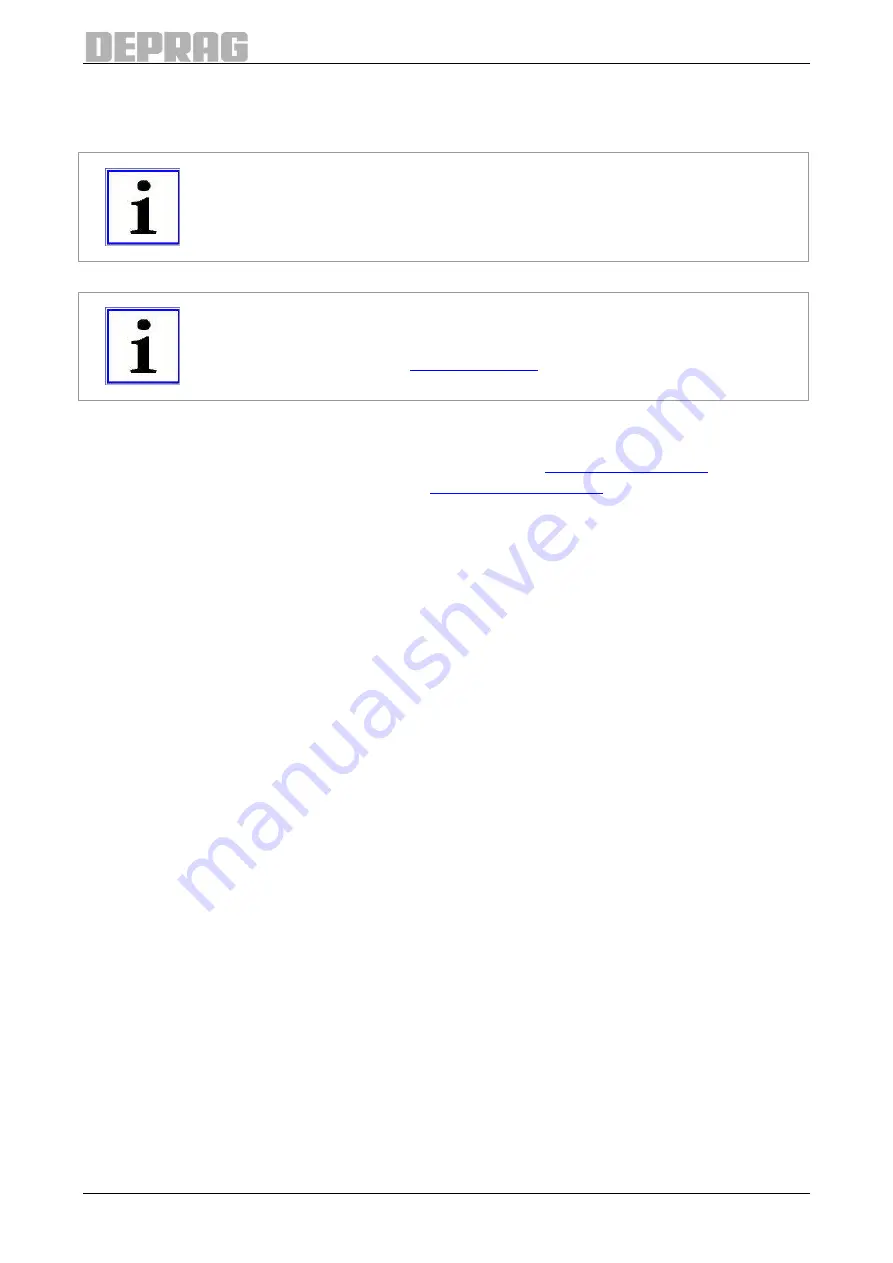
134
14.3 Calibrating the touch display
It is possible that the touch display may need to be re-calibrated due to aging and wear.
IMPORTANT
Calibration must be carried out directly on the display, even if you start the
calibration process through the web-based user interface.
IMPORTANT
Use the Touch-Pen (see
) for calibrating the display.
The calibration must be carried using the following steps:
1. Start calibration either directly in the display (see
the web-based user interface (see
menu system by touching or clicking on the button "Start". The display restarts.
2. After a while, you can see the words "TSLIB calibration utility – Touch crosshair to
calibrate" on the display. If possible, touch the point in the center of the crosshair
at the top left, then at the top right, bottom right, bottom left and then the center.
3. Wait until the display has finished running up again.