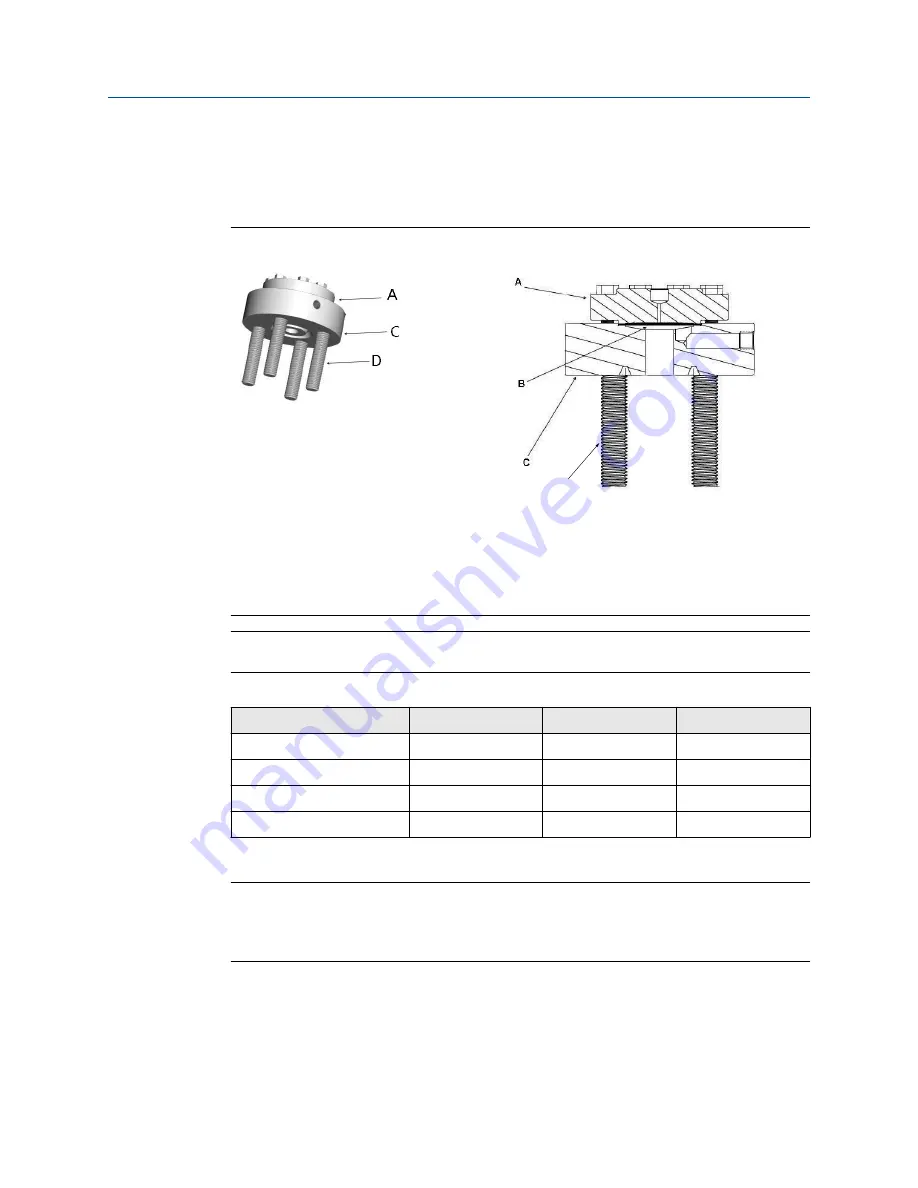
3.10
RCW remote flanged seal - ring type joint (RTJ)
gasket surface
Figure 3-13: RCW Flanged Remote Seal RTJ and Flushing Connection Ring
D
A. Upper housing
B. Diaphragm
C. Lower housing or flushing ring
D. Stud bolts
Note
A lower housing is always required for the RCW type seal.
Table 3-3: RCW Upper Housing Torque Values
Material (nuts and bolts)
Bolt thread size
Class
Torque
SST
3/8–24 NF
150/300/600 lb
23 ft-lb
CS
3/8–24 NF
150/300/600 lb
23 ft-lb
SST
½
–20 NF
900/1500 lb
50 ft-lb
CS
½
–20 NF
900/1500/2500 lb
105 ft-lb
(1)
53 ft-lb for 4.1-in. diaphragm size.
Note
This is the specification for connecting the remote seal to the lower housing, not the
torque specification for the lower housing onto the process flanged connection. The lower
housing bolts should be torqued to the applicable flange requirements.
3.10.1
4.1-in. (104 mm) diaphragm diameter option
The standard diaphragm size for the RCW remote flanged seal with RTJ gasket surface is
2.4-in. A larger, 4.1-in. (104 mm), diaphragm size is offered for small spans to reduce
temperature error when taking process measurements.
Installation
Reference Manual
May 2020
00809-0100-4002
40
Rosemount DP Level
Summary of Contents for Rosemount 1199
Page 4: ...4 ...
Page 8: ...Introduction Reference Manual May 2020 00809 0100 4002 8 Rosemount DP Level ...
Page 22: ...Remote Seal Systems Reference Manual May 2020 00809 0100 4002 22 Rosemount DP Level ...
Page 74: ...Installation Reference Manual May 2020 00809 0100 4002 74 Rosemount DP Level ...
Page 92: ...Fill Fluids Reference Manual May 2020 00809 0100 4002 92 Rosemount DP Level ...