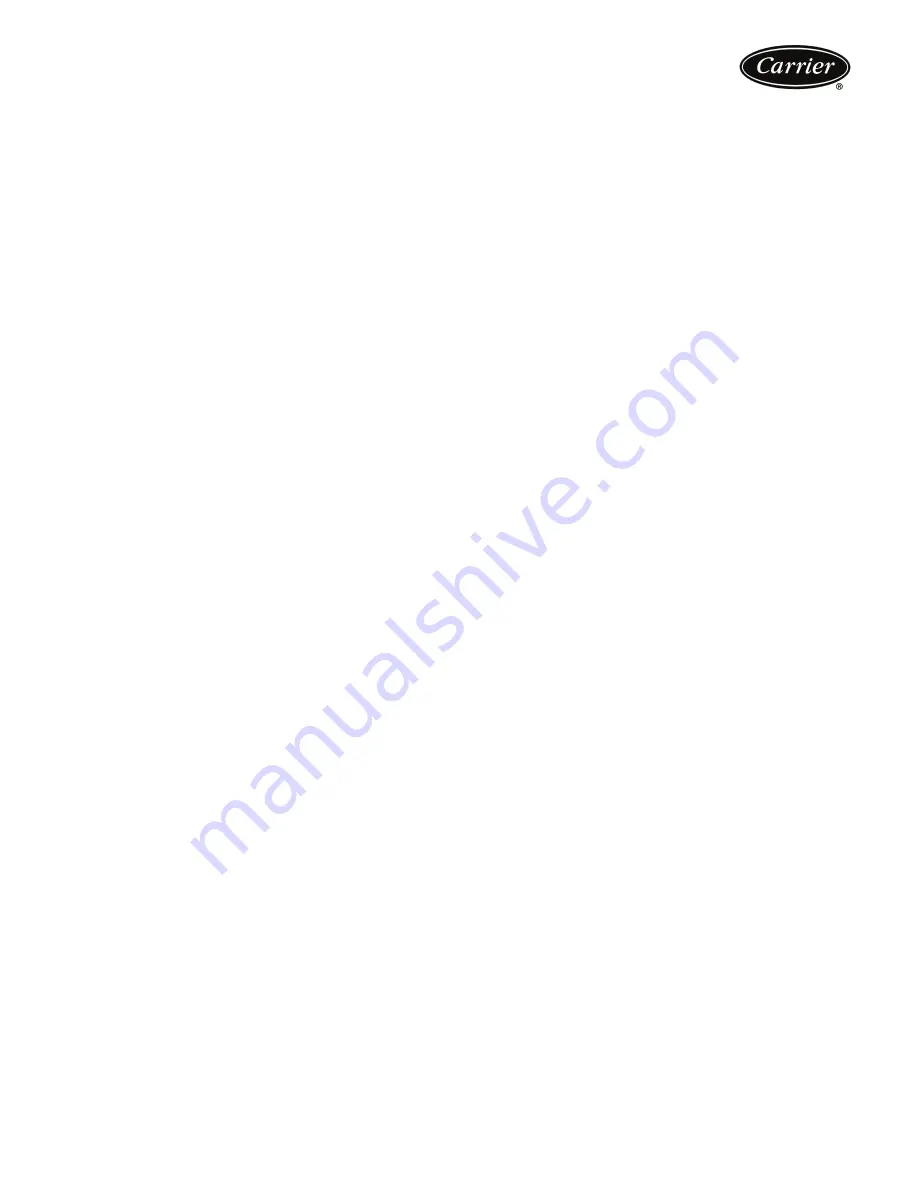
70
3. Assembled condenser coils shall be leak tested
and pressure tested at 656 psig (4522 kPa).
G. Refrigeration Components:
Refrigerant circuit components shall include filter
drier, moisture indicating sight glass, electronic
expansion device, discharge and liquid service valves
(sizes 070-090 only) and complete operating charge
of sides both refrigerant R-410A and compressor
oil.
H. Controls, Safeties, and Diagnostics:
1. Unit controls shall include the following mini-
mum components:
a. Microprocessor with non-volatile memory.
Battery backup system shall not be accepted.
b. Separate terminal block for power and
controls.
c. Control transformer to serve all controllers,
relays, and control components.
d. ON/OFF control switch.
e. Replaceable solid-state controllers.
f. Pressure sensors shall be installed to mea-
sure suction and discharge pressure for each
circuit. Thermistors shall be installed to mea-
sure cooler entering and leaving fluid tem-
peratures, outdoor ambient temperature,
and suction temperature. Provision for field
installation of accessory sensor to measure
compressor return gas temperature.
2. Unit controls shall include the following
functions:
a. Automatic circuit lead/lag for dual circuit
chillers.
b. Hermetic scroll compressors are mainte-
nance free and protected by an auto-adaptive
control that minimizes compressor wear.
c. Capacity control based on leaving chilled
fluid temperature and compensated by rate
of change of return-fluid temperature with
temperature set point accuracy to 0.1° F
(0.06° C).
d. Limiting the chilled fluid temperature pull-
down rate at start-up to an adjustable range
of 0.2° F to 2° F (0.11° C to 1.1° C) per
minute to prevent excessive demand spikes
at start-up.
e. Seven-day time schedule.
f. Leaving chilled fluid temperature reset from
return fluid and outside air temperature.
g. Chilled water pump start/stop control and
primary/standby sequencing to ensure equal
pump run time.
h. Dual chiller control for parallel chiller appli-
cations without addition of hardware
modules and control panels (additional
thermistors and wells are required).
i. Timed maintenance scheduling to signal
maintenance activities for pumps, condenser
coil cleanings, strainer maintenance and
user-defined maintenance activities.
j. Boiler enable signal to initiate system heat-
ing mode.
k. Low ambient protection to energize cooler
and hydronic system heaters.
l. Periodic pump start to ensure pump seals
are properly maintained during off-season
periods.
m. Single step demand limit control activated by
remote contact closure.
n. Nighttime sound mode to reduce the sound
of the machine by a user-defined schedule.
3. Diagnostics:
a. The control panel shall include, as standard,
a scrolling marquee display capable of indi-
cating the safety lockout condition by
displaying a code for which an explanation
may be scrolled at the display.
b. Information included for display shall be:
1) Compressor lockout.
2) Loss of charge.
3) Low fluid flow.
4) Cooler freeze protection.
5) Cooler set point.
6) Chilled water reset parameters.
7) Thermistor and transducer malfunction.
8) Entering and leaving-fluid temperature.
9) Compressor suction temperature.
10) Evaporator and condenser pressure.
11) System refrigerant temperatures.
12) Chiller run hours.
13) Compressor run hours.
14) Compressor number of starts.
15) Low superheat.
16) Time of day:
a) Display module, in conjunction with
the microprocessor, must also be
capable of displaying the output
(results) of a service test. Service test
shall verify operation of every
switch, thermistor, fan, and com-
pressor before chiller is started.
b) Diagnostics shall include the ability
to review a list of the 20 most recent
alarms with clear language descrip-
tions of the alarm event. Display of
alarm codes without the ability for
clear language descriptions shall be
prohibited.
c) An alarm history buffer shall allow
the user to store no less than 20
alarm events with clear language
descriptions, time and date stamp
event entry.
Guide specifications (cont)
Summary of Contents for Aquasnap 30RAP010
Page 14: ...14 a30 5349 Base unit dimensions 30RAP070 090...
Page 15: ...15 ACCESSORY STORAGE TANK FOR UNIT SIZES 010 015 a30 4879 Accessory dimensions...
Page 16: ...16 ACCESSORY STORAGE TANK FOR UNIT SIZES 018 030 a30 4880 Accessory dimensions cont...
Page 17: ...17 ACCESSORY STORAGE TANK FOR UNIT SIZES 035 060 a30 4881...
Page 60: ...60 600 760 a30 5264 Typical control wiring schematic...
Page 75: ......