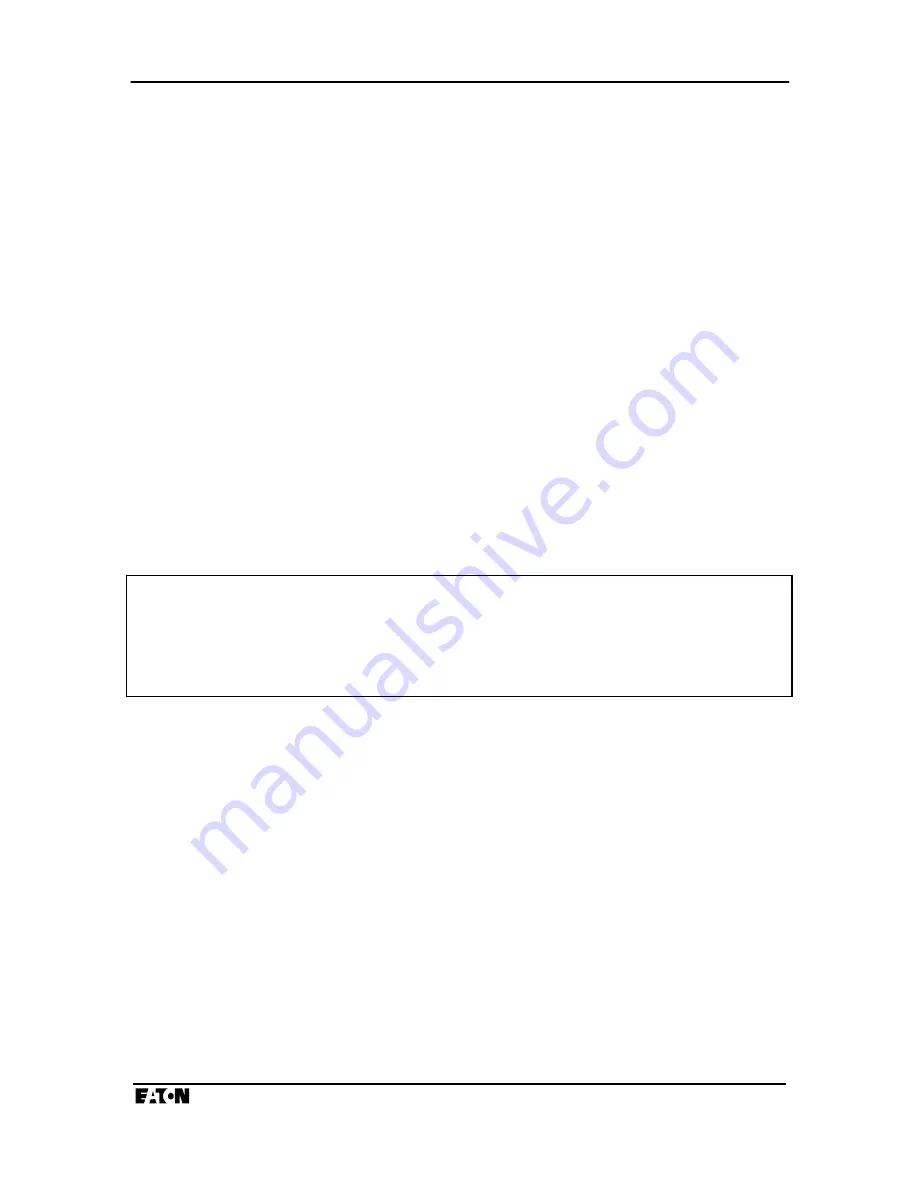
Page 54
I.L. 17562
PR 0.3 Effective 8/99
5.3.10 Setpoint P3L10, Underload Start Delay (ULSD) —
Sets the number of seconds after a
start until the underload trip and alarm functions are enabled.
5.3.11 Setpoint P3L11, Underload Trip Run Delay (ULTR) —
Sets the number of seconds that
current below the underload trip setting must be maintained before a trip output.
5.3.12 Setpoint P3L12, Phase Unbalance Trip Level (UBT) —
Sets the percent of phase
unbalance above which the relay will trip. This element can be set to OFF. The percent
unbalance is calculated from the ratio of negative sequence current to positive sequence current.
Use with the phase unbalance trip start and run delays.
For reversing starter applications (see P1L8), the MP-3000 assumes that the larger sequence
current is the positive sequence current, and can trip for unbalance with the motor turning in
either direction.
5.3.13 Setpoint P3L13, Phase Unbalance Start Delay (UBSD) —
Sets the number of seconds
after a start until the phase unbalance trip and alarm elements are enabled.
5.3.14 Setpoint P3L14, Phase Unbalance Trip Run Delay (UBTR) —
Sets the number of
seconds that a high phase unbalance must be sustained before a trip output.
5.4 Page 4, SP ALARM, Setpoints P4L1 to P4L8 —
This page contains the setpoints needed to
configure the alarm functions. Each alarm function can be disabled.
NOTE
Even if an alarm function is enabled on this page, it must also be directed to an output relay to
produce contact operation for remote or annunciator alarming. Normally (and by factory default
settings), the conditions should all be directed to the ALARM Relay by the 22 settings on setpoint
Page 8. They may also be selectively directed to the AUX 1 and/or AUX 2 output relays using
the settings on setpoint Pages 9 and 10 respectively.
If you configure an alarm here, but don't set it to activate any output relay on Pages 8 to 10,
alarm conditions will still appear in all displays and logs, and in communications information sent
to a PowerNet host.
5.4.1 Setpoint P4L1,
Ground Fault Alarm Level (GFA) —
Sets the ground fault alarm current
pickup level in percent of ground Ct ratio numerator. For example, with a 50:5 ground fault Ct
and a setting of 10%, the GFA function will pick up at 10% of 50A, or 5A actual ground fault
current in the motor. The start and/or run delays must expire before the alarm output occurs.
5.4.2 Setpoint P4L2, I
2
T Alarm Level (I2TA) —
Sets the I
2
T model thermal accumulator or
bucket level at which the relay will alarm, in percent of I
2
T bucket trip value. This important
alarm indicates that the MP-3000 thermal model is progressing toward a thermal protective trip
(thermal capacity bucket is filling), so that the user can act to reduce loading or protect the
process.
This setting also determines when the I
2
T trip condition can reset. After a trip, the I
2
T bucket or
thermal accumulator must cool below the I
2
T alarm level before the thermal trip can reset. See
setting P12L5 for more on resetting of thermal trip.
Summary of Contents for 66D2032G01
Page 18: ...Page 18 I L 17562 PR 0 3 Effective 8 99 Figure 4 1 MP 3000 Pushbuttons...
Page 19: ...I L 17562 Page 19 PR 0 3 Effective 8 99 Figure 4 2 MP 3000 LED Indicators...
Page 72: ...Page 72 I L 17562 PR 0 3 Effective 8 99 Figure 6 1 Panel Cutout Dimensions...
Page 73: ...I L 17562 Page 73 PR 0 3 Effective 8 99 Figure 6 2 Faceplate Dimensions...
Page 74: ...Page 74 I L 17562 PR 0 3 Effective 8 99 Figure 6 3 MP 3000 Case Depth Dimensions...
Page 75: ...I L 17562 Page 75 PR 0 3 Effective 8 99 Figure 6 4 Universal RTD Module Mounting Dimensions...
Page 76: ...Page 76 I L 17562 PR 0 3 Effective 8 99 Figure 6 5 Rear Panel Terminals...
Page 78: ...Page 78 I L 17562 PR 0 3 Effective 8 99 Figure 6 7 Typical ac Supply and URTD Wiring...
Page 79: ...I L 17562 Page 79 PR 0 3 Effective 8 99 Figure 6 8 Alternatives for Discrete Input Wiring...
Page 80: ...Page 80 I L 17562 PR 0 3 Effective 8 99 Figure 6 9 RTD Wiring to URTD Module...
Page 100: ...Page 100 I L 17562 PR 0 3 Effective 8 99 Figure 9 1 Rotor Temperature Tracking...
Page 101: ...I L 17562 Page 101 PR 0 3 Effective 8 99 Figure 9 2 Motor Protection Curve...
Page 102: ...Page 102 I L 17562 PR 0 3 Effective 8 99 Figure 9 3 Underload Jam Protection Curve...
Page 104: ...Page 104 I L 17562 PR 0 3 Effective 8 99 Figure 9 5 Motor Protection Curve Example with RTDs...
Page 105: ...I L 17562 Page 105 PR 0 3 Effective 8 99 Figure 9 6 Motor Start and Run Cycles...
Page 109: ...I L 17562 Page 109 PR 0 3 Effective 8 99 P5L8 40 Incomplete Sequence time 1 60s OFF 1 240s...