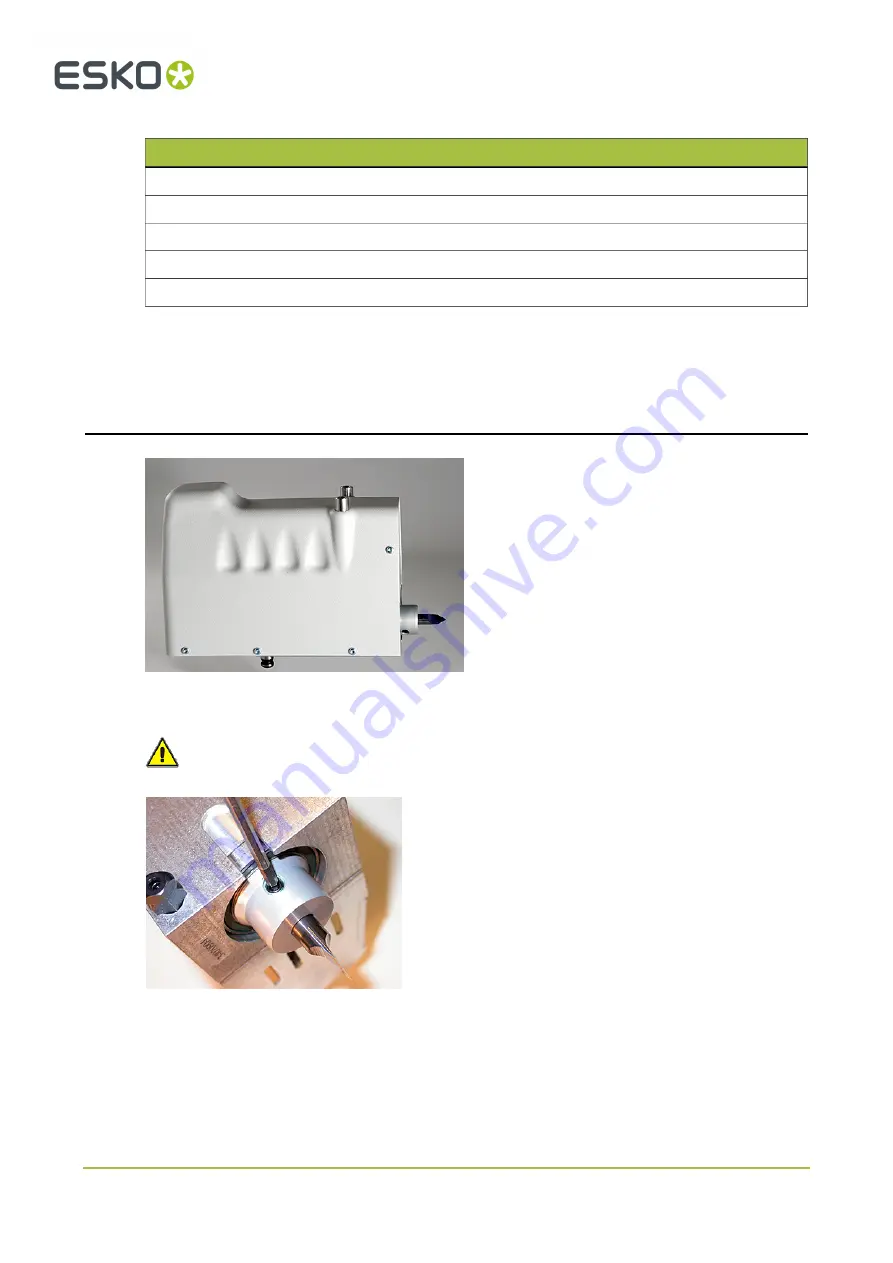
12
Kongsberg XP
Adjustment
Description
Nominal value is 0-3 mm.
Tool Height
Measured automatically, possible to add an
Offset Value
.
Tool Rotation
Adjust
Tool Angle
tangential to
Moving Direction
.
Center Offset
Adjust
Tool
sideways until centered.
Tool Offset
Adjust offset relative to
Laser Pointer
.
For more information about how to run the
Adjustment Wizards
12.14.
Rigid Material Knife
(
RM Knife Tool
)
Replace Knife Blade
Warning: Sharp tool
Use a 3 mm
Allen key
to fix / loosen the
Knife
Blade
.
144