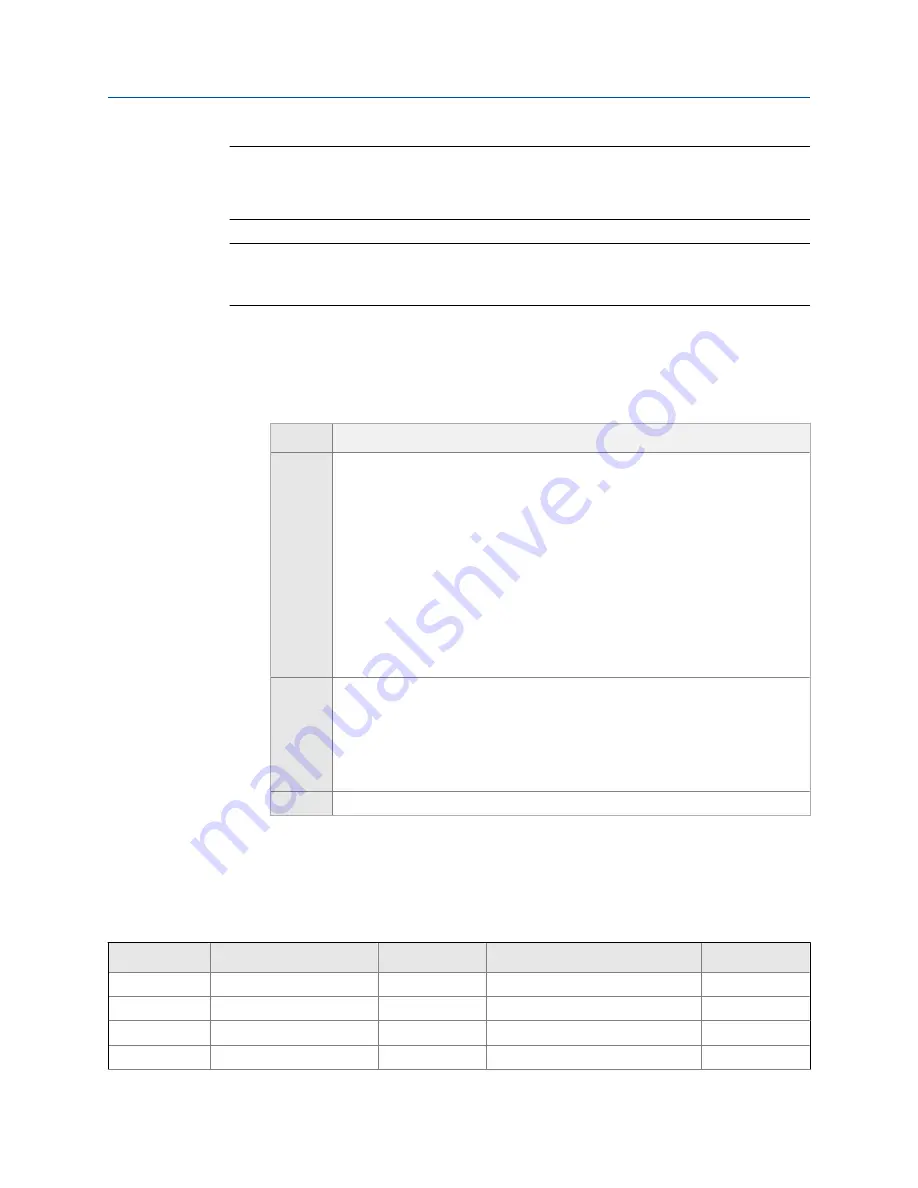
Restrictions
•
For some alerts,
Status Alert Severity
is not configurable.
•
For some alerts,
Status Alert Severity
can be set only to two of the three options.
Tip
Micro Motion recommends using the default settings for
Status Alert Severity
unless you have a specific
requirement to change them.
Procedure
1.
Select a status alert.
2.
For the selected status alert, set
Status Alert Severity
as desired.
Option
Description
Fault
Actions when fault is detected:
•
The alert is posted to the Alert List.
•
Outputs go to the configured fault action (after
Fault Timeout
has expired, if
applicable).
•
Digital communications go to the configured fault action (after
Fault Timeout
has expired, if applicable).
•
The status LED (if available) changes to red or yellow (depending on alert se-
verity).
Actions when alert clears:
•
Outputs return to normal behavior.
•
Digital communications return to normal behavior.
•
The status LED (if available) returns to green and may or may not flash.
Informa-
tional
Actions when fault is detected:
•
The alert is posted to the Alert List.
•
The status LED (if available) changes to red or yellow (depending on alert se-
verity).
Actions when alert clears:
•
The status LED (if available) returns to green and may or may not flash.
Ignore
No action
Status alerts and options for
Status Alert Severity
Status alerts and
Status Alert Severity
Table 5-1:
Alert code
Status message
Default severity Notes
Configurable?
A001
EEPROM Error
Fault
No
A002
RAM Error
Fault
No
A003
No Sensor Response
Fault
Yes
A004
Temperature Overrange
Fault
No
Configure device options and preferences
Configuration and Use Manual
39
Summary of Contents for Micro Motion LNG Series
Page 1: ...Configuration and Use Manual MMI 20032809 Rev AA February 2017 Micro Motion LNG Series Meters ...
Page 6: ...Contents iv Micro Motion LNG Series Meters ...
Page 8: ...Getting Started 2 Micro Motion LNG Series Meters ...
Page 12: ...Before you begin 6 Micro Motion LNG Series Meters ...
Page 18: ...Quick start 12 Micro Motion LNG Series Meters ...
Page 20: ...Configuration and commissioning 14 Micro Motion LNG Series Meters ...
Page 50: ...Configure device options and preferences 44 Micro Motion LNG Series Meters ...
Page 56: ...Integrate the meter with the control system 50 Micro Motion LNG Series Meters ...
Page 58: ...Complete the configuration 52 Micro Motion LNG Series Meters ...
Page 60: ...Operations maintenance and troubleshooting 54 Micro Motion LNG Series Meters ...
Page 74: ...Measurement support 68 Micro Motion LNG Series Meters ...
Page 94: ...Using ProLink III with the transmitter 88 Micro Motion LNG Series Meters ...
Page 98: ...Default values and ranges 92 Micro Motion LNG Series Meters ...
Page 99: ...Default values and ranges Configuration and Use Manual 93 ...