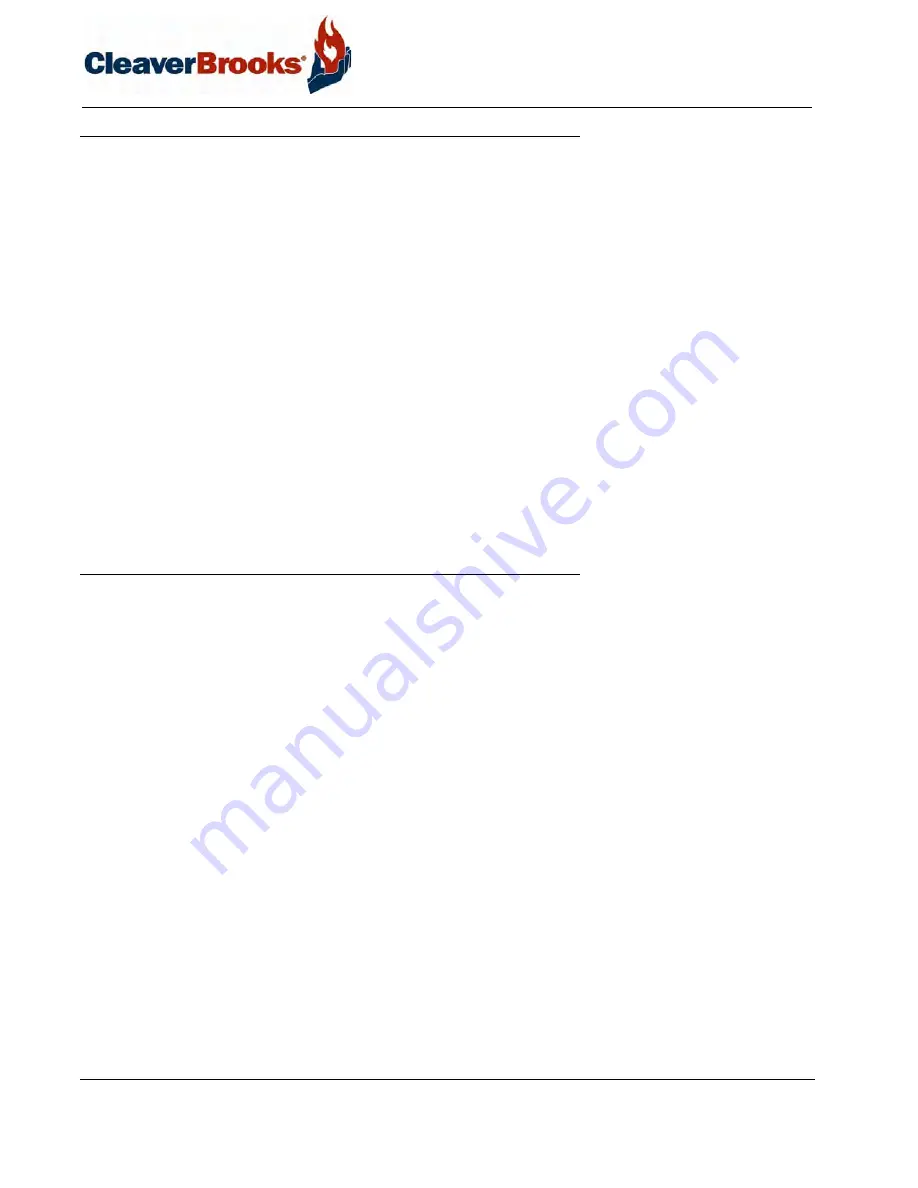
Burner Operation and Control
2-20
750-91 (revised 2009)
Model CB-LE Packaged Boiler Manual
2.13 — Gas Fuel Flow
Metered gas from the utility flows through the pressure regulator at a reduced pressure suitable to burner require-
ments, through the main gas shutoff cock, main gas valve(s), and modulating butterfly gas valve to the non-premix
orifice-type burner.
The main gas valve is of the normally closed type, and is opened (energized) in proper sequence by the program-
ming relay.
The butterfly gas valve modulates the flow of gas from low through high fire settings. The position of the butterfly
valve disc is governed by the gas modulating cam. The butterfly gas valve, and the air control damper are controlled
simultaneously by the modulating motor to proportion combustion air and fuel for changes in load demand.
The gas flow rate required for rated burner input depends upon the heating value (Btu/cubic foot) of the gas sup-
plied. The gas pressure regulator adjusts the gas pressure (flow rate) to the entrance of the gas train. The regulator
is not always supplied with the burner, but may be provided by others.
The main gas valves cannot be energized (opened) unless the combustion air proving switch is closed to indicate a
sufficient supply of combustion air. The low gas pressure and high gas pressure switches must be closed to prove
sufficient, but not excessive, gas fuel pressure.
2.14 — Modulating Firing
The modulating motor, through a linkage arrangement, controls the air damper and the butterfly gas valve, or the
oil metering valve, to maintain a constant air/fuel ratio throughout the firing range.
During burner operation, the motor is controlled by a modulating pressure control on a steam boiler, or by a mod-
ulating temperature control on a hot water boiler. A manually operated potentiometer is provided to permit posi-
tioning of the motor at the desired burner firing rate. The potentiometer is used primarily for initial or subsequent
checking and setting of fuel input. Normal operation should be with the manual-automatic switch in the “auto-
matic” position and under the control of the modulating control.
The modulating motor (commonly called a damper motor) is reversible. It has an internal limit switch that restricts
shaft rotation to 90º. During normal operation the motor will move in either direction or stop at any position
within the range.
The motor potentiometer is electrically connected to a matching potentiometer in the modulating control. Chang-
ing steam pressure or water temperature alters the electrical resistance of the modulating controller potentiometer.
The change in resistance compels an integral balancing relay to start, stop, or reverse the motor rotation. Rotation
in either direction continues until the resistance ratio of the two potentiometers is equal.
When the resistance ratio is equal, the motor stops in a position that allows the proper fuel and combustion air
flow to meet operating demands.
A feature designed into the circuitry maintains the modulating motor in the low-fire position during ignition and
keeps it there until the main flame is established. A low-fire switch, integral to the motor, is actuated by the rotation
Summary of Contents for CBLE
Page 14: ...xiv 750 91 revised 2009 Model CB LE Packaged Boiler Manual...
Page 48: ...Burner Operation and Control 2 22 750 91 revised 2009 Model CB LE Packaged Boiler Manual...
Page 64: ...Waterside Care and Requirements 3 16 750 91 revised 2009 Model CB LE Packaged Boiler Manual...
Page 72: ...Sequence of Operation 4 8 750 91 revised 2009 Model CB LE Packaged Boiler Manual...
Page 158: ...Inspection and Maintenance 8 38 750 91 revised 2009 Model CB LE Packaged Boiler Manual...
Page 166: ...Parts 9 8 750 91 revised 2009 Model CB LE Packaged Boiler Manual Control Panel...
Page 168: ...Parts 9 10 750 91 revised 2009 Model CB LE Packaged Boiler Manual 9 2 7 Front Head Electrical...
Page 170: ...Parts 9 12 750 91 revised 2009 Model CB LE Packaged Boiler Manual 9 2 9 Front Head Insulation...
Page 174: ...Parts 9 16 750 91 revised 2009 Model CB LE Packaged Boiler Manual 9 2 12 Light Oil Air Piping...
Page 176: ...Parts 9 18 750 91 revised 2009 Model CB LE Packaged Boiler Manual 9 2 13 Heavy Oil Air Piping...
Page 182: ...Parts 9 24 750 91 revised 2009 Model CB LE Packaged Boiler Manual 9 2 16 IFGR Impeller...
Page 184: ...Parts 9 26 750 91 revised 2009 Model CB LE Packaged Boiler Manual 9 2 18 Temperature Controls...
Page 186: ...Parts 9 28 750 91 revised 2009 Model CB LE Packaged Boiler Manual W C Main Aux...
Page 193: ......
Page 194: ...e mail info cleaverbrooks com Web Address http www cleaverbrooks com...