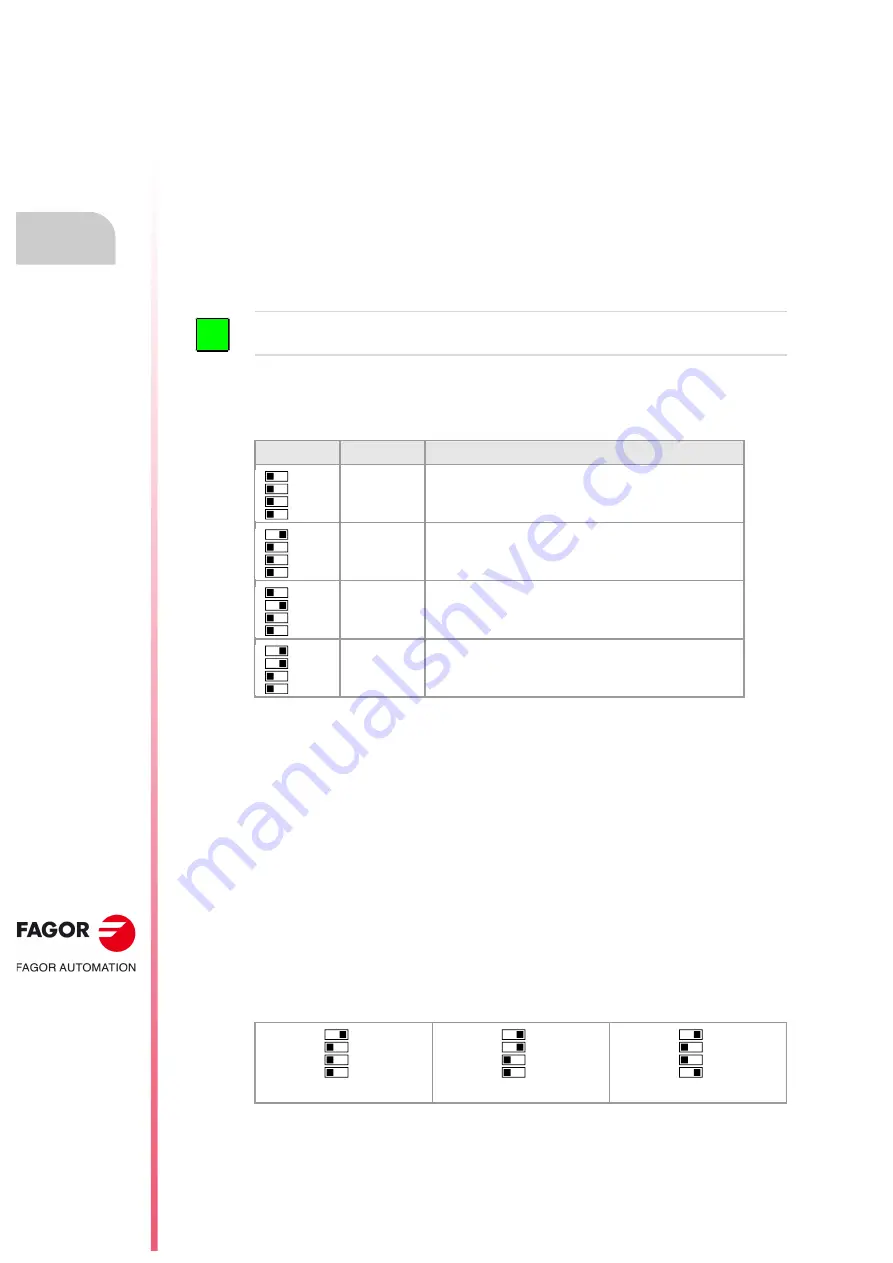
Remote modules.
CNC 8060
CNC 8065
5.
RIOW REMOTE MODULES.
(CANOPEN
PROTOCOL).
RIOW-CANOPEN-STAND
mod
ule.
Lead
ing
(first)
modu
le.
·88·
(R
EF
: 1906)
5.5.3
Node configuration.
The node is configured using the dipswitches to select the node address and the
transmission speed.
Configuring the node speed.
To select the speed of the node, the module must be in configuration mode (all the
dipswitches in the ·off· position). After turning the module on in configuration mode, the top
4 LED's of the module blink indicating the speed selected at the module. The STOP LED
corresponds to dipswitch ·1·, the RUN to dipswitch ·2·, the TX to dipswitch ·3· and the RX
to dipswitch ·4·. The first time the module is configured, the TX LED blinks indicating that
no valid speed has been selected.
The first 4 dipswitches are used to select the speed; the rest must be in the ·off· position.
To select the speed, put the corresponding dipswitches in the ·on· position. The transmission
speed depends on the total length of the cable. Use the following approximate values.
Assigning other values may cause communication errors due to signal distortion.
To save the selected speed, put dipswitch ·8· in the ·on· position. After saving the
configuration, the corresponding LED's turn on to indicate the module speed. For 1 MHz,
all four LED's turn on.
Once the speed has been selected, turn the module off by removing power and set dip-switch
·8· in the ·off· position. Bear in mind that the next time the module is turned on, the position
of the dipswitches will indicate the address (node number) of the group.
Configuring the address (node number) of the group.
Each one of the elements integrated into the CAN bus is identified by its address or node
number. The CNC must always occupy position "0" and the rest of the elements of the bus
will occupy consecutive positions starting with 1.
The address (node number) of the group is selected while the module is off. Select the speed
by putting the corresponding dipswitches in the ·on· position. The binary meaning of each
dipswitch increases according to its number; dipswitch ·1· for address 1, dipswitch ·3· for
address 4 and so on.
If when turning the module on, all the dipswitches are not in the ·off· position, the position of the
dipswitches will be the new address (node number) of the group.
i
Dipswitch
Speed
Length of the CAN bus.
1000 kHz
Up to 20 meters.
800 kHz
From 20 to 40 meters.
500 kHz
From 40 to 100 meters.
250 kHz
From 100 to 500 meters.
Address ·1·.
Address ·3·.
Address ·9·.
1
2
3
4
ON
1
2
3
4
ON
1
2
3
4
ON
1
2
3
4
ON
1
2
3
4
ON
1
2
3
4
ON
1
2
3
4
ON
Summary of Contents for 8025 M CNC
Page 1: ...Ref 1906 8060 8065 CNC Remote modules...
Page 8: ...BLANK PAGE 8...
Page 14: ...BLANK PAGE 14...
Page 16: ...BLANK PAGE 16...
Page 18: ...BLANK PAGE 18...
Page 20: ...BLANK PAGE 20...
Page 24: ...BLANK PAGE 24...
Page 26: ...BLANK PAGE 26...
Page 28: ...BLANK PAGE 28...
Page 30: ...Remote modules CNC 8060 CNC 8065 1 PREVIOUS INFORMATION 30 REF 1906...
Page 32: ...Remote modules CNC 8060 CNC 8065 2 HARDWARE STRUCTURE 32 REF 1906...
Page 177: ...Remote modules CNC 8060 CNC 8065 177 User notes REF 1906...
Page 178: ...Remote modules CNC 8060 CNC 8065 178 User notes REF 1906...
Page 179: ...Remote modules CNC 8060 CNC 8065 179 User notes REF 1906...