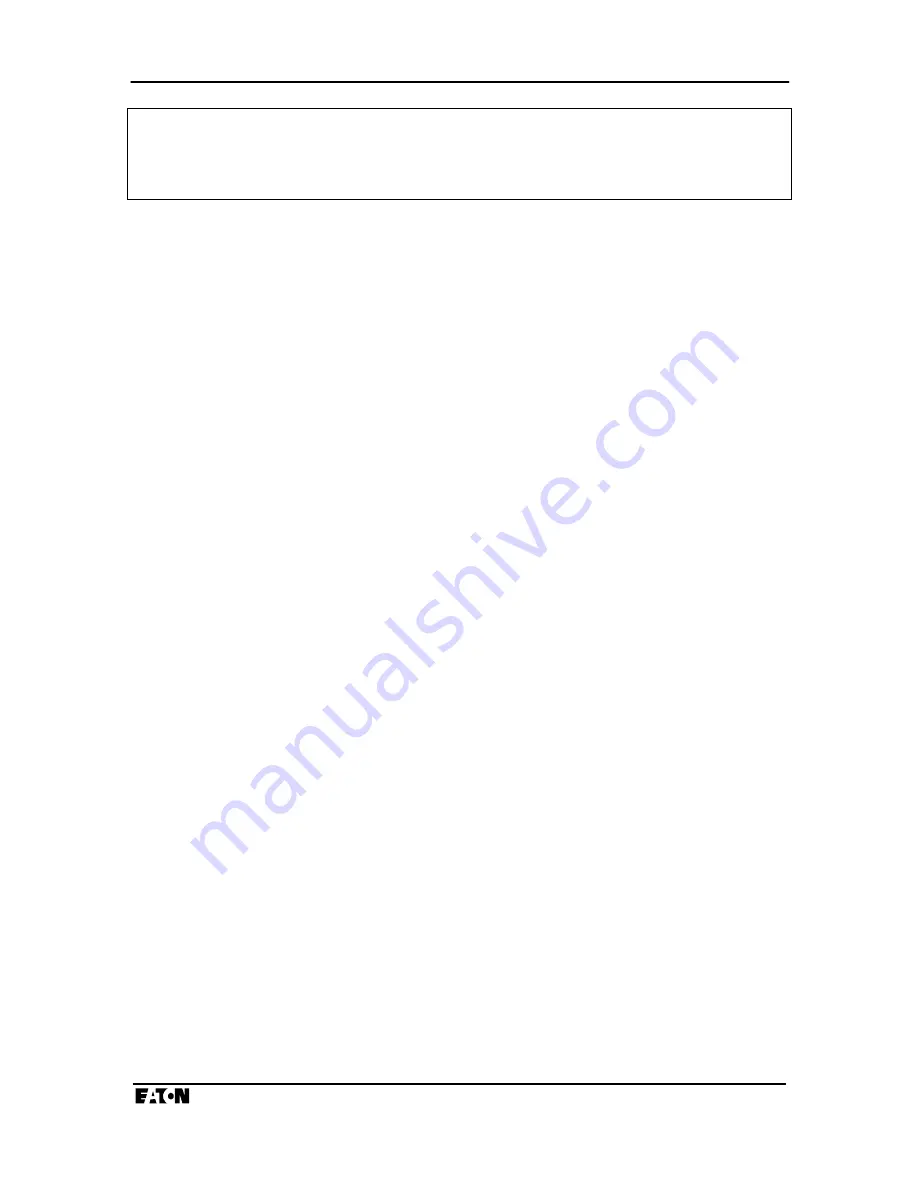
Page 84
I.L. 17562
PR 0.3 Effective 8/99
DANGER
The contactor control circuit is to be reconnected. At this time the motor associated with the
application can be started. It is important to ensure that all safety precautions associated with
rotating equipment and the associated driven mechanism be taken. Failure to do so can result in
serious or fatal injury and/or equipment damage.
q
Disconnect all ac power from the system.
q
Reconnect the contactor lead to MP-3000 trip relay terminal 12.
q
Check all rotating components and driven mechanisms associated with the motor for secure
connections.
q
Clear away any loose or foreign objects.
q
Clear all personnel from the area of the motor and driven mechanisms.
q
Turn on all ac power.
q
Make sure the MP-3000 Protection LED is on, and that the display says READY--3.
q
Follow any startup procedures for the load equipment.
q
Start the motor using the external start switch or contacts.
q
Using the information supplied by the application engineer or equipment manufacturer, verify
that the motor is operating properly.
q
With the motor running, use a clamp-on type ammeter to measure the ac current on each of
the motor phases.
q
Verify that the I
A,
I
B,
and I
C
currents, as indicated by the MP-3000 on the MONT I Page of the
Monitor mode are within about 5% of the ammeter values.
q
If the current during this test is well below FLA, or if the cts are far from the optimum ratio,
errors may be larger. This test is intended to show incorrectly set ct ratios or faulty wiring,
rather than precision of measurements.
q
If a ground Ct is connected, check ground current IG. Investigate the cause of any abnormal
ground leakage current flow.
q
Check the percent unbalance display %UB for consistency with the ammeter measurements,
given the acceptable error ranges.
q
A negative sign on the unbalance display indicates that the relay is programmed for a
reversing motor, and that it believes the motor is running in reverse. Since an MP-3000
programmed for a reversing starter won't trip for reversed phase sequence, this gives a
convenient check that the phase sequence is properly wired.
q
If the analog transducer output is connected, determine which measurement it is transmitting
- view setpoint P11L1.
q
Check that the analog output current corresponds to the displayed value of the selected
parameter.
q
If a PowerNet data communications host is connected, upload the starting current profile and
check for coordination with cold-start protection curves on the PowerNet display.
q
It is wise to verify the ability of the MP-3000 to open the contactor and trip the motor. The
easiest way is by remote trip, via remote trip contact or data communications. Many other
internal functions can be manipulated to force a relay trip. One technique is to connect a
shorting jumper across the relay current terminals for one of the three phases - this should
produce an unbalance trip, or a thermal trip after some time.
Summary of Contents for 66D2032G01
Page 18: ...Page 18 I L 17562 PR 0 3 Effective 8 99 Figure 4 1 MP 3000 Pushbuttons...
Page 19: ...I L 17562 Page 19 PR 0 3 Effective 8 99 Figure 4 2 MP 3000 LED Indicators...
Page 72: ...Page 72 I L 17562 PR 0 3 Effective 8 99 Figure 6 1 Panel Cutout Dimensions...
Page 73: ...I L 17562 Page 73 PR 0 3 Effective 8 99 Figure 6 2 Faceplate Dimensions...
Page 74: ...Page 74 I L 17562 PR 0 3 Effective 8 99 Figure 6 3 MP 3000 Case Depth Dimensions...
Page 75: ...I L 17562 Page 75 PR 0 3 Effective 8 99 Figure 6 4 Universal RTD Module Mounting Dimensions...
Page 76: ...Page 76 I L 17562 PR 0 3 Effective 8 99 Figure 6 5 Rear Panel Terminals...
Page 78: ...Page 78 I L 17562 PR 0 3 Effective 8 99 Figure 6 7 Typical ac Supply and URTD Wiring...
Page 79: ...I L 17562 Page 79 PR 0 3 Effective 8 99 Figure 6 8 Alternatives for Discrete Input Wiring...
Page 80: ...Page 80 I L 17562 PR 0 3 Effective 8 99 Figure 6 9 RTD Wiring to URTD Module...
Page 100: ...Page 100 I L 17562 PR 0 3 Effective 8 99 Figure 9 1 Rotor Temperature Tracking...
Page 101: ...I L 17562 Page 101 PR 0 3 Effective 8 99 Figure 9 2 Motor Protection Curve...
Page 102: ...Page 102 I L 17562 PR 0 3 Effective 8 99 Figure 9 3 Underload Jam Protection Curve...
Page 104: ...Page 104 I L 17562 PR 0 3 Effective 8 99 Figure 9 5 Motor Protection Curve Example with RTDs...
Page 105: ...I L 17562 Page 105 PR 0 3 Effective 8 99 Figure 9 6 Motor Start and Run Cycles...
Page 109: ...I L 17562 Page 109 PR 0 3 Effective 8 99 P5L8 40 Incomplete Sequence time 1 60s OFF 1 240s...