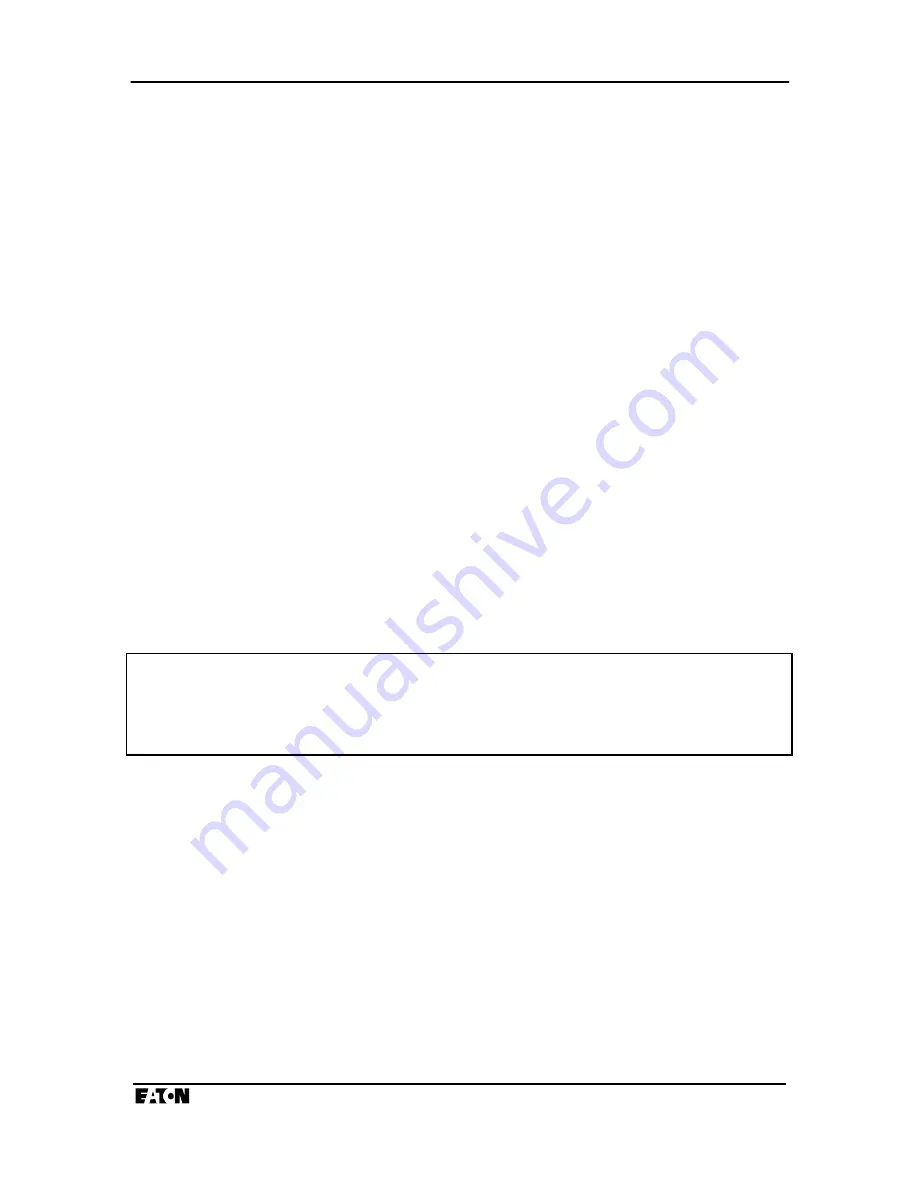
Page 50
I.L. 17562
PR 0.3 Effective 8/99
Ground fault protection by residual connection of phase Cts is possible, but doesn't give high
sensitivity. See Section 9.1.10.
5.1.7 Setpoint P1L7, Frequency (FREQ) —
Sets the MP-3000 for either a 60 Hz or 50 Hz ac
supply frequency. No hardware settings are necessary. The MP-3000 can protect the motor
during the limited frequency excursions of a power system in emergency conditions, but is not
intended for use with variable-frequency motor drives.
5.1.8 Setpoint P1L8, Reversing or Non-reversing Starter (REV/NONREV) —
Specifies
whether or not the starter for this motor is designed to reverse phase sequence and make the
motor run in either direction.
Setting to REV indicates that starting with a reversed phase sequence is an acceptable operating
condition. The relay will accept either sequence at the time of a start, and will assign the role of
positive sequence to the larger of the two sequence components.
When the motor runs in reverse, any phase current unbalance is displayed with a negative sign.
This is not a negative number - view it as a notation that the unbalance is measured on the
motor running in reverse.
If set to NONREV, the relay will check the phase sequence at the beginning of the START cycle
only and accept only a positive phase sequence (ABC). It trips the motor for a reversed
sequence of ACB with the message “PH REVRS” on the display.
5.2 Page 2, SP RTD, Setpoints P2L1 to P2L10 —
This page contains all of the setpoints
needed to use the RTD temperature inputs from the optional URTD accessory module.
NOTE
For direct temperature tripping, alarming, and displays to function, a URTD module must be
connected and communicating with the relay. However, the setpoints for temperature can be
viewed or adjusted with or without a URTD module connected.
Pay attention to the specific labeled assignments of the eleven URTD input channels. The first
six are specifically intended for up to six RTDs embedded in the motor stator winding. Inputs 7
and 8 are specifically for motor bearing RTDs. Inputs 9 and 10 are specifically for load bearings.
Input 11 is an auxiliary general-use input.
All RTD inputs have alarm and trip values set below. But, note that only the maximum of the
values read via stator RTD channels 1 through 6 is used by the MP-3000 motor thermal
modeling algorithm.
5.2.1 Setpoint P2L1, RTD Display Information (RTD IN C or RTD IN F) —
Specifies the
temperature displays in degrees Celsius or degrees Fahrenheit.
5.2.2 Setpoint P2L2, Winding Temp Trip (WD T) —
Specifies the motor stator winding
temperature limit above which the hottest winding RTD will cause the relay to trip the motor.
This trip can also be set to OFF. Trip temperature values are in degrees C or F depending on
Summary of Contents for 66D2032G01
Page 18: ...Page 18 I L 17562 PR 0 3 Effective 8 99 Figure 4 1 MP 3000 Pushbuttons...
Page 19: ...I L 17562 Page 19 PR 0 3 Effective 8 99 Figure 4 2 MP 3000 LED Indicators...
Page 72: ...Page 72 I L 17562 PR 0 3 Effective 8 99 Figure 6 1 Panel Cutout Dimensions...
Page 73: ...I L 17562 Page 73 PR 0 3 Effective 8 99 Figure 6 2 Faceplate Dimensions...
Page 74: ...Page 74 I L 17562 PR 0 3 Effective 8 99 Figure 6 3 MP 3000 Case Depth Dimensions...
Page 75: ...I L 17562 Page 75 PR 0 3 Effective 8 99 Figure 6 4 Universal RTD Module Mounting Dimensions...
Page 76: ...Page 76 I L 17562 PR 0 3 Effective 8 99 Figure 6 5 Rear Panel Terminals...
Page 78: ...Page 78 I L 17562 PR 0 3 Effective 8 99 Figure 6 7 Typical ac Supply and URTD Wiring...
Page 79: ...I L 17562 Page 79 PR 0 3 Effective 8 99 Figure 6 8 Alternatives for Discrete Input Wiring...
Page 80: ...Page 80 I L 17562 PR 0 3 Effective 8 99 Figure 6 9 RTD Wiring to URTD Module...
Page 100: ...Page 100 I L 17562 PR 0 3 Effective 8 99 Figure 9 1 Rotor Temperature Tracking...
Page 101: ...I L 17562 Page 101 PR 0 3 Effective 8 99 Figure 9 2 Motor Protection Curve...
Page 102: ...Page 102 I L 17562 PR 0 3 Effective 8 99 Figure 9 3 Underload Jam Protection Curve...
Page 104: ...Page 104 I L 17562 PR 0 3 Effective 8 99 Figure 9 5 Motor Protection Curve Example with RTDs...
Page 105: ...I L 17562 Page 105 PR 0 3 Effective 8 99 Figure 9 6 Motor Start and Run Cycles...
Page 109: ...I L 17562 Page 109 PR 0 3 Effective 8 99 P5L8 40 Incomplete Sequence time 1 60s OFF 1 240s...