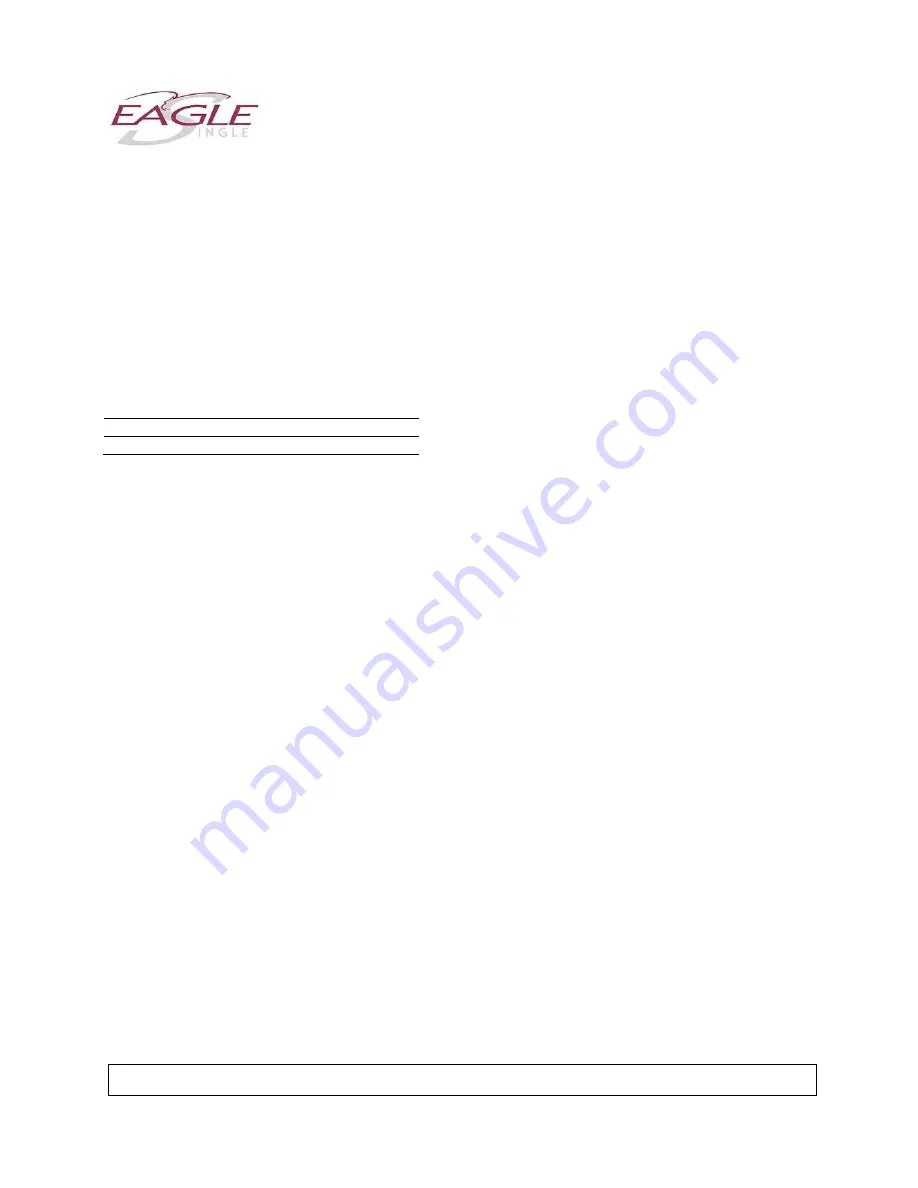
ICA-D212-725 (29)
Page 45 of 50
CHAPTER 29 – HYDRAULIC SYSTEM (29-00-00)
COPYRIGHT
2007 BY DART AEROSPACE LTD.
THIS DOCUMENT IS PRIVATE AND CONFIDENTIAL AND IS SUPPLIED ON THE EXPRESS CONDITION THAT IT IS NOT TO BE USED FOR ANY PURPOSE OR COPIED OR COMMUNICATED TO ANY
OTHER PERSON WITHOUT WRITTEN PERMISSION FROM DART AEROSPACE LTD.
Revision:
6
Date: 13.08.26
29.3.10.1.5 Support cylinder and remove two
bolts through trunnion plates (10). Remove plates
and cylinder.
29.3.10.1.6
If cylinder is being replaced, remove
clevis and hydraulic fittings for use on new
cylinder.
29.3.10.2
Inspection and repair
MATERIALS REQUIRED
NUMBER NOMENCLATURE
C-407 Abrasive
Pad
29.3.10.2.1
Grasp cylinder (4, Figure 29-10) just
below trunnion plates (10) and move the cylinder
laterally. Lateral movement of cylinder should be
from 0.003 to 0.050 in. (0.076 to 1.27 mm). There
should not be any evidence of binding.
29.3.10.2.2 Should tightness or binding be
found during inspection, remove cylinder (4) and
clean inside diameter of trunnion plate (10)
bushings using fine grade abrasive pad (C-407).
29.3.10.2.3
Inspect bearing in cylinder lever (11)
for tightness. Breakaway torque required to rotate
bearing shall not exceed 4.0 in-oz. (0.0282 Nm).
This inspection may be accomplished as follows:
29.3.10.2.3.1 Disconnect bellcrank (7 or 8) from
cylinder lever (11).
29.3.10.2.3.2 Place attachment bolt previously
removed in cylinder lever bearing.
29.3.10.2.3.3 Attach a spring scale to attachment
bolt and check force required to rotate bearing
(Figure 29-11).
29.3.10.2.3.4 Should torque required to rotate
cylinder lever (11, Figure 29-9) bearing exceed
limit, use an air drill motor and attaching hardware
previously removed to spin bearing until 4.0 in-oz.
(0.0282 Nm) or less with no radial play is achieved
(Figure 29-11).
29.3.10.2.3.5 If bearing does not meet torque
requirement, replace in accordance with HR
Textron Component Manual.
29.3.10.3
Installation
29.3.10.3.1 Position hydraulic cylinder (4, Figure
29-10) and two trunnion plates (10) on support
(9).
29.3.10.3.2 Install two bolts through trunnion
plates from left side, using aluminum washers
under bolt heads and nuts.
29.3.10.3.3 Align cylinder lever to bellcrank (7 or
8). Install spacer (6) between bearing of cylinder
lever (9) and right (inboard) tang of bellcrank (7
or 8). Install bolt head inboard with aluminum
washer under bolt head and nut. Install cotter
pin.
29.3.10.3.4 Assemble clevis (2) and nut (3) to
upper end of cylinder. Dimension from center of
clevis holes to end of cylinder is 1.22 in. (30.99
mm). Tighten clevis jamnut.
NOTE
Check security of check valve (12) before hoses
(5) are connected.
29.3.10.3.5 Attach control tube (1) to clevis with
bolt, two steel washers and nut. Install bolt with
head inboard. If raised pad on outside of clevis
(2) prevents washer under bolt head or nut from
seating properly, refer to Technical Bulletin 212-
79-21. Secure with cotter pin. Observe labels
and connect hydraulic pressure and return
fittings and hoses (5).
29.3.10.3.6 If bellcrank (7 or 8) was removed,
install with bolt heads inboard. Use washers
under head and nuts. Install cotter pins.
Summary of Contents for ICA-D212-725
Page 2: ......
Page 19: ......
Page 47: ......
Page 55: ......
Page 71: ......
Page 73: ......
Page 75: ......
Page 95: ......
Page 121: ......
Page 137: ......
Page 149: ......
Page 249: ......
Page 251: ......
Page 325: ......
Page 327: ......
Page 473: ......
Page 475: ......
Page 531: ......
Page 581: ......
Page 707: ......
Page 729: ......