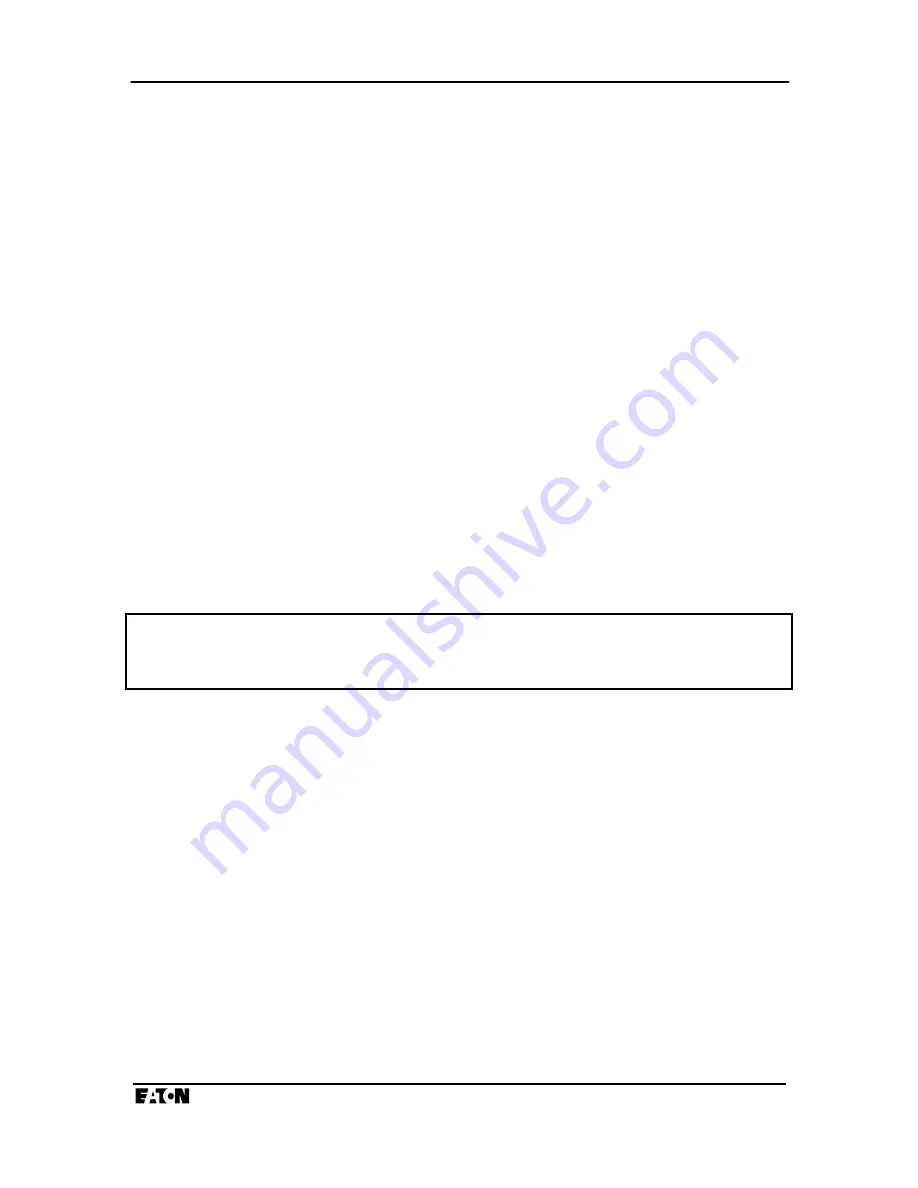
Page 114
I.L. 17562
PR 0.3 Effective 8/99
temperatures, thermal-model bucket level, and time limits on restarting imposed by jogging
functions. See Table 4.2 for a listing and description of these parameters. Note that software
version number appears in this mode.
12.1.5 Reviewing Motor History Data —
Push the History mode button. See Table 4.4 for the
four pages of information available for review in the History Mode, including the numbers of each
of the different types of trips and alarms, and the highest currents and temperatures with time
tags. The accumulation of these historical values can be selectively cleared and restarted using
setpoints P14L1 to P14L4 in the Program mode. See Section 5.14.
12.1.6 Reviewing the Logged Motor Data —
Push the Log mode button. Pages include a log
book of the last 100 events, a log of the last 20 abnormal events with more details, and a
detailed log of the last 4 starts. The MP-3000 logs motor events in chronological order with
details and time tag as shown in Table 4.5.
12.1.7 Reviewing the motor starting current profile curve -
One particular logging function,
the starting current profile display, cannot be viewed on the relay faceplate. The profile data
must be uploaded via data communications to a PowerNet host computer after the start.
PowerNet provides an informative plot of the actual starting current curve, plotted along with the
cold-start protection limit curve, for checking of coordination. See Figure 2.1 for an example.
The MP-3000 stores the profiles for the last 4 starts. See PowerNet Help function or users
manual for instructions on viewing the profile. See Section 10 for information on connecting
data communications to the MP-3000.
•
12.2 Troubleshooting MP-3000 Monitored Equipment —
If the monitored equipment
malfunctions, certain troubleshooting information from the MP-3000 assists in localizing the
problem. The description is given in two categories - alarm conditions (Paragraph 12.2.1) and
trip conditions (Paragraph 12.2.2).
WARNING
Troubleshooting procedures involve working at times in equipment areas where potentially lethal
voltages are present. Personnel must have adequate training and exercise extreme caution to
avoid injury, including possible fatal injury.
12.2.1 Alarm conditions —
An alarm condition occurs when one of the electrical characteristics
exceeds its programmed setpoint value. Start delays, and run or pickup delays, must expire
before the alarm is raised. The red alarm LED lights and a message appears in the display
window to assist with the isolation process. Multiple alarms are alternated or cycled in the
display.
Connect external devices, such as an annunciator, to the Alarm relay of the MP-3000, to get the
attention of operators who can act to solve the problem. The form c alarm relay contacts are
brought out to terminals 17, 18, and 19 - see Figure 6.5.
Setpoint Page 8, setpoints P8L1 to P8L22, allow the user to select which alarm or trip events
operate the alarm relay. Normally, the user should direct all alarms of functions in use to the
alarm relay by these setpoints.
It is recommended to use the alarm relay in Mode 2, and to direct all alarm conditions to it.
Connect the annunciator to terminals 17 and 18. With this connection, an alarm is raised if the
relay or its power supply fails; as well as for all other problems the MP-3000 can actively report.
However, if the MP-3000 is deenergized routinely in service, use the alarm relay in Mode 1 and
connect the annunciator to terminals 18 and 19 to avoid nuisance alarms.
Summary of Contents for 66D2032G01
Page 18: ...Page 18 I L 17562 PR 0 3 Effective 8 99 Figure 4 1 MP 3000 Pushbuttons...
Page 19: ...I L 17562 Page 19 PR 0 3 Effective 8 99 Figure 4 2 MP 3000 LED Indicators...
Page 72: ...Page 72 I L 17562 PR 0 3 Effective 8 99 Figure 6 1 Panel Cutout Dimensions...
Page 73: ...I L 17562 Page 73 PR 0 3 Effective 8 99 Figure 6 2 Faceplate Dimensions...
Page 74: ...Page 74 I L 17562 PR 0 3 Effective 8 99 Figure 6 3 MP 3000 Case Depth Dimensions...
Page 75: ...I L 17562 Page 75 PR 0 3 Effective 8 99 Figure 6 4 Universal RTD Module Mounting Dimensions...
Page 76: ...Page 76 I L 17562 PR 0 3 Effective 8 99 Figure 6 5 Rear Panel Terminals...
Page 78: ...Page 78 I L 17562 PR 0 3 Effective 8 99 Figure 6 7 Typical ac Supply and URTD Wiring...
Page 79: ...I L 17562 Page 79 PR 0 3 Effective 8 99 Figure 6 8 Alternatives for Discrete Input Wiring...
Page 80: ...Page 80 I L 17562 PR 0 3 Effective 8 99 Figure 6 9 RTD Wiring to URTD Module...
Page 100: ...Page 100 I L 17562 PR 0 3 Effective 8 99 Figure 9 1 Rotor Temperature Tracking...
Page 101: ...I L 17562 Page 101 PR 0 3 Effective 8 99 Figure 9 2 Motor Protection Curve...
Page 102: ...Page 102 I L 17562 PR 0 3 Effective 8 99 Figure 9 3 Underload Jam Protection Curve...
Page 104: ...Page 104 I L 17562 PR 0 3 Effective 8 99 Figure 9 5 Motor Protection Curve Example with RTDs...
Page 105: ...I L 17562 Page 105 PR 0 3 Effective 8 99 Figure 9 6 Motor Start and Run Cycles...
Page 109: ...I L 17562 Page 109 PR 0 3 Effective 8 99 P5L8 40 Incomplete Sequence time 1 60s OFF 1 240s...