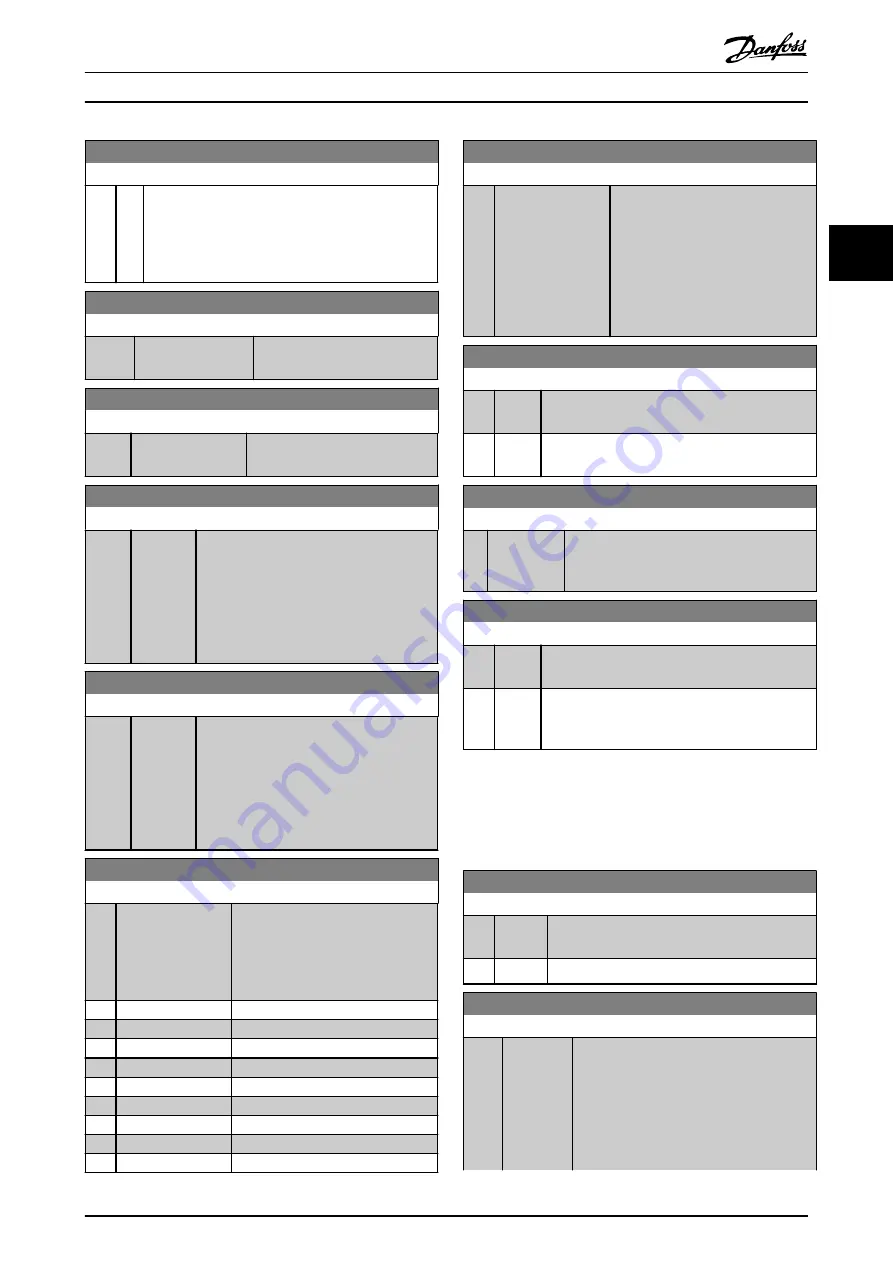
7-40 Process PID I-part Reset
Option: Function:
[1]
Yes Select
[1] Yes
to reset the I-part of the process PID
controller. The selection will automatically revert to
[0]
No
. Resetting the I-part makes it possible to start from
a welldefined point after changing something in the
process, e.g. changing a textile roll.
7-41 Process PID Output Neg. Clamp
Range:
Function:
-100 %
*
[ -100 - par. 7-42 %] Enter a negative limit for the
process PID controller output.
7-42 Process PID Output Pos. Clamp
Range:
Function:
100 %
*
[ par. 7-41 - 100 %] Enter a positive limit for the
process PID controller output.
7-43 Process PID Gain Scale at Min. Ref.
Range:
Function:
100 %
*
[0 - 100
%]
Enter a scaling percentage to apply to the
process PID output when operating at the
minimum reference. The scaling percentage
will be adjusted linearly between the scale
at min. ref. (
7-43 Process PID Gain Scale at
) and the scale at max. ref.
7-44 Process PID Gain Scale at Max. Ref.
7-44 Process PID Gain Scale at Max. Ref.
Range:
Function:
100 %
*
[0 - 100
%]
Enter a scaling percentage to apply to the
process PID output when operating at the
maximum reference. The scaling percentage
will be adjusted linearly between the scale
at min. ref. (
7-43 Process PID Gain Scale at
) and the scale at max. ref.
7-44 Process PID Gain Scale at Max. Ref.
7-45 Process PID Feed Fwd Resource
Option:
Function:
[0]
*
No function
Select which drive input should be
used as the feed forward factor. The
FF factor is added directly to the
output of the PID controller. This
increases dynamic performance.
[1]
Analog input 53
[2]
Analog input 54
[7]
Frequency input 29
[8]
Frequency input 33
[11] Local bus reference
[20] Digital pot.meter
[21] Analog input X30-11
[22] Analog input X30-12
[29] Analog Input X48/2
7-45 Process PID Feed Fwd Resource
Option:
Function:
[32] Bus PCD
Selects a bus reference configured by
. Change
for the
bus used in order to make the feed-
forward available in
. Use index 1 for feed-forward
[748] (and index 2 for reference
[1682]).
7-46 Process PID Feed Fwd Normal/ Inv. Ctrl.
Option:
Function:
[0]
*
Normal Select
[0] Normal
to set the feed forward factor to
treat the FF resource as a positive value.
[1]
Inverse Select
[1]Inverse
to treat the FF resource as a
negative value.
7-48 PCD Feed Forward
Range:
Function:
0
*
[0 - 65535 ] Read-out parameter where the bus
7-45 Process PID Feed Fwd Resource
[32]) can
be read.
7-49 Process PID Output Normal/ Inv. Ctrl.
Option:
Function:
[0]
*
Normal Select
[0] Normal
to use the resulting output from
the process PID controller as is.
[1]
Inverse Select
[1] Inverse
to invert the resulting output
from the process PID controller. This operation is
performed after the feed forward factor is applied.
3.9.6 7-5*Ext. Process PID Ctrl.
Parameter group 7-5* is only used if
is set to
[7] Extended PID speed CL
or
[8] Extended PID
Speed OL
.
7-50 Process PID Extended PID
Option:
Function:
[0]
Disabled Disables the extended parts of the process PID
controller.
[1]
*
Enabled Enables the extended parts of the PID controller.
7-51 Process PID Feed Fwd Gain
Range:
Function:
1.00
*
[0.00 -
100.00 ]
The feed forward is used to obtain the
desired level, based on a well-known signal
available. The PID controller then only takes
care of the smaler part of the control,
necessary because of unknown characters.
The standard feed fwd factor in
is always related to
Parameter Descriptions
VLT
®
AutomationDrive Programmming Guide
MG33ME02 - VLT
®
is a registered Danfoss trademark
103
3
3