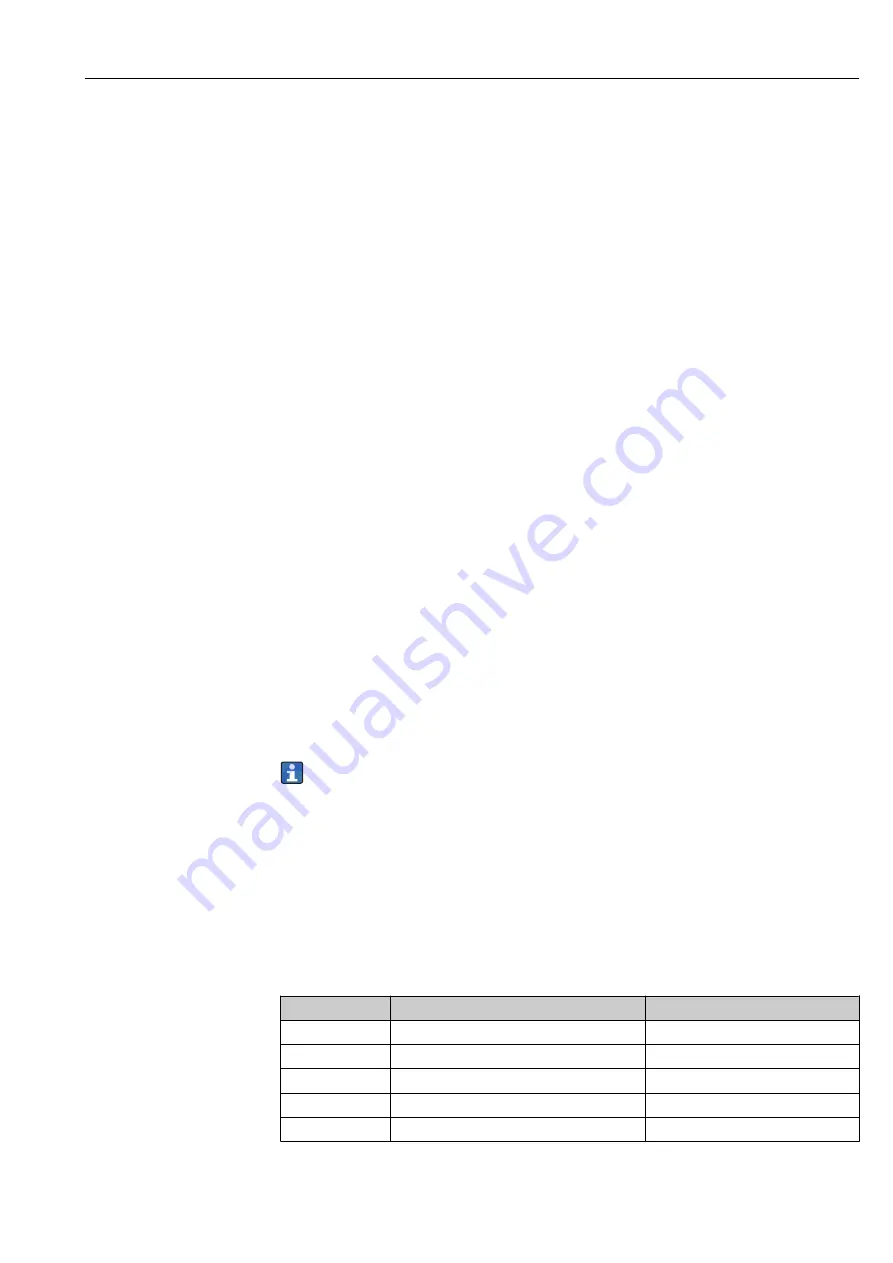
Ecograph T, RSG35
System integration
Hauser
31
8
System integration
8.1
Integrating the measuring device in the system
8.1.1
General notes
The device has (optional) fieldbus interfaces for exporting process values. Measured values
and statuses can also be transmitted to the device via fieldbus. Note: Counters cannot be
transferred.
Alarms or errors in the context of data transmission are displayed depending on the bus
system (e.g. status byte).
The process values are transferred in the same devices that are used for display at the
device.
8.1.2
Ethernet
Setup
→
Advanced setup
→
Communication
→
Ethernet
The IP address can be entered manually (fixed IP address) or assigned automatically using
DHCP.
The port for data communication is preset to 8000. The port can be changed in the
Expert
→
Communication
→
Ethernet
menu.
The following functions are implemented:
• Data communication with PC software (analysis software, configuration software, OPC
server)
• Web server
The following connections are possible at the same time:
• 1x Port 8000 (configuration software, OPC server or analysis software)
• 1x Port 8002 (OPC server only)
• 4x Modbus slave TCP
• 5x Web server
Ports can be changed!
As soon as the maximum number of connections has been reached, new connection
attempts are blocked until an existing connection has been terminated.
8.1.3
Modbus RTU/TCP slave
The device can be connected to a Modbus system via RS485 or Ethernet interface. The
general settings for the Ethernet connection are made in the
Setup
→
Advanced setup
→
Communication
→
Ethernet
menu. Configuration for Modbus communication is done in
the
Setup
→
Advanced setup
→
Communication
→
Modbus slave
menu. Up to 12 analog
inputs and 6 digital inputs can be transmitted via Modbus and stored in the device.
Menu position
RTU (RS485)
Ethernet
Device address:
1
to 247
IP address manual or automatic
Baud rate:
9600/
19200
/38400/57600/115200
-
Parity:
Even/Odd/
None
-
Stop bits:
1
/2
-
Port:
-
502