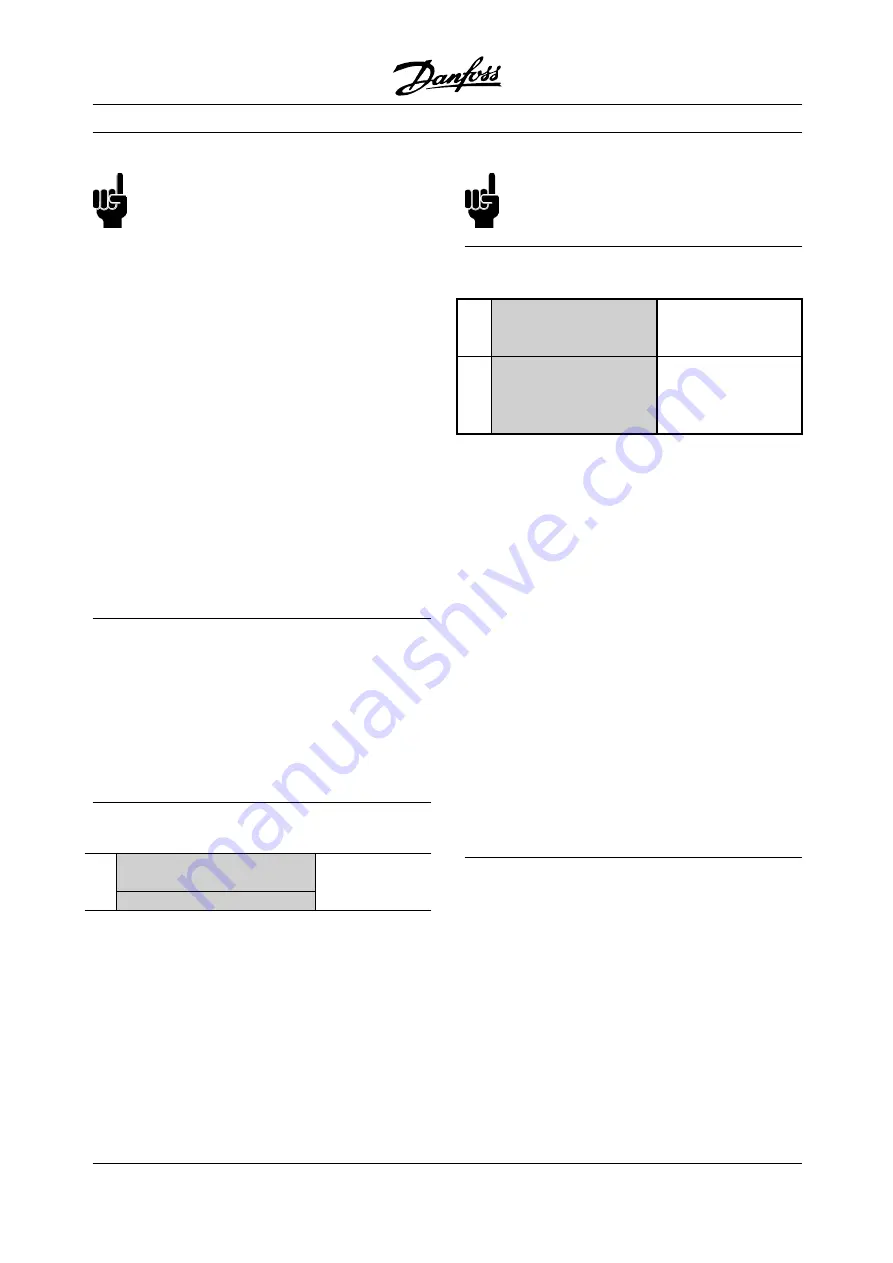
Decentral Solutions
NOTE
If an unshielded/unarmoured cable is used,
some EMC requirements are not complied with,
see
EMC test results
in the Design Guide.
If the EMC specifications regarding emission are
to be complied with, the motor cable must be
shielded/armoured, unless otherwise stated for the
RFI filter in question. It is important to keep the
motor cable as short as possible so as to reduce the
noise level and leakage currents to a minimum. The
motor cable shield must be connected to the metal
cabinet of the variable frequency drive and to the metal
cabinet of the motor. The shield connections are to
be made with the biggest possible surface area (cable
clamp). This is enabled by different installation devices
in different variable frequency drives. Mounting with
twisted shield ends (pigtails) is to be avoided, since
these spoil the shielding effect at high frequencies. If
it is necessary to break the shield to install a motor
isolator or motor relay, the shield must be continued
at the lowest possible HF impedance.
■
Motor thermal protection
The electronic thermal relay in UL approved variable
frequency drives has received the UL approval for single
motor protection, when parameter 128
Motor thermal
protection
has been set for
ETR Trip
and parameter
105
Motor current, I
M, N
has been programmed to
the rated motor current (see motor nameplate).
■
Brake resistor
No. 81 (optional
function)
82 (optional
function)
Brake resistor
terminals
R-
R+
The connection cable to the brake resistor must
be shielded/armoured. Connect the shield to the
metal cabinet of the variable frequency drive and to
the metal cabinet of the brake resistor by means of
cable clamps. Dimension the cross-section of the
brake cable to match the brake torque.
See chapter
Dynamic Braking
in the
Design Guide
MG.90.FX.YY
for sizing of brake resistors.
NOTE
Please note that voltages up to 850 V DC
occur on the terminals.
■
Control of mechanical brake
No. 122
(optional
function)
123
(optional
function)
MBR-
MBR+
Mechanical brake
(UDC=0.45 X
electrical Voltage)
Max 0.8 A
In lifting/lowering applications you need to be able
to control an electromagnetic brake. The brake
is controlled using the special mechanical brake
control/supply terminals 122/123.
When the output frequency exceeds the brake cut
out value set in par. 138, the brake is released if the
motor current exceeds the preset value in parameter
140. When stopping the brake is engaged when the
output frequency is less than the brake engaging
frequency, which is set in par. 139.
If the variable frequency drive is at alarm status
or in an overvoltage situation the mechanical
brake is cut in immediately.
If not using the special mechanical brake control/supply
terminals (122-123), select
Mechanical brake
control
in parameter 323 or 341 for applications
with an electromagnetic brake.
A relay output or digital output (terminal 46) can be used.
See
Connection of mechanical brake
for further details.
MG.90.F2.22 - VLT is a registered Danfoss trademark
84