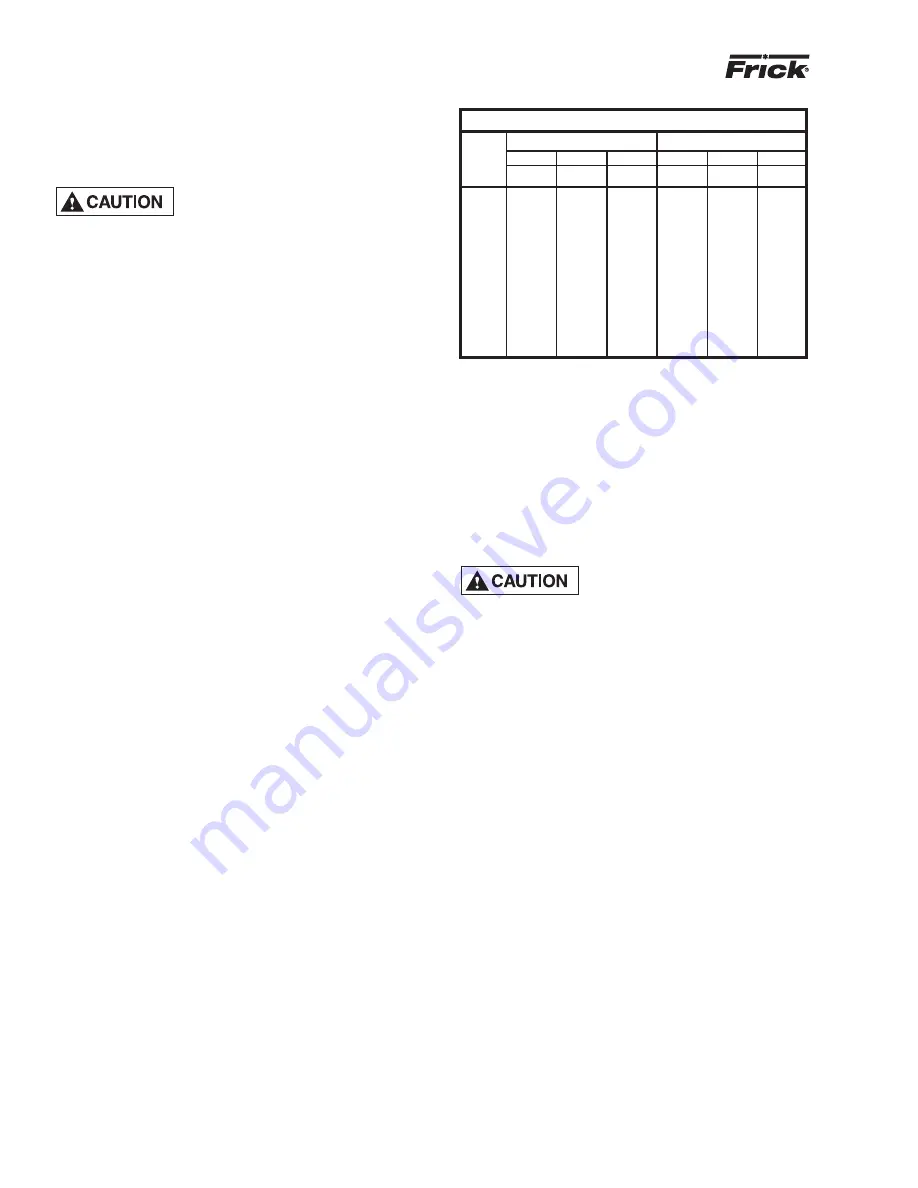
RWB II ROTARY SCREW COMPRESSOR UNITS
INSTALLATION
S70-200 IOM
Page 4
ALLOWABLE FLANGE LOADS
NOZ.
MOMENTS
(ft-lbf)
LOAD
(lbf)
SIZE AXIAL VERT. LAT. AXIAL VERT. LAT.
NPS
M
R
M
C
M
L
P V
C
V
L
1 25 25 25 50 50 50
1.25 25 25 25 50 50 50
1.5 50 40 40
100 75 75
2 100 70 70
150
125
125
3 250 175 175 225 250 250
4 400 200 200 300 400 400
5 425 400 400 400 450 450
6 1000 750 750 650 650 650
8 1500 1000 1000 1500 900 900
10 1500 1200 1200 1500 1200 1200
12 1500 1500 1500 1500 1500 1500
14 2000 1800 1800 1700 2000 2000
FOUNDATION
Each RWB II Rotary Screw Compressor Unit is shipped
mount ed on a wood skid which must be removed prior to unit
installation.
Allow space for ser vic ing both ends
of the unit. A min i mum of 36 inches
is rec om mend ed.
The fi rst requirement of the compressor foundation is that it
must be able to support the weight of the compressor pack-
age in clud ing coolers, oil, and refrigerant charge. Screw
com pres sors are capable of converting large quantities of
shaft power into gas compression in a relatively small space
and a mass is required to effectively dampen these rel a tive ly
high frequency vibrations.
Firmly anchoring the compressor package to a suitable
foun da tion by proper application of grout and elimination of
pip ing stress imposed on the compressor is the best insur-
ance for a trouble free installation. Use only the certifi ed
general ar range ment draw ings from Frick Co. to determine
the mount ing foot locations and to allow for recommended
clear anc es around the unit for ease of operation and servic-
ing. Foun da tions must be in com pli ance with local building
codes and materials should be of industrial quality.
The fl oor should be a minimum of 6 inches of reinforced con-
crete and housekeeping pads are recommended. An chor
bolts are required to fi rmly tie the unit to the fl oor. Once the
unit is rigged into place (See RIGGING and HANDLING),
the feet must then be shimmed in order to level the unit. The
shims should be placed to position the feet roughly one inch
above the house keep ing pad to allow room for grout ing. An
ex pan sion-type ep oxy grout must be worked under all areas
of the base with no voids and be allowed to settle with a slight
out ward slope so oil and water can run off of the base.
When installing on a steel base, the following guidelines
should be implemented to properly design the system base:
1. Use I-beams in the skid where the screw compressor will
be attached to the system base. They should run parallel to
the package feet and support the feet for their full length.
2. The compressor unit feet should be continuously welded to
the system base at all points of contact.
3. The compressor unit should not be mounted on vibration
iso la tors in order to hold down package vibration levels.
4. The customer’s foundation for the system base should ful ly
support the system base under all areas, but most cer tain ly
un der the I-beams that support the compressor pack age.
When installing on the upper fl oors of buildings, extra pre cau -
tions should be taken to prevent normal package vi bra tion
from being transferred to the building structure. It may be
necessary to use rubber or spring isolators, or a com bi na tion
of both, to prevent the transmission of compressor vibration
directly to the structure. However, this may in crease package
vibration levels because the compressor is not in contact with
any damping mass. The mounting and support of suction
and discharge lines is also very important. Rub ber or spring
pipe supports may be required to avoid ex cit ing the building
structure at any pipe supports close to the compressor pack-
age. It is best to employ a vibration ex pert in the design of
a proper mounting arrangement.
In any screw compressor installation, suction and dis charge lines
should be supported in pipe hangers (preferably with in 2 ft. of
vertical pipe run) so that the lines won’t move if dis con nect ed
from the compressor. See table for Allowable Flange Loads.
A licensed architect should be consulted to determine the
prop er foundation requirements for any large engine or
tur bine drive.
When applying screw compressors at high pressures, the
customer must be pre pared for package vibration and noise
higher than the values predicted for normal refrigeration duty.
Proper foundations and proper installation methods are vi tal;
and even then, sound attenuation or noise curtains may be
required to reduce noise to desired levels.
For more detailed information on Screw Compressor Foun-
da tions, please request Frick publication S70-210 IB.
RIGGING and HANDLING
THIS SCREW COM
PRES SOR
PACK AGE MAY BE TOP-HEAVY.
USE CAU TION IN RIGGING AND
HAN DLING.
The unit can be moved with rigging, using a crane or forklift,
by hooking into the four lifting eyes on the com pressor and
motor bases. If no motor is mounted, the lifting ring should
be moved to the compressor side of the center of the unit
because 60 percent of the weight is toward the compressor
end. If a motor is mounted ap propriate adjustment in the lift-
ing point should be made to compensate for motor weight.
Adjustment of the lifting point must also be made for any
additions to the standard package such as an external oil
cooler, etc., as the center of balance will be effected.
The unit can be moved with a forklift by forking under the skid,
or it can be skidded into place with pinch bars by push ing
against the skid. NEVER MOVE THE UNIT BY PUSH ING
OR FORKING AGAINST THE SEPARAT OR SHELL OR ITS
MOUNTING SUPPORTS.
SKID REMOVAL
If the unit is rigged into place the skid can be removed
by taking off the nuts and bolts that are fastening the unit
mount ing supports to the skid before lowering the unit onto
the mounting surface.
If the unit is skidded into place remove the cross mem bers
from the skid and remove the nuts anchoring the unit to the
skid. Using a 5 ton jack under the separator raise the unit at the
compressor end until it clears the two mounting bolts. Spread
the skid to clear the unit mounting support, then low er the unit
to the surface. Repeat proced ure on opposite end.