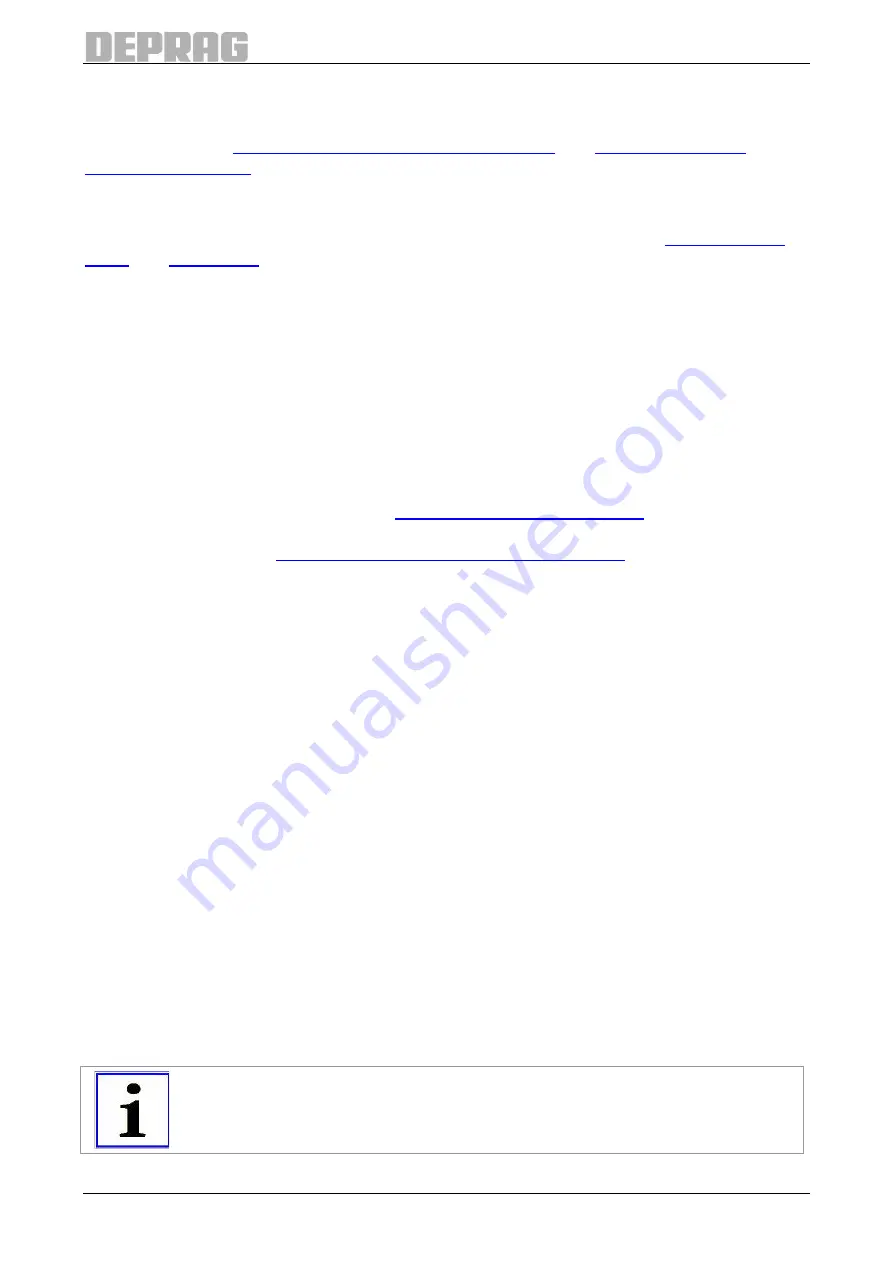
21
7.3 Method of operation of the sequence controller AST40
Upon activation of the AST40 sequence controller, the process information display
appears (also see
Figure 36: Process display, Alternative 1
).
The MINIMAT–EC-Servo screwdriver is controlled via the I/O interface SPS1. If an
optional fieldbus module is installed, then either the fieldbus module or the I/O interface
can perform the control task. Selecting this occurs in the menu (also see
).
Application of the start signal starts the screwdriving operation. This is started by the
program specified via the program selection.
7.4 Instructions on programming the sequence controller
The AST40 sequence controller is already pre-configured in its delivered state.
A screwdriving program which functions with the accompanying MINIMAT–EC-Servo
screwdriver also already present. The screw assembly programs and settings must
however be adjusted to the present application case.
Basic settings and parameter changes in the screwdriving programs can be made directly
in the AST40 sequence controller, see
. If the screwdriving
programs are to be changed or new ones are to be created, then this must be done via the
web user interface, see
10.3.4 Menu Area – Screwdriving sequence
. Standard programs
like Torque Screwdriving, Rotation angle screwdriving and Rotation angle unscrewing can
be created and parameterized directly on the AST40 sequence controller.
7.5
Connection to a higher level controller
Signal sequence of a screwdriving cycle (independent of the control method):
Basic prerequisites:
•
Presence of the program selection (may be present continuously, but it is evaluated
only when the start signal is applied)
Communication:
1. Sensing of Ready output, signal HIGH? The controller is ready for screw fixing
operation.
2. Apply HIGH signal at the Program start input
3. Sensing of Ready output, signal LOW? The screw fixing operation has commenced.
4. Sensing the outputs OK and NIO, is one of the signals HIGH? The screw fixing
operation has terminated.
5. Signal LOW at the program start input, and, if necessary, change the bit pattern for
program selection
6. Wait for Ready output, signal HIGH? Controller is again ready for screwdriving.
7. Continue as given in point 1 - new screwdriving cycle
With program start, the Ready signal as well as OK/NIO are set to LOW.
The subsequent HIGH of OK or NIO indicates the end of the screwdriver cycle.
IMPORTANT
The start signal must be 150ms LOW between two screwdriving cycles.