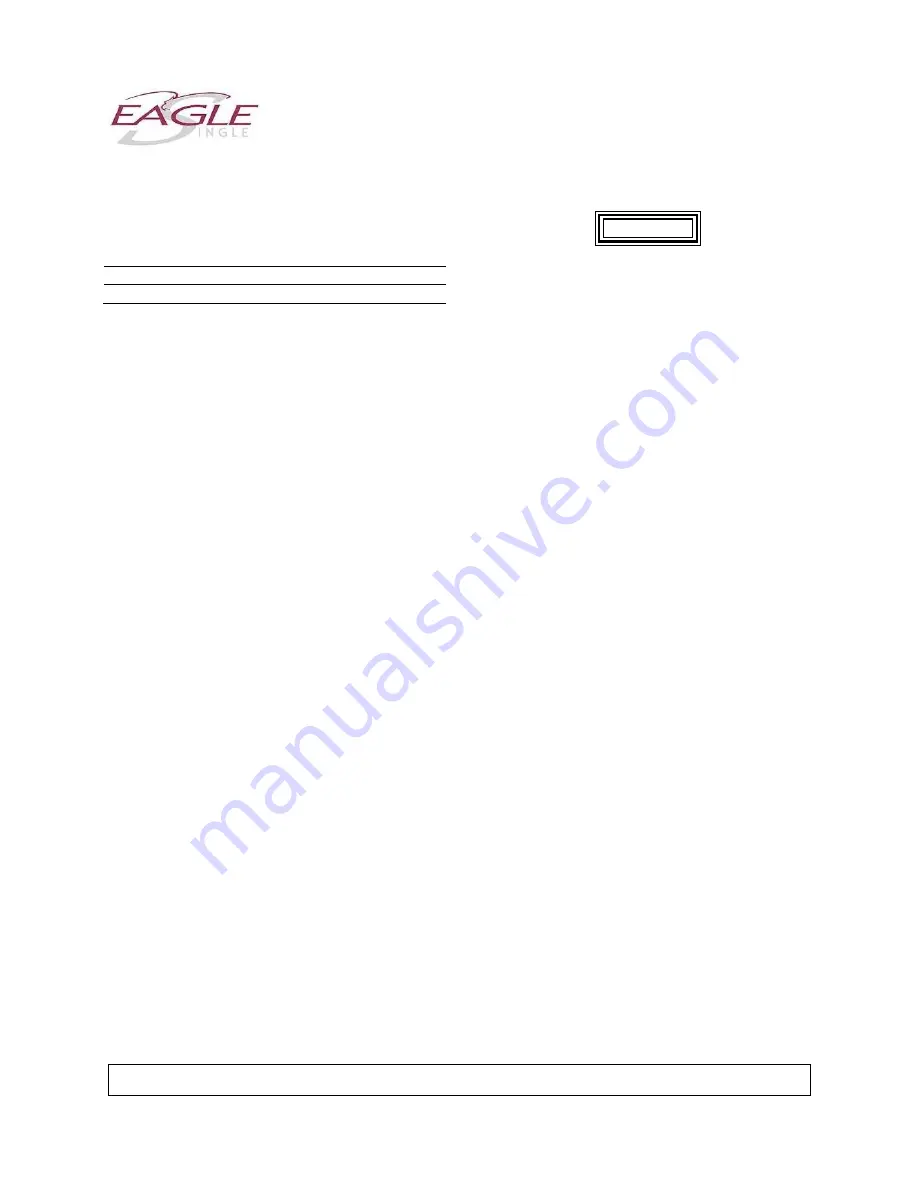
ICA-D212-725 (67)
Page 14 of 55
CHAPTER 67 – FLIGHT CONTROLS (67-00-00)
COPYRIGHT
2007 BY DART AEROSPACE LTD.
THIS DOCUMENT IS PRIVATE AND CONFIDENTIAL AND IS SUPPLIED ON THE EXPRESS CONDITION THAT IT IS NOT TO BE USED FOR ANY PURPOSE OR COPIED OR COMMUNICATED TO
ANY OTHER PERSON WITHOUT WRITTEN PERMISSION FROM DART AEROSPACE LTD.
Revision:
6
Date:
13.08.26
67.1.8
Anti-Torque Controls (Helicopters
Prior to s/n 31175)
MATERIALS REQUIRED
NUMBER NOMENCLATURE
C-405 Lockwire
NOTE
Refer to paragraph 67.1.4 prior to beginning
rigging.
67.1.8.1
Ensure linkage is complete, with
the following adjustable links and control tubes
disconnected:
67.1.8.1.1
Pitch change links (3, Figure 67-5)
from tail rotor blades.
67.1.8.1.2
Link (6) from lever on left side of
tail rotor gearbox.
67.1.8.1.3
Control tube (12) from bellcrank
(13) above hydraulic cylinder.
67.1.8.1.4
Force gradient (31) from pedal
adjuster (28).
NOTE
For rigging copilot pedals if copilot dual control kit
is installed, refer to appropriate Service
Instruction.
67.1.8.2
Retract all adjustable stop bolts
(detail E) as far as possible.
NOTE
Adjustment of pitch change link length not required
for fixed length pitch change links (Post TB 212-
01-185)
67.1.8.3
Adjust both pitch change links (3)
to initial length of 6.115 ±0.010 in. (155.32 ±0.254
mm) between centers of rod end bearings.
67.1.8.4
Connect each link to blade pitch
horn with bolt and floating bushing. Torque bolt to
135 in.Ibs. (15.26 Nm). Secure with lockwire (C-
405).
CAUTION
DO NOT MEASURE BETWEEN CROSSHEAD
AND WEAR INDICATOR, IF INSTALLED.
MEASUREMENT SHALL BE TAKEN
BETWEEN CROSSHEAD AND TRUNNION.
67.1.8.5
Position tail rotor blades to
obtain dimensions of 4.032 ± 0.010 in. (102.413
±0.254 mm) between inboard face of crosshead
and outboard face of hub trunnion (detail C).
67.1.8.6
Holding specified position of
rotor, adjust link (6) to obtain 0.40 in. (10.16
mm) minimum clearance (detail D) with
bellcrank (7) and connect link to lever (5) with
bolt, washers, and nut. Torque nut 60 to 110
in.lbs. (6.78 to 12.43 Nm). Install cotter pin.
67.1.8.7
Check clevis on cylinder (15) for
1.22 in. (30.99 mm) dimension from end of
piston rod to center of clevis bolt hole.
67.1.8.8
Hold left pedal full forward. Push
down on hydraulic cylinder rod to bottom
actuator valve.
67.1.8.9
Maintaining specified rotor
position, adjust control tube (12) to fit on
bellcrank (13), then shorten tube one-half turn
and connect.
67.1.8.10
Place left pedal in full forward
position. Push down on tail rotor servo control
rod to center valve arm and remove control
system looseness.
67.1.8.11
Flap tail rotor assembly to one
extreme and check for clearance between blade
and tail rotor yoke using a 0.010 in. (0.254 mm)
feeler gage (Figure 67-7). Perform clearance
check on same blade with tail rotor flapped to
opposite extreme. Accomplish clearance check
on opposite blade in same manner.
Summary of Contents for ICA-D212-725
Page 2: ......
Page 19: ......
Page 47: ......
Page 55: ......
Page 71: ......
Page 73: ......
Page 75: ......
Page 95: ......
Page 121: ......
Page 137: ......
Page 149: ......
Page 249: ......
Page 251: ......
Page 325: ......
Page 327: ......
Page 473: ......
Page 475: ......
Page 531: ......
Page 581: ......
Page 707: ......
Page 729: ......