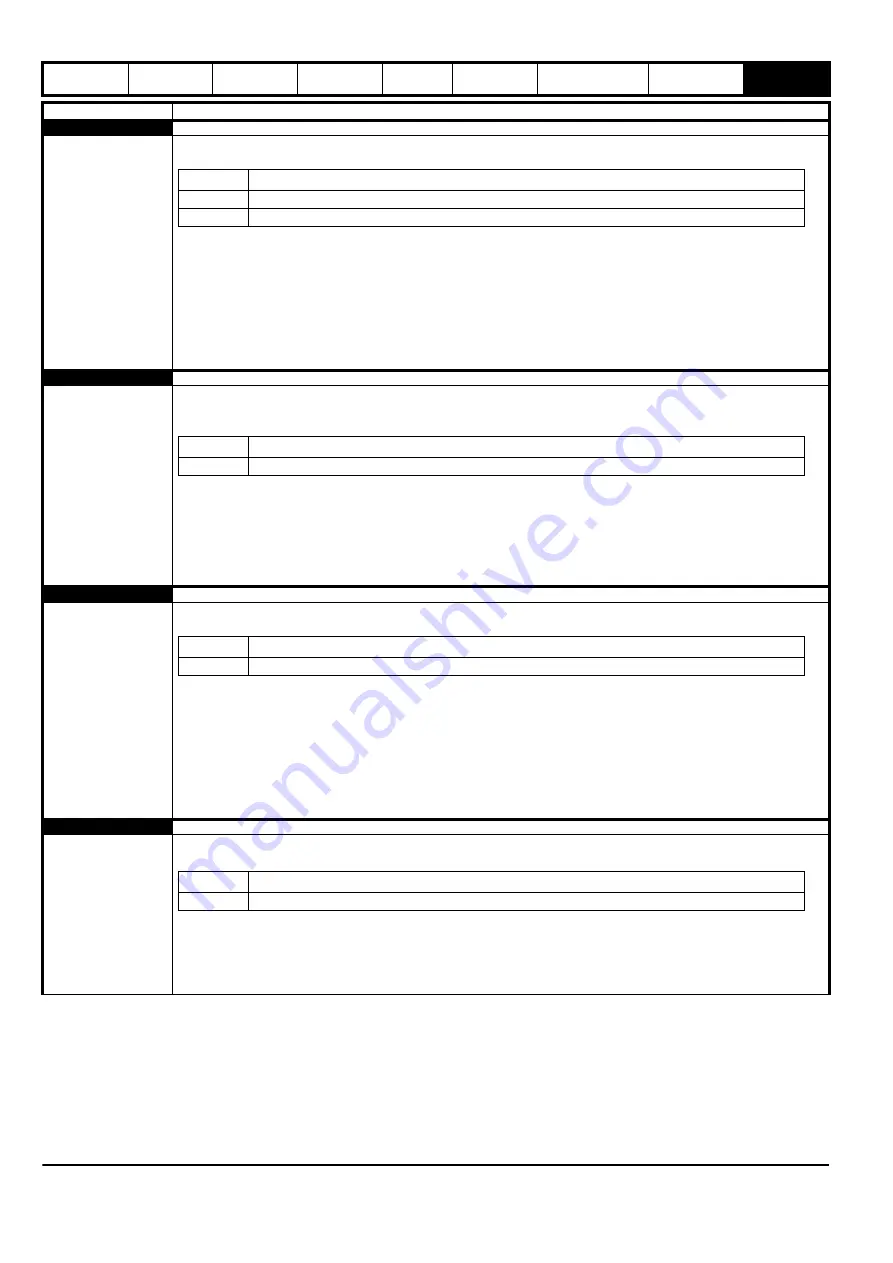
196
E300 Installation Guide
Issue Number: 1
Encoder 3
Phase offset incorrect while running
191
The Encoder 3 trip indicates that the drive has detected an incorrect U, V, W phase angle while running (RFC-S mode only)
or a SinCos phase error. The feedback device can be identified by the sub-trip number.
Recommended actions:
•
Check the integrity of the encoder mechanical mounting
•
Check encoder shield connections, terminations, minimise length of any shield pigtails to connectors
•
For a U, V, W servo encoder, ensure that the phase rotation of the U, V, W commutation signals is the same as the
phase rotation of the motor
•
For a SinCos encoder, ensure that motor and incremental SinCos connections are the correct rotation i.e. for forward
rotation of the motor, the encoder rotates clockwise (when looking at the shaft of the encoder)
•
Repeat the phase offset measurement test
•
Check the encoder signal for noise with an oscilloscope
Encoder 4
Feedback device comms failure
192
The Encoder 4 trip indicates that the encoder communications has timed out or the communications position
message transfer time is too long. This trip can also be caused due to wire break in the communication channel between
the drive and the encoder. The feedback device can be identified by the sub-trip number.
Recommended actions:
•
Check correct encoder connections
•
Check the encoder cable shield connections, terminations, minimise length of any shield pigtails to connectors
•
Check the encoder power supply setting
Drive Encoder Voltage Select
(
C04
) is correct
•
Check
Drive Encoder Additional Power Up Delay
(
C10
) and adjust where required to support encoder feedback
•
Carry out encoder auto-configuration
Drive Encoder Auto Configuration Select (
C02
)
•
Faulty encoder, replace
Encoder 5
Checksum or CRC error
193
The Encoder 5 trip indicates that there is a checksum or CRC error, or the SSI encoder is not ready. The Encoder 5 trip can
also indicate a wire break to a communications based encoder.
Recommended actions:
•
Check correct encoder connections
•
Check the encoder cable shield connections, terminations, minimise length of any shield pigtails to connectors
•
Check the comms resolution setting
Drive Encoder Comms Bits
(
C08
)
•
If using Hiperface, EnDat or BiSS encoders carry out auto-configuration
Drive Encoder Auto Configuration Select
(
C02
)
•
Check
Drive Encoder Additional Power Up Delay
(
C10
) power up delay and adjust where required to support encoder
feedback
•
Check the encoder signal for noise with an oscilloscope
•
Faulty encoder, replace
Encoder 6
Encoder has indicated an error
194
The Encoder 6 trip indicates that the encoder has indicated an error or that the power supply to an SSI encoder has failed,
this trip can also indicate a wire break to an SSI encoder.
Recommended actions:
•
Check correct encoder connections
•
Check the encoder cable shield connections, terminations, minimise length of any shield pigtails to connectors
•
Check the encoder power supply setting
Drive Encoder Voltage Select
(
C04
)
•
Replace the encoder / contact the supplier of the encoder
Trip
Diagnosis
Sub-trip
Reason
1
Drive position feedback interface 1
2
Drive position feedback interface 2
Sub-trip
Reason
1
Drive position feedback interface
Sub-trip
Reason
1
Drive position feedback interface
Sub-trip
Reason
1
Drive position feedback interface
Summary of Contents for E300 Series
Page 211: ......
Page 212: ...0479 0005 01 ...