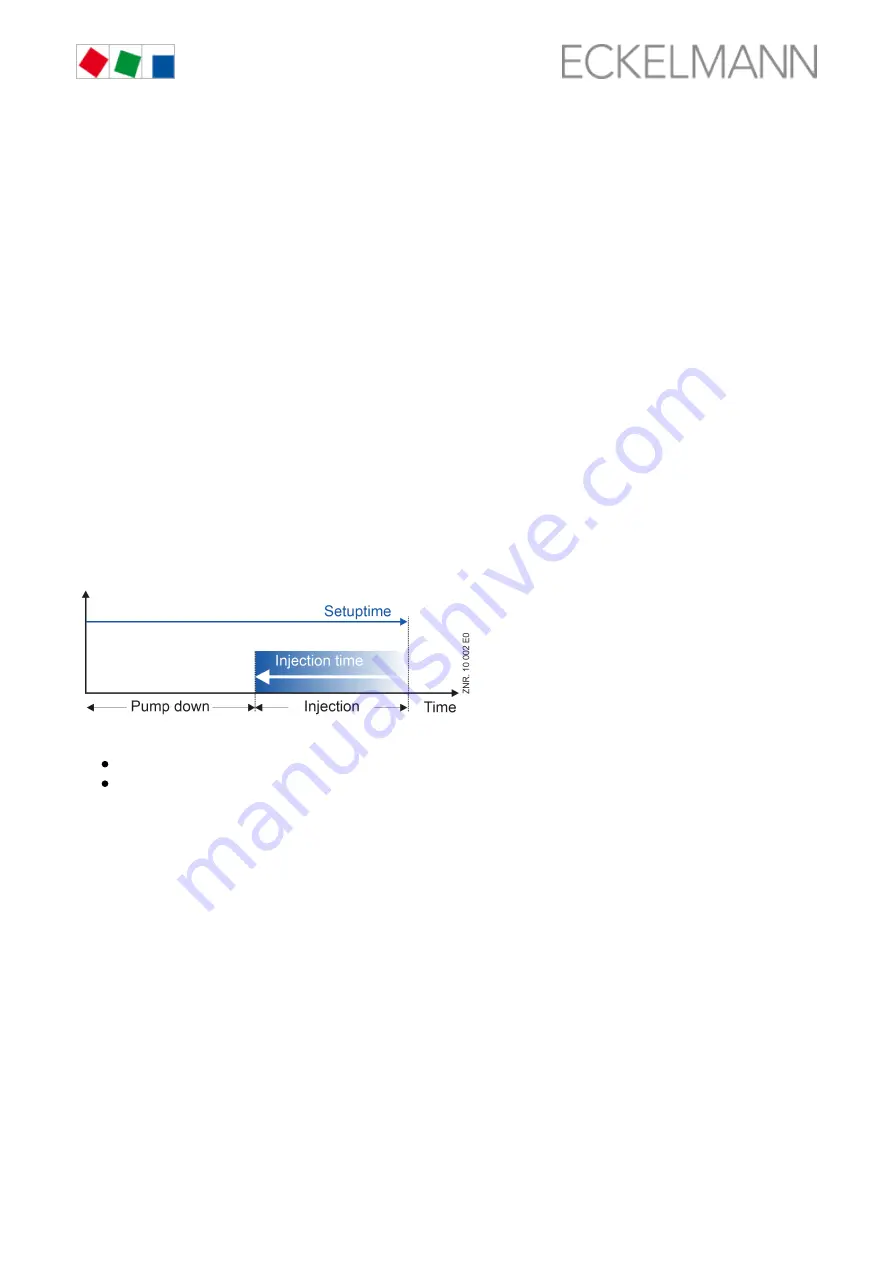
KGL Operating Manual – VS 3010 BS
2018-07-02
/
56 178
The Z2 high-pressure is measured via a pressure transducer with linear characteristic and 4-20 mA output via
analogue input 5 (terminals 4749) and displayed on the actual value screens.
If cascade regulation is inactive (parameter “Kaskadenreg.” (Menu 3-1) = “OFF“), the HP-Z2 actual value is
only for display and not for regulation. The regulation of a cascade can then be performed with an external
controller. If the HP-Z2 transducer and cascade regulation are active, the calculated HP-Z2 and tc_Z2
setpoints are also displayed (see following chapter).
4.6.1.3 Cascade regulation control algorithm
Cascade regulation consists of a PID controller in each case for the temperature control and superheat
regulation of the cascade heat exchanger. The control variable is output via an analogue output to a
continuous control valve (two continuous control valves in tandem operation) and sets the opening degree of
the E-valve (two E-valves in the case of tandem operation). It is automatically decided here whether the
cascade temperature controller (regulation of the condensation temperature Z2) or the cascade superheat
controller (regulation of the Z1 superheat in the cascade) is active.
Fixed opening degree in the pump down / injection phase
After the restart of the controller, it first performs an initialisation cycle in which the opening degree is preset.
During this cycle, the cascade heat exchanger is first evacuated (opening degree = 0%) and then injected with
refrigerant at a fixed opening degree of 100% for an also adjustable time (parameter “setup time” in menu 3-2-
3 and parameter “inject.time" in menu 3-2-3). This procedure, particularly in the case of superheat regulation
with two temperature sensors, prevents the cascade inlet temperature (R5.1) from assuming invalid values.
The injection phase is cancelled if at least one of the following conditions is met:
Expiry of the injection time (parameter “inject.time”in menu 3-2-3 as safety function)
The difference between R6.1 and t0-Z1 or R5.1 exceeds the setpoint superheat and the temperature
difference between the ct-Z2 setpoint and the actual value of the cascade input sensor R5.1 is smaller
than 5 Kelvin.
If the value for the injection time for the evaporator to be regulated is set too high, this can result in the escape
of liquid refrigerant at the evaporator end. As a matter of principle, no check for undercutting the minimum
superheat takes place during the specified injection time.
4.6.1.4 Continuous temperature control using condensation temperature Z2
The regulation of the cooling is performed according to the condensation temperature of the Z2 circuit. In the
event of the failure or absence of a Z2-HP transducer, the temperature control is performed via the refrigerant
temperature sensor R4.1 instead of via tc-Z2.
If the condensation temperature (tc-Z2) of the Z2 circuit (or the refrigerant temperature R4.1 in the event of
failure of the HP-Z2 transducer) reaches the current setpoint, the opening degree of the expansion valve is
reduced to the value required to maintain the condition reached. Cooling can be performed during operation
with only one expansion valve or in tandem operation with two expansion valves.
The setpoint for the temperature regulation (tc-Z2Soll) for the cascade controller is determined according to