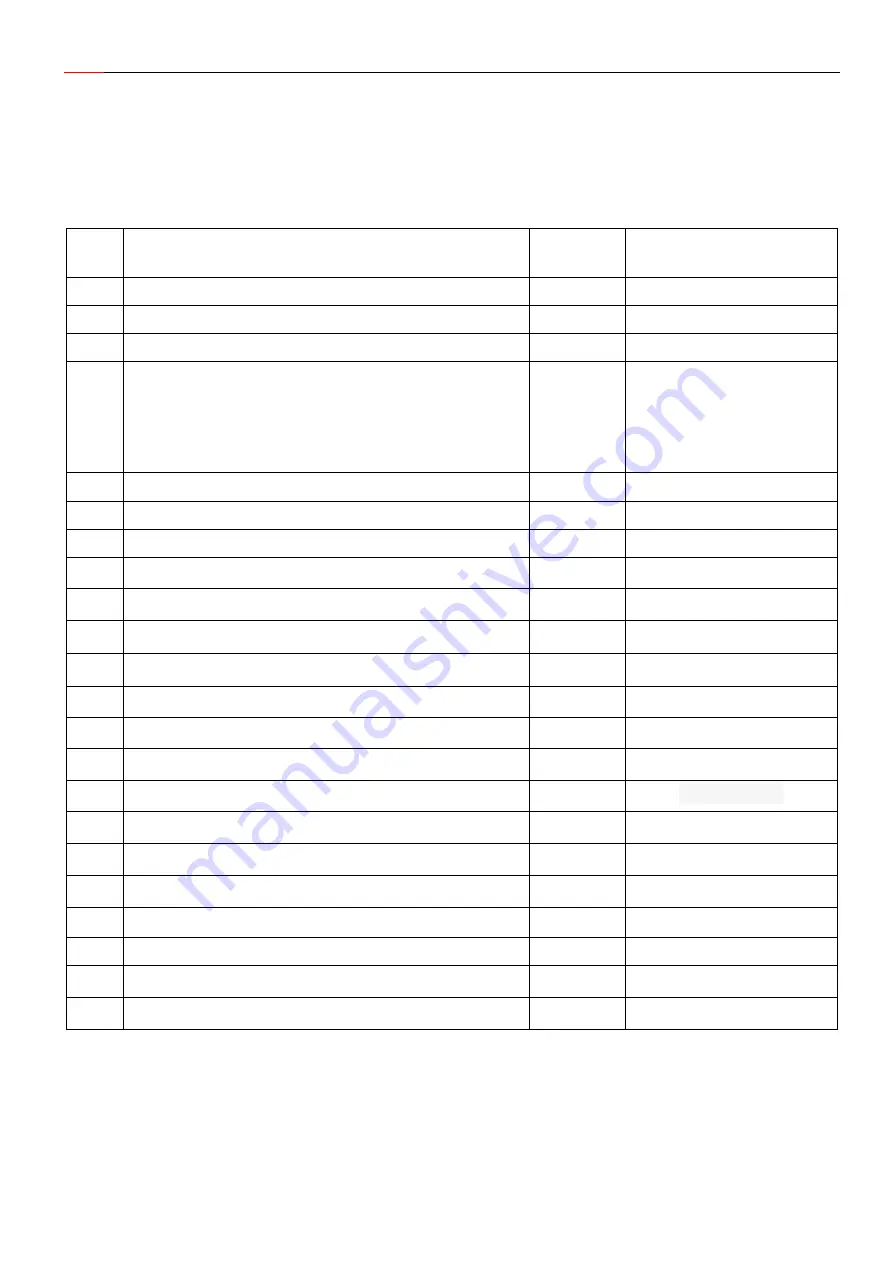
Cynko
Met
RS-1500
25
4.
Information regarding use
4.1
Technical characteristics.
Table 2. Basic technical specifications of the spreader
Item
no.
Content
Unit of
measure
RS-1500
1.
Total length
mm
5890
2.
Total width
mm
1600
3.
Total height
mm
2065
4.
Dimensions of cargo bed:
•
Length
•
width
•
height
mm
3960
1260
750
5.
cargo capacity
m
3
3.7
6.
Loading surface
m
2
4.99
7.
Lift of the loading surface
mm
1060
8.
Road clearance
mm
300
9.
Vehicle weight
kg
1700
10. Gross vehicle weight rating
(1)
kg
2030
11.
Permissible loading capacity
(1)
kg
3000
12. Track of wheels
mm
1200
13. Tire size
400/60-15.5 14 PR
14. Tires Speed Index
A8 (40km/h)
15. Tires Load Index
145 (2900 KG)
16. Max. tire pressure
kPa
350
17. Max. pressure in hydraulic system
bar/MPa
160/16
15. Rated voltage
V
12 V
16. Permissible design speed
(2)
km/h
30
17. Permissible max. speed during work
km/h
8
18. Power requirement
kW/KM
33/45
19. Noise emission
(3)
dB
78-82
(1)
– capacity depends on the equipment of the spreader
(2)
- The permitted speed of the spreader moving on public roads in Poland is 30 km / h (according to the Act of 20 June 1997,
"the Road Traffic Law", art. 20). In countries where the machine is operated, observe the restrictions associated with the
relevant national law on road traffic.
(3)
- During work in idle gear. The value is lower during spreading due to attenuation.
Summary of Contents for RS-1500
Page 67: ...CynkoMet RS 1500 67 NOTES...
Page 70: ...CynkoMet RS 1500 70 Table 1 Bottom frame load carrying beam drawbar...
Page 72: ...CynkoMet RS 1500 72 Table 2 750 wall...
Page 75: ...CynkoMet RS 1500 75 Table 4 Drive transmission system Table 4 Drive transmission system...
Page 82: ...CynkoMet RS 1500 82 Table 9 Conveyor drive...
Page 84: ...CynkoMet RS 1500 84...
Page 87: ...CynkoMet RS 1500 87 Table 11 A2H adapter...
Page 90: ...CynkoMet RS 1500 90 Table 13 Spreader of adapter A2H...
Page 92: ...CynkoMet RS 1500 92 Table 14...
Page 94: ...CynkoMet RS 1500 94 Table 15 Conveyor...
Page 96: ...CynkoMet RS 1500 96...