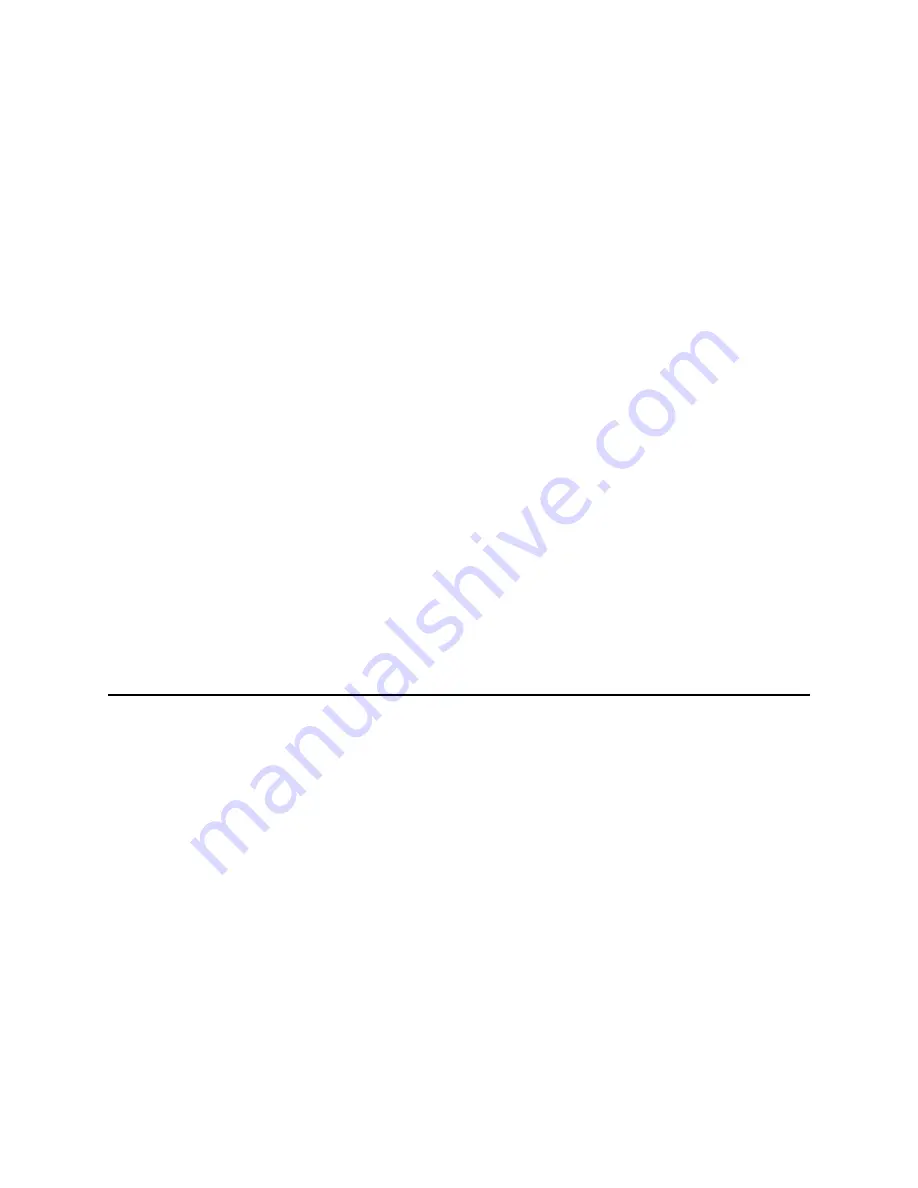
Page 63
SY-01314 Flash Error
Warning! EEPROM flash write error.
Possible Cause 1:
A transmission problem occurred.
Solution 1:
Send the file or data again. You can repeat this action several
times.
Possible Cause 2:
The printer EEPROM does not accept the data or
setting.
Solution 2:
Power off the printer. Wait one minute, and then power on the
printer. Repeat the action again.
Possible Cause 3:
The printer EEPROM does not accept the flash file.
Solution 3:
Warning:
Do NOT power off the printer DURING a firmware
download. Send the file or repeat the action again.
If you cannot fix the problem,
contact your service provider for assistance.
Summary of Contents for SP75 Plus
Page 1: ...SP75 Printer Guide 559455 001 Rev A March 2005 ...
Page 81: ...Page 76 Turn the page to see information about the next message ...
Page 93: ...Page 88 Turn the page to see information about the next message ...
Page 99: ...Page 94 Turn the page to see information about the next message ...
Page 109: ...Page 104 Related Topics Cleaning the printer on page 21 ...
Page 121: ...Page 116 Turn the page to see information about the next message ...
Page 134: ......