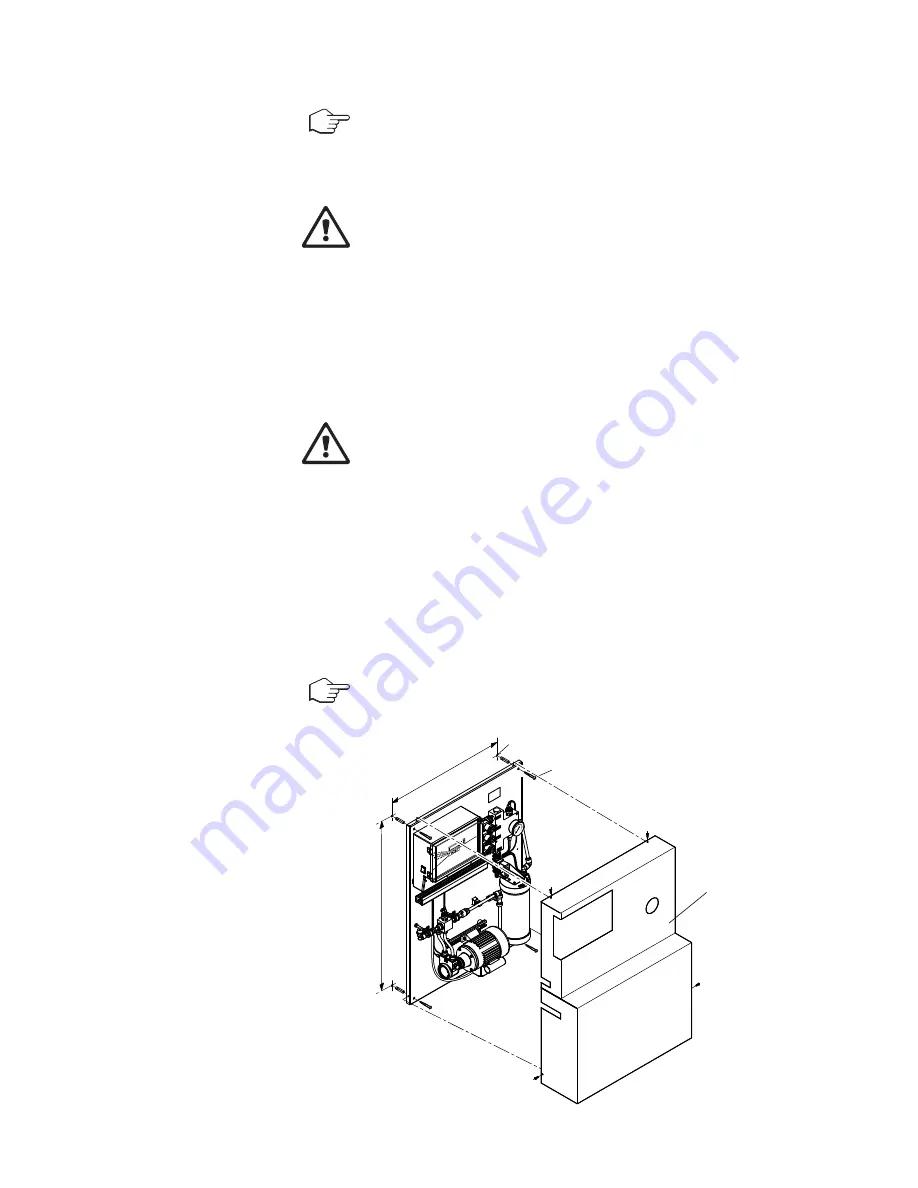
35
4.3
Installation of the central unit
Location of the central unit
– The central unit is designed for
wall mounting
. Make sure the construc-
tion (wall, pillar, etc.) to which the central unit is to be mounted, offers
a sufficiently high loadbearing capacity and is suitable for the installa
-
tion.
Caution!
Do not mount the central unit to vibrating parts
.
– The central unit must be installed only in a
location having a water
drain
on the floor. If this is not possible, it is mandatory to provide
water
sensors
to safely interrupt water supply in case of leakage. Furthermore,
choose a suitable location that prevents damage to material assets in
case of leakage.
– Make sure the ambient conditions at the desired location meet the
specifications outlined in chapter 8.2.
–
Danger of damage!
Do not install the central unit in exposed locations
or locations with heavy dust load. Use the optional casing (option “Z408”)
to protect the central unit from damage and soiling,
or use the central
unit with spray circle discharge integrated in two protective cab inets
(option “Z409”)
.
– Install the central unit so that the water hoses between the connector
box and the nozzles are as short as possible (
max. 10 m
).
–
Install the central unit in a freely accessible location providing enough
space for operation and maintenance.
Installation of the central unit
Use the provided fastening set to mount the central unit to the wall or to
the monobloc. If for some special reasons an installation with the sup-
plied fastening material is not feasible, choose a type of installation that is
equally stable.
Important!
Use a level for accurate horizontal adjustment.
Z408
ø10 mm
ø8x50 mm
900 mm
640 mm