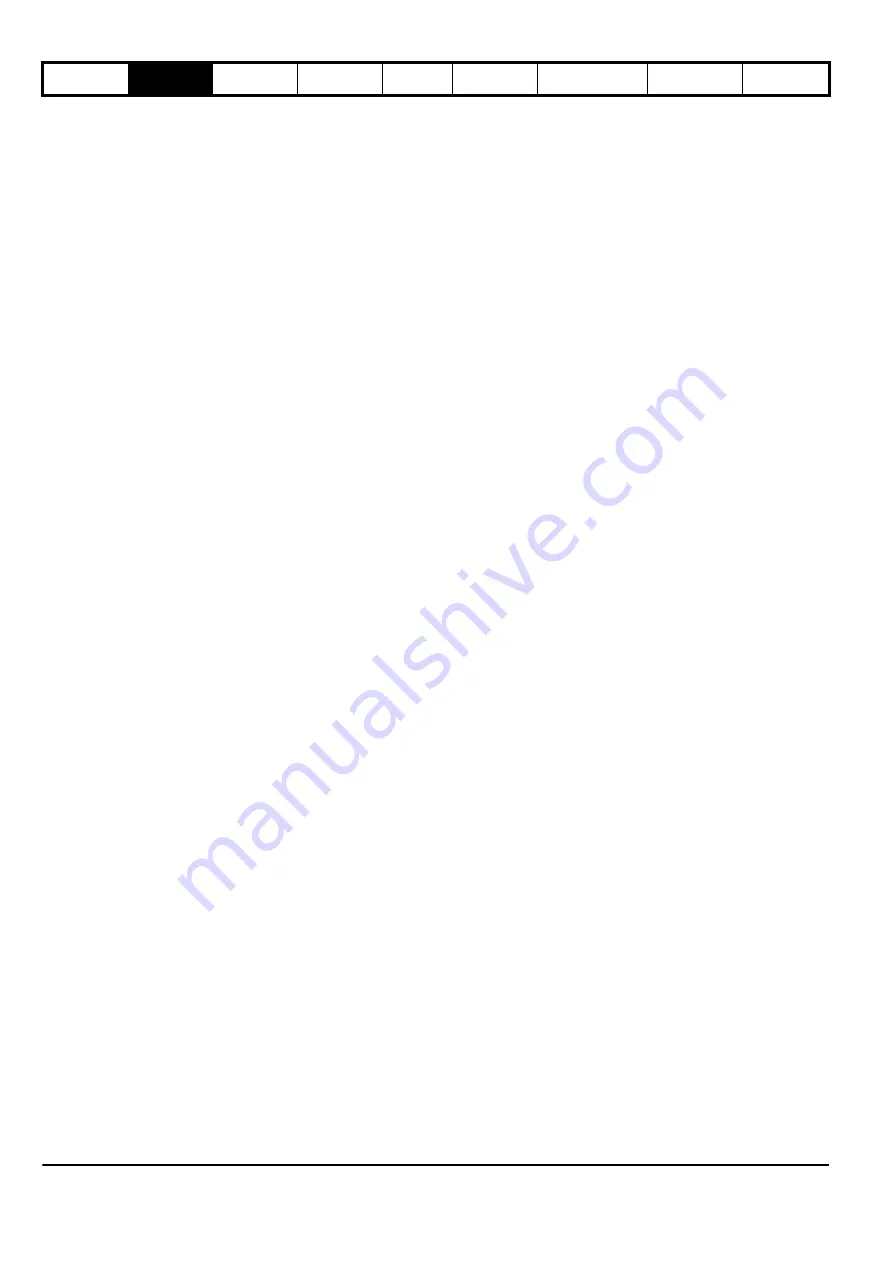
8
E300 Installation and Commissioning Guide
Issue Number: 1
2 Product information
2.1
E300 Advanced Elevator
drive
E300 Advanced Elevator
drive features
•
Universal high performance drive for asynchronous induction motors and synchronous permanent magnet motors.
•
Flexibility with speed and position measurement, supporting multiple devices and all common interfaces
•
Analog and digital I/O with single channel Safe Torque Off (STO) input
•
Local and Remote keypad options
•
NV Media Card for parameter copying and data storage
Configuration
The
E300 Advanced Elevator
drive, can operate in either Open loop or RFC-A mode with asynchronous induction motors for geared Elevator
applications, or in RFC-S mode with synchronous permanent magnet motors for gearless Elevator applications. The default operating mode for the
E300 Standard Elevator
drive is RFC-S mode with this targeted at gearless Elevator applications using PM synchronous motors.
Full support is provided for a both a rotating and static autotune. There is support for a wide range of position feedback devices from the incremental
encoder to high resolution SinCos encoders along with a simulated encoder output as standard onboard the drive.
The
E300 Standard Elevator
drive also has TuV Nord approval to EN81 for a zero output motor contactor solution using the drives Safe Torque Off
(STO), Drive enable input.
Profile
The default operating profile for the
E300 Advanced Elevator
drive is Creep to floor mode. Optimization of the profile is possible through the separate
acceleration and deceleration rates along with multiple jerks. Variable speed and current control loop gains are available for the start, travel and stop.
The
E300 Advanced Elevator
drive additionally offers enhanced profile control:
•
Direct to floor mode - decelerates the elevator car directly to the floor following a signal to stop, with no creep speed.
•
Peak curve operation - profile peak speed and stopping distance controlled regardless of when the signal to stop is given, optimizing travel time.
•
Floor sensor correction - using a floor sensor / limit switch to compensate for rope slip, rope stretch and other mechanical offsets.
•
Position controlled short floor operation.
An optional external load cell compensation input can be connected to the drive where required.
Parallel interface
The
E300 Standard Elevator
drive and control software can support either digital only parallel interfaces (binary or priority speed selection) or digital
parallel interfaces with an analog speed reference. The drive has brake control set-up configured as default with the option of selecting the additional
output motor contactor control.
Programming, monitoring
The
E300 Standard Elevator
drive has a standard Keypad which allows set-up and optimization of the drive along with monitoring of parameters.
An NV Media Card can be used which allows drive parameters to be uploaded and downloaded. The NV Media Card can also be used to back up the
drive parameter set. The NV Media Card support is via a SMARTCARD or SD card Adaptor and SD card.
The Elevator Connect PC tool allows programming, uploading and downloading of drive parameter sets along with monitoring the
E300 Standard
Elevator
drive during operation and optimization. The Elevator Connect PC tool is free of charge and can be downloaded from
www.controltechniques.com.
Communications
The
E300 Advanced Elevator
drive has RS485 serial communications by default. This supports communications to the Elevator controller, PC tools
and Firmware programming. Additional communications protocols are supported via SI option modules.
Summary of Contents for E300 Series
Page 211: ......
Page 212: ...0479 0005 01 ...