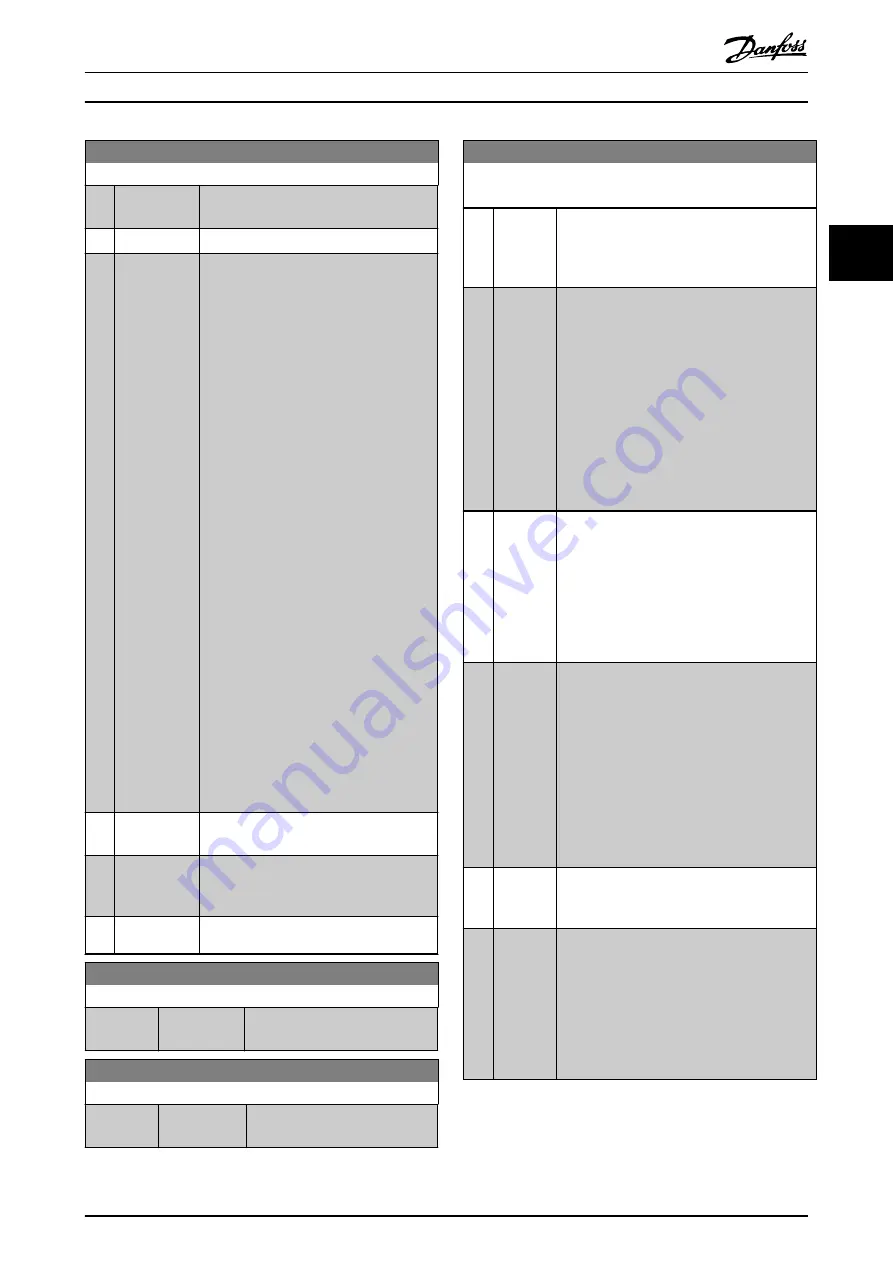
1-80 Function at Stop
Option:
Function:
[1]
DC hold
Energizes motor with a DC holding current
(see
).
[2]
Motor check
Checks if a motor has been connected.
[3]
Pre-
magnetizing
Builds up a magnetic field while the motor
is stopped. This allows the motor to
produce torque quickly at subsequent start
commands (asynchronous motors only). This
Pre-magnetizing function does not help the
very first start command. Two different
solutions are available to pre-magnetize the
machine for the first start command:
1. Start the frequency converter
with a 0 RPM reference and wait 2
to 4 rotor time constants (see
below) before increasing the
speed reference.
2a. Set
to the
desired pre-mag time (2 to 4 rotor
time constants - see below).
2b. Set
to
either
[0] DC-hold
or
[1] DC-Brake
.
Set the DC-hold or DC-brake
current magnitude (
or
)
to be equal to I_pre-mag = Unom/
(1.73 x Xh)
Sample rotor time constants =
(Xh+X2)/(6.3*Freq_nom*Rr)
1 kW = 0.2 seconds
10 kW = 0.5 seconds
100 kW = 1.7 seconds
1000 kW = 2.5 seconds
[4]
DC Voltage
U0
When the motor is stopped, the P1-55 [0]
parameter defines the voltage at 0Hz.
[5]
Coast at low
reference
When the reference is below
1-81 Min Speed
for Function at Stop [RPM]
, the motor is
disconnected from the frequency converter.
[6]
Motor check,
alarm
1-81 Min Speed for Function at Stop [RPM]
Range:
Function:
Size related
*
[0 - 600 RPM] Set the speed at which to activate
1-80 Function at Stop
.
1-82 Min Speed for Function at Stop [Hz]
Range:
Function:
Size related
*
[0.0 - 20.0 Hz] Set the output frequency at which
to activate
1-80 Function at Stop
.
1-83 Precise Stop Function
FC 302 only.
Option:
Function:
[0]
*
Precise
ramp stop
Only optimal when the operational speed - of
e.g. the conveyor belt - is constant. This is an
open loop control. Achieves high repetitive
precision at the stopping point.
[1]
Cnt stop
with reset
Counts the number of pulses, typically from an
encoder and generates a stop signal after a pre-
programmed number of pulses -
- has been received at T29
or T33 [30].
This is a direct feedback with one-way closed
loop control.
The counter function is activated (starts timing)
at the edge of the start signal (when it changes
from stop to start). After each precise stop the
number of pulses counted during ramp down
to 0 rpm is reset.
[2]
Cnt stop
w/o reset
Same as [1] but the number of pulses counted
during ramp down to 0 rpm is deducted from
the counter value entered in
.
This reset function can for example be used to
compensate for the extra distance done during
ramping down and to reduce the impacts of
gradual wear of mechanical parts.
[3]
Speed
comp
stop
Stops at precisely the same point, regardless of
the present speed, the stop signal is delayed
internally when the present speed is lower than
the maximum speed (set in
).
The delay is calculated on the basis of the
reference speed of the frequency converter and
not on the basis of the actual speed. Please
therefore make sure that the frequency
converter has ramped up before you activate
the speed compensated stop.
[4]
Com cnt
stop w/rst
Same as [3] but after each precise stop the
number of pulses counted during ramp down
to 0 rpm is reset.
[5]
Comp cnt
stop w/o
r
Same as [3] but the number of pulses counted
during ramp down to 0 rpm is deducted from
the counter value entered in
.
This reset function can for example be used to
compensate for the extra distance done during
ramping down and to reduce the impacts of
gradual wear of mechanical parts.
The Precise Stop Functions are advantageous in
applications where high precision is required.
If you use a standard stop command the accuracy is
determined by the internal task time. That is not the case
Parameter Descriptions
VLT
®
AutomationDrive Programmming Guide
MG33ME02 - VLT
®
is a registered Danfoss trademark
45
3
3