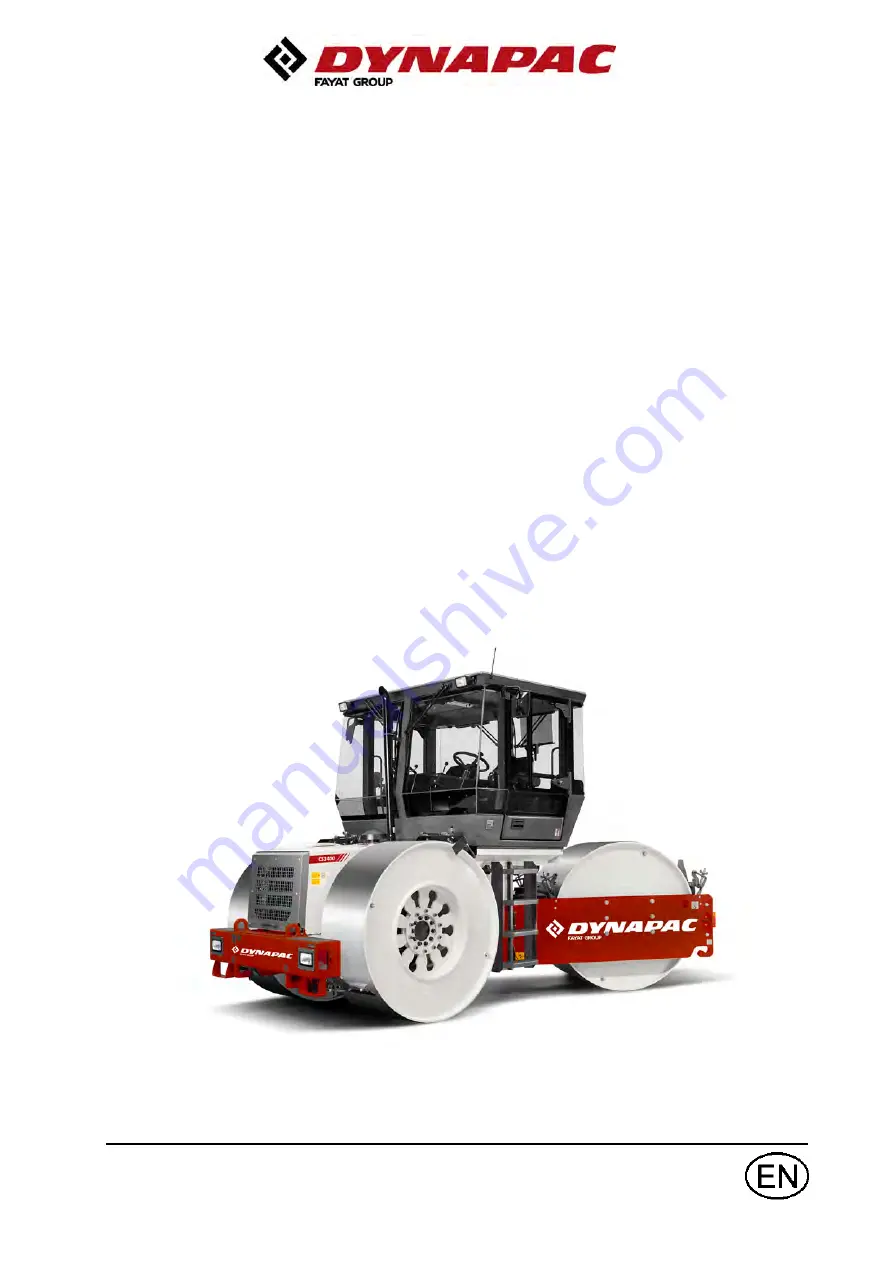
Instruction manual
Instruction manual
Operating & Maintenance
Operating & Maintenance
4812162501_F.pdf
4812162501_F.pdf
Static Three-drum Roller
Static Three-drum Roller
CS1400
CS1400
Engine
Engine
Deutz TD 3.6 L04 (IIIB/T4f)
Deutz TD 3.6 L04 (IIIB/T4f)
Serial number
Serial number
10000514xxA016632 -
10000514xxA016632 -
Translation of original instruction
Translation of original instruction
Reservation for changes
Reservation for changes
Printed in Sweden
Printed in Sweden
Summary of Contents for CS1400
Page 2: ......
Page 10: ...e 4812162501_F pdf 2018 04 25...
Page 14: ...Introduction 4812162501_F pdf 2018 04 25 4...
Page 22: ...Special instructions 4812162501_F pdf 2018 04 25 12...
Page 30: ...Technical specifications 4812162501_F pdf 2018 04 25 20...
Page 48: ...Machine description 4812162501_F pdf 2018 04 25 38...
Page 70: ...Operating instructions Summary 4812162501_F pdf 2018 04 25 60...
Page 72: ...Preventive maintenance 4812162501_F pdf 2018 04 25 62...
Page 80: ...Maintenance Maintenance schedule 4812162501_F pdf 2018 04 25 Service Checklist 70...
Page 92: ...Maintenance 50h 4812162501_F pdf 2018 04 25 82...
Page 98: ...Maintenance measures 500 h 4812162501_F pdf 2018 04 25 88...
Page 106: ...Maintenance 1000h 4812162501_F pdf 2018 04 25 96...
Page 117: ......
Page 118: ...Dynapac Compaction Equipment AB Box 504 SE 371 23 Karlskrona Sweden www dynapac com...