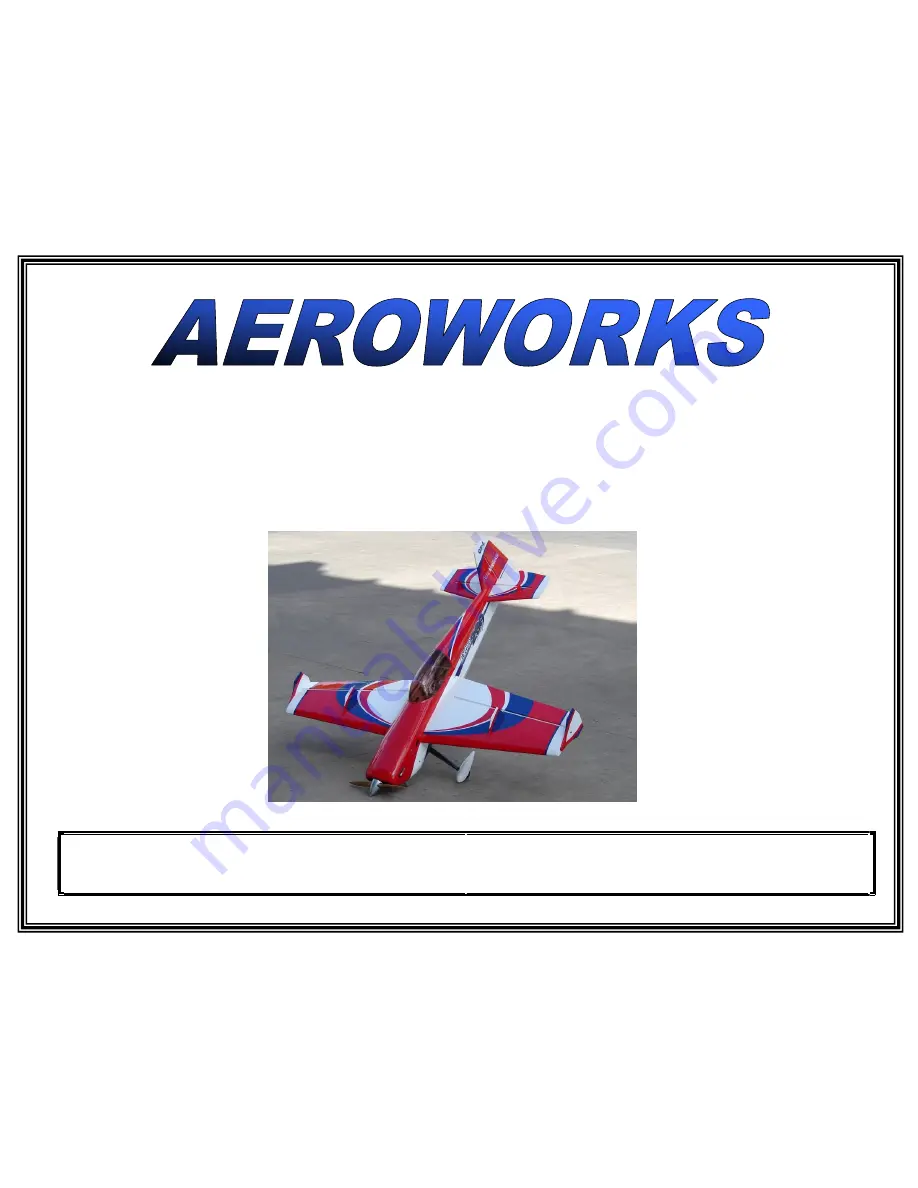
60cc Freestyle 260 ARF QB-L
(Quick Build Light)
ASSEMBLY MANUAL
AEROWORKS
4903 Nome Street, Denver, CO. 80239 - Phone 303-371-4222 - Fax 303-371-4320
E-mail - [email protected]
60cc Freestyle 260 ARF QB-L
(Quick Build Light)
ASSEMBLY MANUAL
AEROWORKS
4903 Nome Street, Denver, CO. 80239 - Phone 303-371-4222 - Fax 303-371-4320
E-mail - [email protected]