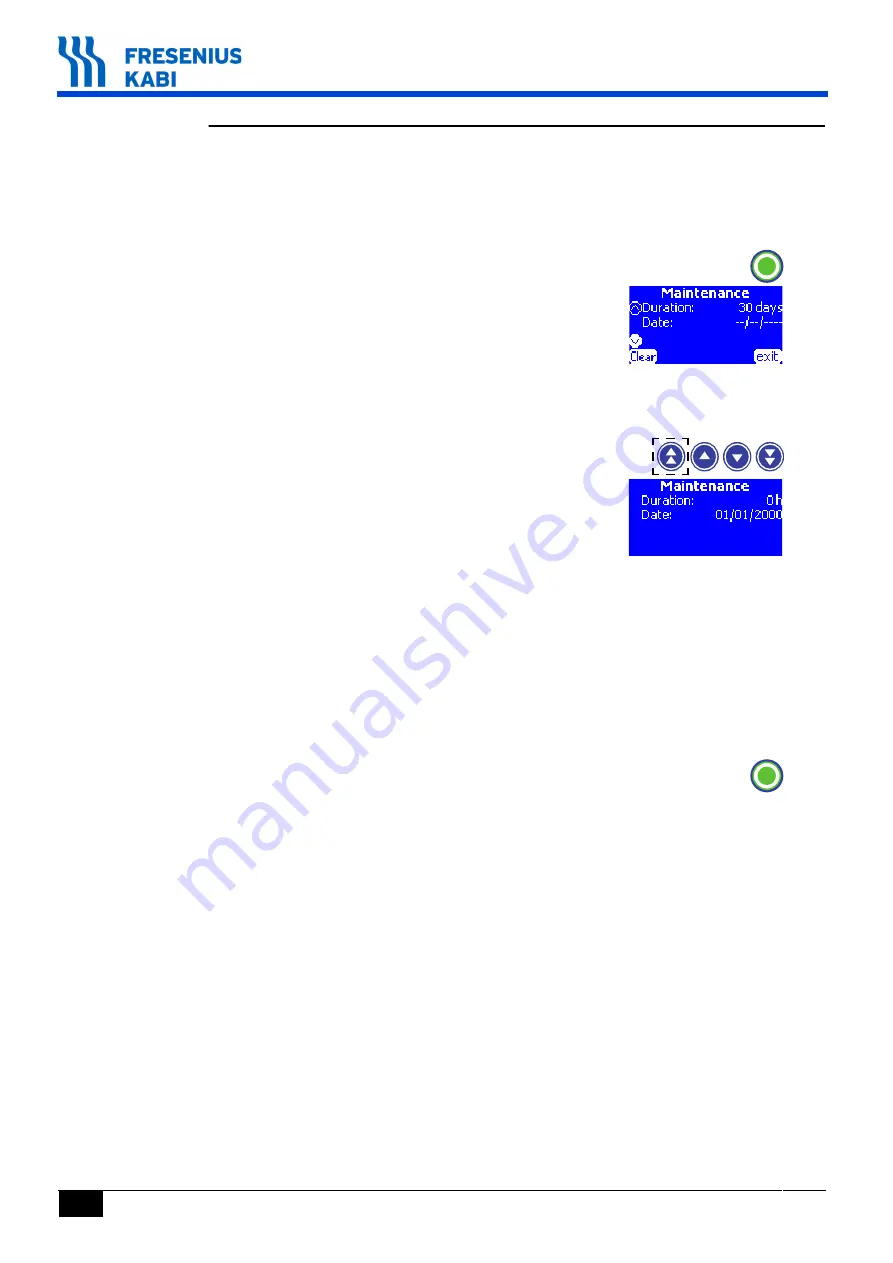
36
va04.3_001g_Eng.fm
Ma
in
te
na
nc
e pr
év
en
tive
4.4.4 Test 2, Maintenance
This test displays:
the running time since the last maintenance service in hours, days or months
the date of the last maintenance service
the total running time in hours, days or months and the number of cycles
executed by the pumping unit.
Test 2
, press "enter".
The main "
Maintenance
" menu displays.
Scroll through the information using the selection keys.
Choose between the proposed options "Reset"
or "Exit".
"RAZ", using the left selection key.
The following "
Maintenance
" menu displays.
For this menu:
Running time
:
the number of operating hours is reset to "0".
Date
:
the date of the last maintenance is reset to the day’s date.
Total running time
:
the total running time since the beginning remains
incremented.
Total distance:
the number of cycles executed since the start remains
incremented.
"Exit"
,
leaves the screen and allows to return to the "
Test
" menu.
Summary of Contents for Volumat Agilia
Page 1: ...0 9 C E S Volumat Agilia Technical Manual ...
Page 6: ...66 TM_Volumat_Agilia_Eng_TDM fm ...
Page 8: ...8 va01_001e_Eng fm Introduction 1 2 Operation diagram ...
Page 12: ...12 va01_001e_Eng fm Introduction ...
Page 26: ...26 va02_001e_Eng fm Description and operation ...
Page 30: ...30 va03 1_001e_Eng fm Description of the menus ...
Page 62: ...62 va04 4_001e_Eng fm Preventive maintenance ...
Page 70: ...70 va05 1_001e_Eng fm Troubleshooting ...
Page 76: ...76 va06 0_001g_Eng fm Intervention procedures ...
Page 82: ...82 va06 0_0011g_Eng fm Intervention procedures ...
Page 86: ...86 va06 0_0021g_Eng fm Intervention procedures ...
Page 94: ...94 va06 0_0040g_Eng fm Fiches d intervention ...
Page 104: ...104 va06 0_0060g_Eng fm Fiches d intervention ...
Page 110: ...110 va06 0_0070g_Eng fm Fiches d intervention ...
Page 134: ...134 va07 1_001g_Eng fm Calibrations ...
Page 136: ...136 va08 0_001d_Eng fm Spare parts catalogue ...