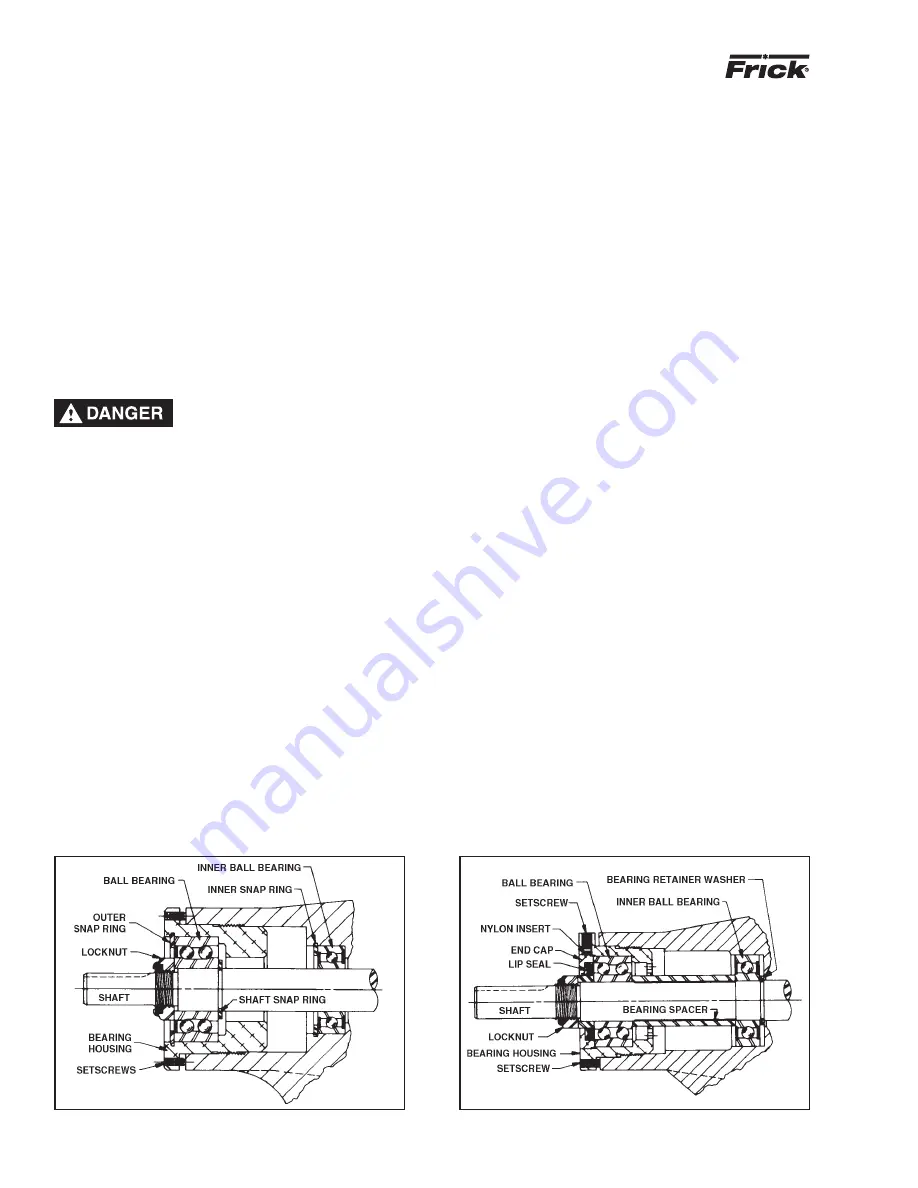
RWB II ROTARY SCREW COMPRESSOR UNITS
MAINTENANCE
S70-200 IOM
Page 28
11. Add oil by attaching a suitable pressure-type hose to
the oil-charging valve located on top of the separator. Us ing
a pressure-type oil pump and recommended Frick oil, open
the charging valve and fi ll the separator until the oil level is
midway in the top sight glass. NOTE: Fill slowly because
the oil will fi ll up in the separator faster than it shows in the
sight glass. Refer to the ta ble in the OIL CHARGE sec tion
for ap prox i mate oil charge quan ti ties.
12. Open the suction and discharge service valves, and
also the liquid injection and economizer service valves, if
ap pli ca ble.
13. Close the disconnect switch for the compressor motor
start er.
14. Start the unit.
DEMAND PUMP DISASSEMBLY
BEFORE OPENING ANY VIKING
PUMP LIQUID CHAM BER (PUMP-
I N G C H A M B E R , R E S E RVO I R ,
JACK ET, ETC.) ENSURE:
1. THAT ANY PRESSURE IN THE CHAMBER HAS BEEN
COM PLETE LY VENTED THROUGH SUC TION OR DIS-
CHARGE LINES OR OTHER AP PRO PRI ATE OPEN INGS
OR CON NEC TIONS.
2. THAT THE DRIVING MEANS (MOTOR, TURBINE,
EN GINE, ETC.) HAS BEEN “LOCKED OUT” OR MADE
NON OPERATIONAL SO THAT IT CANNOT BE START ED
WHILE WORK IS BEING DONE ON THE PUMP.
FAILURE TO FOLLOW ABOVE LISTED PRE CAU TION ARY
MEASURES MAY RE SULT IN SERIOUS INJURY OR
DEATH.
1. Mark head and casing before disassembly to ensure
prop er reassembly. Position the idler pin, which is offset in the
pump head, up and equal distance be tween port con nec tions
to allow for proper fl ow of liquid through the pump.
2. Remove the head capscrews.
3. Tilt top of head back when removing to prevent idler
from falling off idler pin.
4. Remove idler and bushing assembly. If idler bush-
ing needs replacing, see INSTALLATION OF CARBON
GRAPH ITE BUSHINGS.
f
Figure 26 - Thrust-Bearing assembly (GG, HJ, HL)
Figure 27 - Thrust-Bearing assembly (AS, AK, AL)
5. Insert a brass bar or piece of hardwood in the port open-
ing and between rotor teeth to keep shaft from turning. Turn
the locknut coun ter clock wise and remove locknut. See Fig ure
26 or 27.
6. Loosen two setscrews in face of bearing housing and
turn thrust bearing assembly counterclockwise and re move
from casing. See Figure 26 or 27.
7. GG, HJ, HL: Remove snap ring from shaft. See Figure
26. AS, AK, AL: Remove bearing spacer from shaft. See
Fig ure 27.
8. Remove brass bar or piece of hard wood from port open-
ing.
9. The rotor and shaft can now be re moved by tap ping on end
of shaft with a lead ham mer or, if using a reg u lar ham mer, use
a piece of hardwood be tween shaft and hammer. The rotary
member of the seal will come out with rotor and shaft.
10. AS, AK, AL: Remove bearing retainer washer. The
wash er may have stayed with rotor and shaft when re moved
or is against ball bearing. See Fig ure 27.
11. Remove the mechanical seal rotary member and spring
from rotor and shaft assembly.
12. GG, HJ, HL: Remove inner snap ring and single-row ball
bearing from casing.
AS, AK, AL: Remove single-row ball bearing from casing.
13. Remove seal seat or stationary part of seal from
cas ing.
14. Disassemble thrust-bearing assembly.
GG, HJ, HL: Remove outer snap ring from bearing hous ing
and remove ball bearing. See Figure 26.
AS, AK, AL: Loosen two set screws in fl ange out side di-
am e ter. Rotate end cap and lip seal coun ter clock wise and
re move. Remove ball bearing. See Figure 27.
The casing should be examined for wear, par tic u lar ly in the
area between ports. All parts should be checked for wear
before pump is put together.
When making major repairs, such as replacing a rotor and
shaft, it is advisable to also install a new mechanical seal,
head and idler pin, idler, and bush ing. See INSTALLATION
OF CARBON GRAPH ITE BUSHINGS.