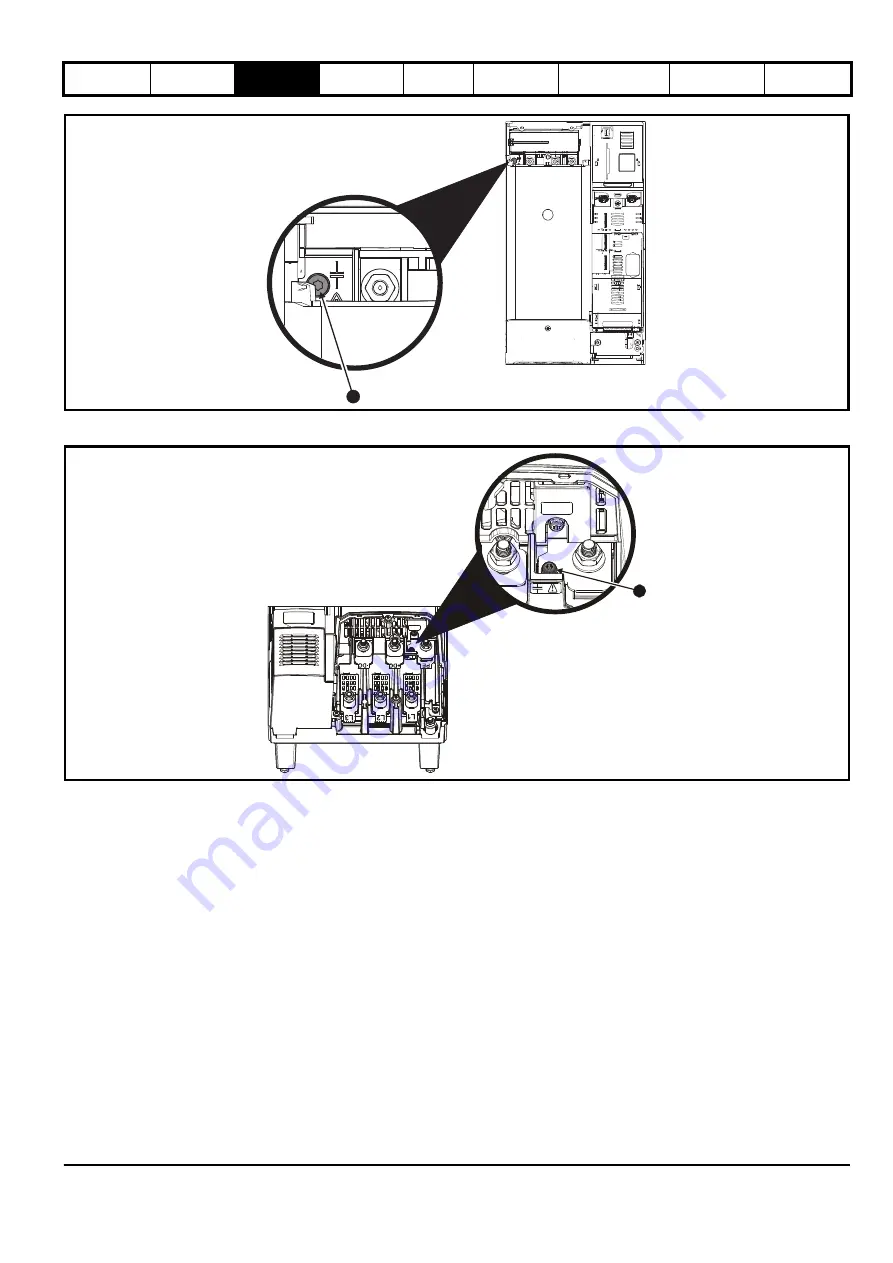
E300 Installation and Commissioning Guide
33
Issue Number: 1
Figure 3-17 Removal of size 6 internal EMC filter
To electrically disconnect the Internal EMC filter, remove the screw (1) as highlighted above.
Figure 3-18 Removal of the size 7 internal EMC filter
To electrically disconnect the Internal EMC filter, remove the screw (1) as highlighted above.
1
1
Summary of Contents for E300 Series
Page 211: ......
Page 212: ...0479 0005 01 ...