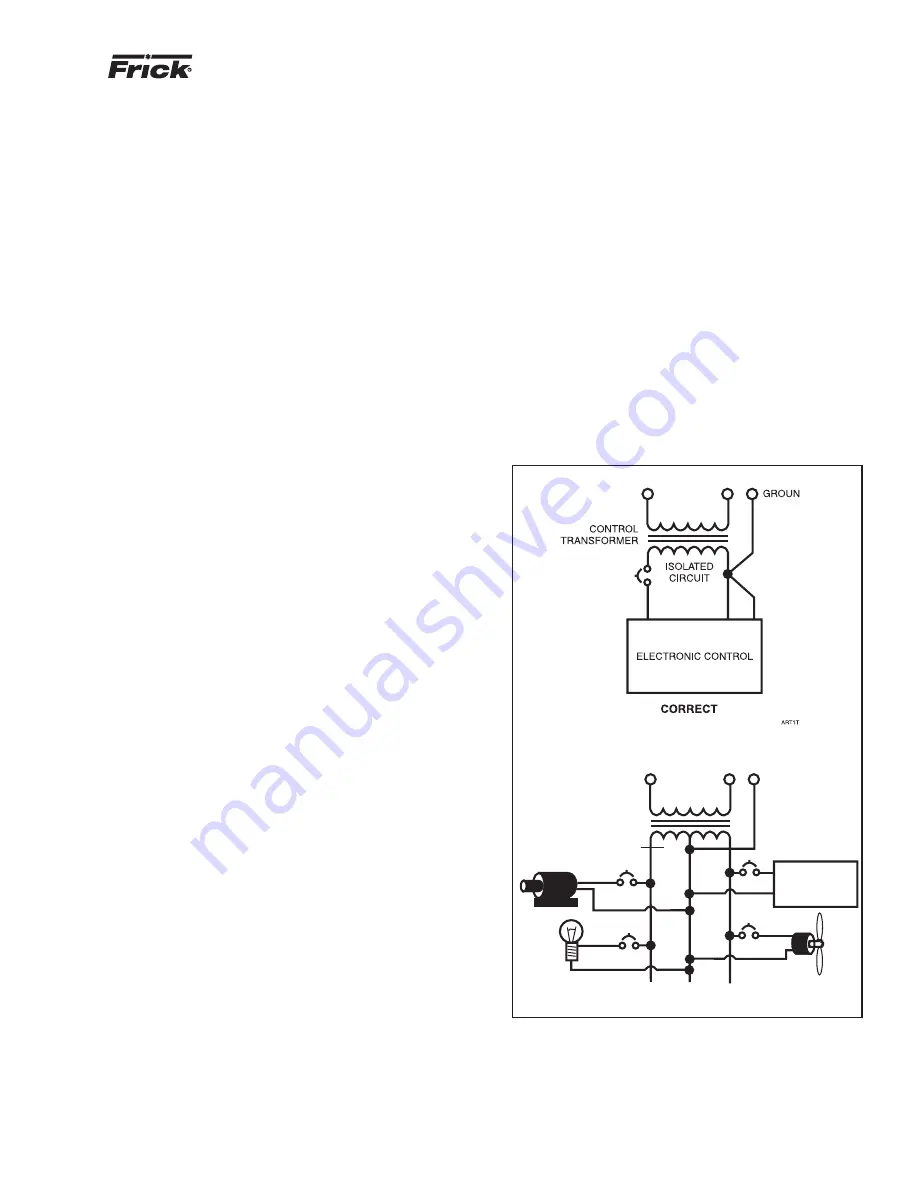
RWB II ROTARY SCREW COMPRESSOR UNITS
PROPER IN STAL LA TION OF ELECTRONIC EQUIPMENT
S70-200 IOM
Page 47
PROPER INSTALLATION OF ELECTRONIC EQUIPMENT
IN AN IN DUS TRI AL ENVIRONMENT
In today’s refrigeration plants, electronic controls have found
their way into almost every aspect of refrigeration control.
Electronic con trols have brought to the industry more pre cise
con trol, im proved energy savings and operator con ve nienc es.
Electronic control devices have rev o lu tion ized the way refrig-
eration plants operate to day.
The earlier relay systems were virtually immune to radio
fre quen cy interference (RFI), electromagnetic interference
(EMI), and ground loop cur rents. Therefore in stal la tion and
wiring were of little con se quence and the wiring job con-
sist ed of hook ing up the point-to-point wiring and sizing the
wire properly. In an electronic system, im prop er in stal la tion
will cause problems that out weigh the benefi ts of electronic
con trol. Electronic equip ment is susceptible to RFI, EMI, and
ground loop currents which can cause equipment shut downs,
processor memory and program loss, er rat ic be hav ior, and
false readings. Manufacturers of in dus tri al elec tron ic equip-
ment take into con sid er ation the effects of RFI, EMI, and
ground loop currents and incorporate pro tec tion of the
elec tron ics in their designs. These man u fac tur ers re quire
that certain installation precautions be tak en to pro tect the
elec tron ics from these ef fects. All electronic equip ment must
be viewed as sen si tive instrumentation and there fore re quires
care ful attention to installation procedures. These pro ce dures
are well known to instrument engineers, but are usu al ly not
followed by general elec tri cians.
There are a few basics, that if followed, will result in a
trou ble-free installation. The Na tion al Electric Code (NEC)
is a guide line for safe wiring practices, but it does not deal
with pro ce dures used for electronic control in stal la tion. Use
the fol low ing procedures for elec tron ic equip ment in stal -
la tion. These pro ce dures do not over ride any rules by the
NEC, but are to be used in con junc tion with the NEC code.
WIRE SIZING
Size supply wires one size larger than re quired for
am per age draw to reduce in stan ta neous volt age dips
caused by large loads such as heat ers and contactors
and so le noids. These sud den dips in volt age can cause the
pro ces sor, whether it be a mi cro pro ces sor, a com put er, or a
PLC to malfunction mo men tari ly or cause a com plete reset
of the control system. If the wire is loaded to its max i mum
ca pac i ty, the volt age dips are much larger, and the potential
of a mal func tion is very high. If the wire is sized one size
larg er than required, the voltage dips are smaller than in a
fully loaded supply wire, and the po ten tial for mal func tion
is much lower. The NEC code book calls for spe cifi c wire
sizes to be used based on cur rent draw. An ex am ple of this
would be to use #14 gauge wire for circuits up to 15 amp or
#12 gauge wire for circuits of up to 20 amp. There fore, when
con nect ing the power feed circuit to an elec tron ic in dus tri al
con trol, use #12 gauge wire for a maximum cur rent draw
of 15 amp and #10 wire for a max i mum cur rent draw of 20
amp. Use this rule of thumb to minimize volt age dips at the
elec tron ic control.
VOLTAGE SOURCE
Selecting the voltage source is extremely im por tant for
prop er operation of elec tron ic equip ment in an in dus tri al en-
vi ron ment. Standard pro ce dure for electronic in stru men ta tion
is to pro vide a “clean” separate source volt age in order to
pre vent EMI, from other equipment in the plant, from in ter -
fer ing with the operation of the electronic equipment. Con-
nect ing electronic equip ment to a breaker panel (also known
as light ing panels and fuse panels) sub jects the electronic
equip ment to noise gen er at ed by other devices con nect ed
to the breaker panel. This noise is known as elec tro mag net ic
in ter fer ence (EMI). EMI fl ows on the wires that are common
to a circuit. EMI can not travel eas i ly through trans form ers
and there fore can be isolated from selected cir cuits. Use
a con trol transformer to isolate the elec tron ic con trol
pan el from other equip ment in the plant that gen er ate
EMI. (Figure 44)
CONTROL
TRANSFORMER
NONISOLATED
CIRCUIT
GROUND
ELECTRONIC
CONTROL
INCORRECT
ART1B
Figure 44