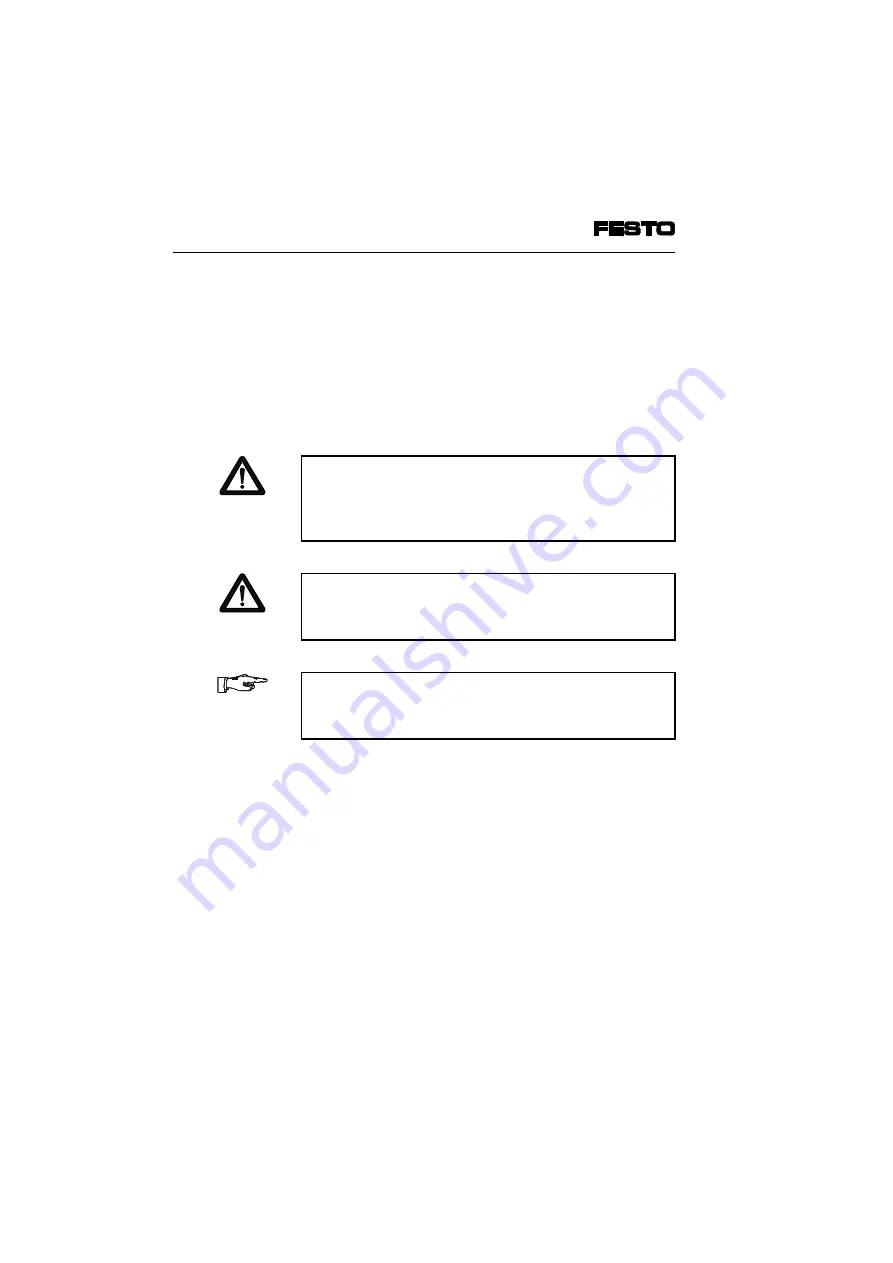
Important user instructions
This manual contains instructions on the dangers which
may occur if the CP system is not used correctly. These
instructions are always printed in italics, are framed and
also signalled by a pictogram.
Danger
categories
A distinction is made between the following:
WARNING
This means that personal injury tor damage to
property may occur if these instructions are not
observed.
CAUTION
This means that damage to property may occur if
these instructions are not observed.
PLEASE NOTE
This means that this instruction must also be ob-
served.
Contents and general safety instructions
VI
CP FB6-E 9809c
Summary of Contents for Compact Performance CP-FB6-E
Page 1: ...Compact Performance CP fieldbus node 6 Programming and diagnosis Fieldbus protocol INTERBUS...
Page 11: ...Contents and general safety instructions X CP FB6 E 9809c...
Page 12: ...Chapter 1 Installation 1 Installation CP FB6 E 9809c 1 1...
Page 29: ...1 Installation 1 18 CP FB6 E 9809c...
Page 30: ...Chapter 2 Commissioning 2 Commissioning CP FB6 E 9809c 2 1...
Page 58: ...Chapter 3 Diagnosis 3 Diagnosis CP FB6 E 9809c 3 1...
Page 70: ...Appendix A Technical appendix A Technical appendix CP FB6 E 9808c A 1...