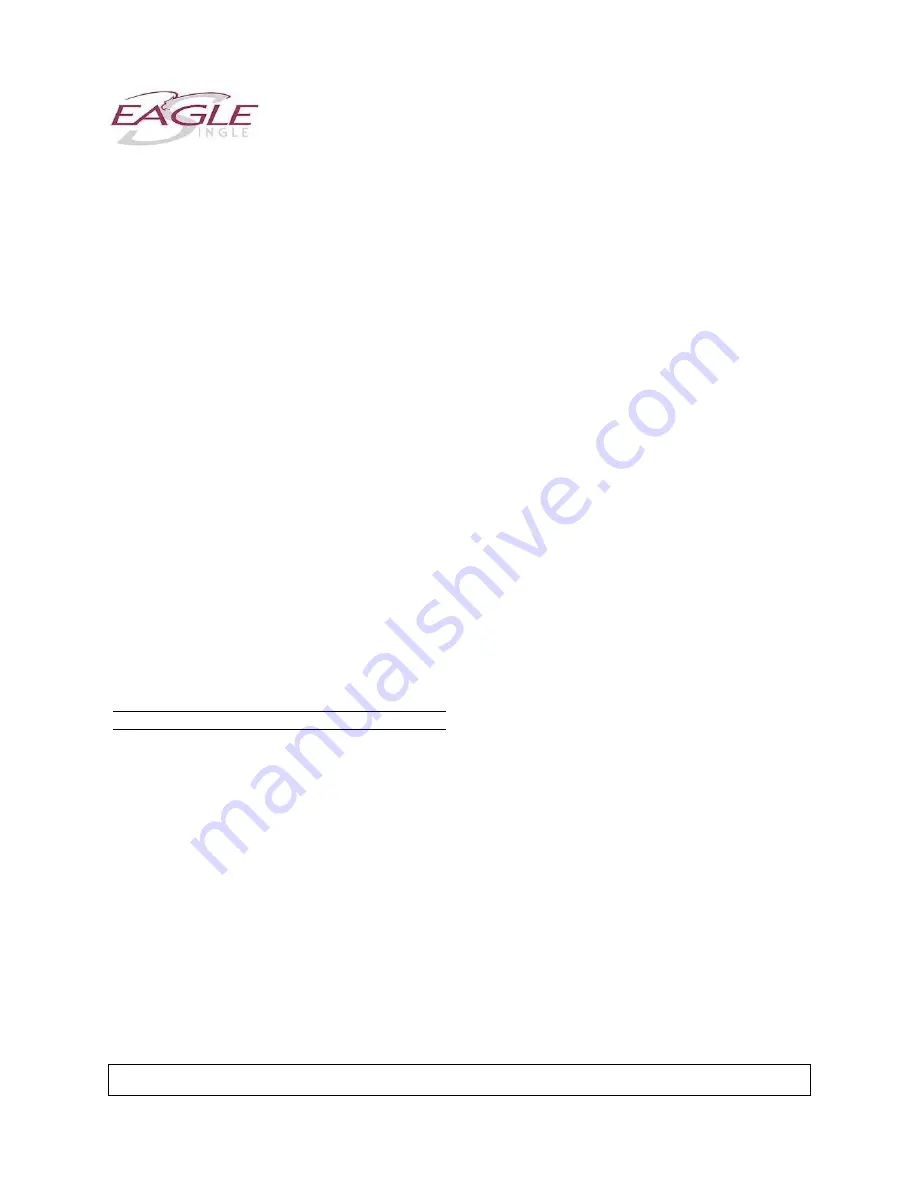
ICA-D212-725 (67)
Page 28 of 55
CHAPTER 67 – FLIGHT CONTROLS (67-00-00)
COPYRIGHT
2007 BY DART AEROSPACE LTD.
THIS DOCUMENT IS PRIVATE AND CONFIDENTIAL AND IS SUPPLIED ON THE EXPRESS CONDITION THAT IT IS NOT TO BE USED FOR ANY PURPOSE OR COPIED OR COMMUNICATED TO
ANY OTHER PERSON WITHOUT WRITTEN PERMISSION FROM DART AEROSPACE LTD.
Revision:
6
Date:
13.08.26
67.2.4
Minimum Collective Friction
Adjustment
67.2.4.1
Loosen friction nut (2, Figure 67-
9) completely.
67.2.4.2
With hydraulic power on, apply a
spring scale at middle within 0.5 in. (12.7 mm)) of
upper throttle grip. Check for 8 to 10 lbs. (35.58 to
44.48 N) force required to move stick upward
against sliding friction preload.
NOTE
If hydraulic power is not available,
adjustment may be checked by disconnecting
control tube (9) from arm (7). Scale should
indicate 13 to 14 lbs. (57.82 to 62.27 N)
sliding friction when stick is moved upward.
67.2.4.3
When adjustment is required,
remove access plate from floor at left of copilot
seat. Adjust bolt in clamp (13) on jackshaft elbow
to obtain proper friction.
67.2.5
Throttle Control Gears Adjustment
MATERIALS REQUIRED
NUMBER NOMENCLATURE
C-405 Lockwire
NOTE
If throttle controls do not operate smoothly,
perform following checks and adjustments
(Figure 67-12).
67.2.5.1
Detach control stick boot and
remove cover plates for access to throttle control
gears at both ends of collective stick and jackshaft
assembly.
67.2.5.2
At each end of jackshaft, verify
marked tooth of each flex shaft gear is mated in
tenth tooth space of gear sector. Also check at
each end of travel each gear sector is at least one
full tooth from rolling off mating gear.
67.2.5.3
Disconnect control tubes and
check for 0.003 to 0.008 in. (0.076 to 0.203 mm)
backlash of each gear sector with mating gear,
measured at control tube attach point of sector
arm in neutral position. With gear sector and flex
shaft in neutral position, a pull force of 4.5 lbs.
(20.01 N) is maximum allowable.
67.2.5.4
Determine type of spacer
installed between throttle gear sectors. If spacer
shown in view A is installed, adjust as outlined in
step 67.2.5.5. If spacer shown in view B is
installed, adjust as outlined in step 67.2.5.6.
67.2.5.5
Adjust gear sector backlash as
follows (view A):
67.2.5.5.1
Remove nut, washers, and bolt
securing gear sectors and spacer. Remove gear
sector, spacers (2) and shims.
67.2.5.5.2
Install gear sector with shims
between gear sector and support to provide
backlash of 0.003 to 0.008 in. (0.076 to 0.203
mm). Place spacers (2) between gear sector and
support and install bolt.
67.2.5.5.3 Measure
gap between spacer
and gear sector to determine thickness of shim
required to provide a snug fit.
67.2.5.5.4
Install shim between spacer and
gear sector and install and torque nut 50 to 70
in.Ibs. (5.65 to 7.91 Nm).
67.2.5.5.5
Check backlash of each gear
sector is 0.003 to 0.008 in. (0.076 to 0.203 mm).
With gear sector and flex shaft in a neutral
position, check gear sector will move when a
maximum force of 4.5 lbs. (20.01 N) is applied at
bolt hole with pull applied perpendicular to gear
sector. Install cotter pin in nut.
67.2.5.6
Adjust gear sector backlash as
follows (view B):
67.2.5.6.1
Remove bolt securing gear
sector.
67.2.5.6.2
Remove Iockwire and turn nuts
of spacer to decrease length of spacer.
Summary of Contents for ICA-D212-725
Page 2: ......
Page 19: ......
Page 47: ......
Page 55: ......
Page 71: ......
Page 73: ......
Page 75: ......
Page 95: ......
Page 121: ......
Page 137: ......
Page 149: ......
Page 249: ......
Page 251: ......
Page 325: ......
Page 327: ......
Page 473: ......
Page 475: ......
Page 531: ......
Page 581: ......
Page 707: ......
Page 729: ......