. Preventive maintenance inspection is recommended any
time a compressor exhibits a noticeable change in vibra tion
level, noise or performance.