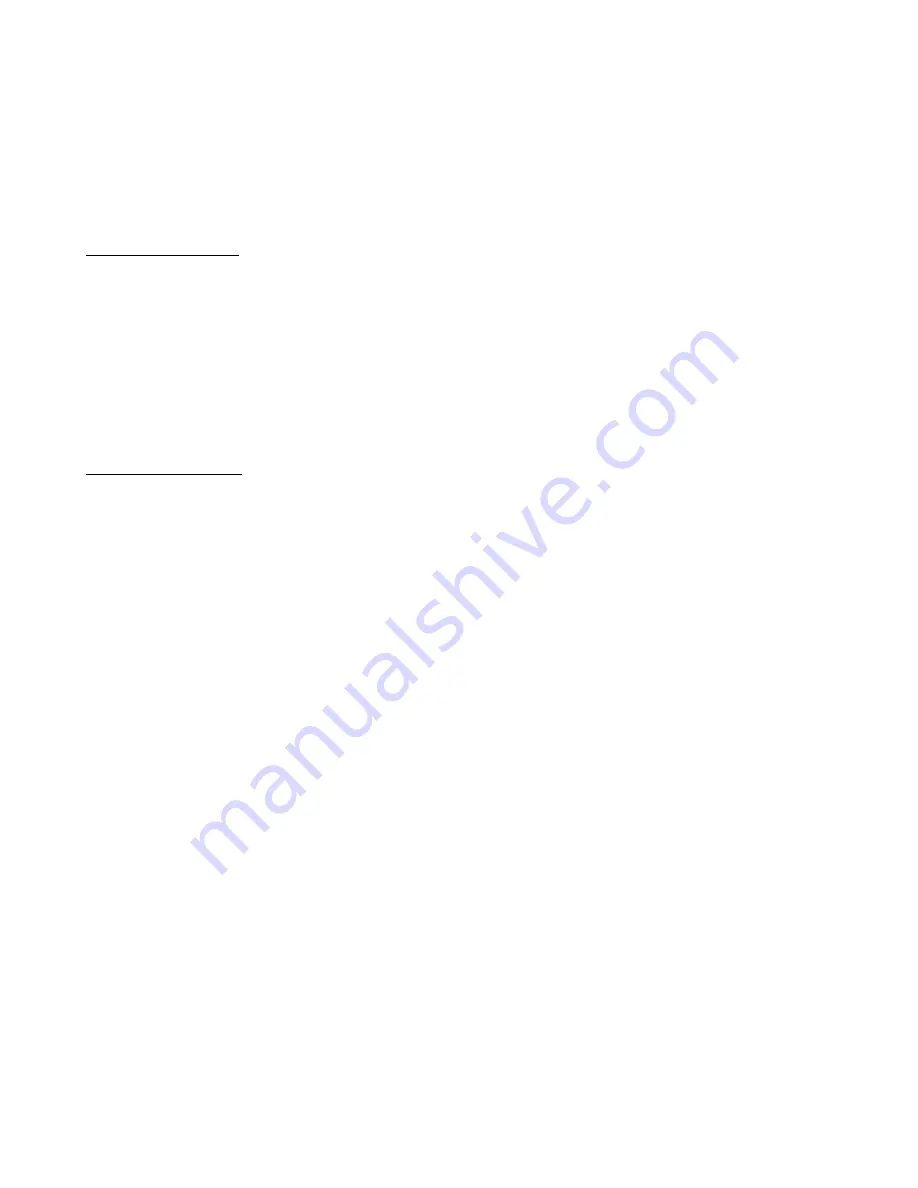
52
Ramp Loading —
The ramp loading control slows down
the rate at which the compressor loads up. This control can pre-
vent the compressor from loading up during the short period of
time when the chiller is started and the chilled water loop has to
be brought down to
CONTROL POINT
. This helps reduce
electrical demand charges by slowly bringing the chilled water
to
CONTROL POINT
. The total power draw during this period
remains almost unchanged.
There are two methods of ramp loading with the PIC II.
Ramp loading can be based on chilled water temperature or on
motor load. Either method is selected from the RAMP__DEM
screen.
1. Temperature ramp loading
(TEMP PULLDOWN RAMP)
limits the degrees per minute rate at which either leaving
chilled water or entering chilled water temperature de-
creases. This rate is configured by the operator on the
TEMP_CTL screen. The lowest temperature ramp load-
ing rate will also be used if chiller power has been off for
3 hours or more (even if the motor ramp load is selected
as the ramp loading method).
NOTE: If chiller control power has been off for 3
hours or more, the next start-up (only) will follow the
minimum configurable temperature ramp rate regard-
less of the ramp loading method and rate which are
configured in the screens. This is used to maximize oil
reclaim during start-up.
2. Motor load ramp loading (
MOTOR LOAD RAMP%/
MIN
) limits the percent per minute rate at which the com-
pressor motor current or compressor motor load increas-
es. The LOAD PULLDOWN rate is configured by the
operator on the RAMP_DEM screen in amps or kilo-
watts. The point name is
MOTOR LOAD RAMP%/MIN
.
If kilowatts is selected for the
DEMAND LIMIT SOURCE
,
the
MOTOR RATED KILOWATTS
must be entered on the
RAMP_DEM screen (information found on the chiller Requi-
sition form).
The
TEMP PULLDOWN DEG/MIN
may be viewed or
modified on the TEMP_CTL screen which is accessed from
the EQUIPMENT SERVICE screen.
PULLDOWN RAMP
TYPE, DEMAND LIMIT SOURCE
, and
MOTOR LOAD
RAMP %/MIN
may be viewed or modified on the
RAMP_DEM screen.
Rampdown —
The Rampdown control applies to VFD
equipped chillers. At machine start-up the VFD speed is set to
“Start Speed” which is the lower of
VFD MAXIMUM SPEED
or the configured value of
VFD START SPEED
.
VFD START
SPEED
is configured on the SETUP2 screen. After Ramp
Loading is complete the control begins to reduce the VFD
speed. Speed reduction continues until the leaving water tem-
perature is within the control point dead band and any condi-
tion is reached that would require the VFD speed to hold or in-
crease. The chiller is then out of Rampdown and running in
normal capacity control.
Capacity Override (Table 7) —
Capacity overrides can
prevent some safety shutdowns caused by exceeding the motor
amperage limit, refrigerant low temperature safety limit, motor
high temperature safety limit, and condenser high pressure
limit. In all cases there are 2 stages of compressor vane control.
1. When the value of interest crosses the First Stage Set
Point into the Override Region, the guide vanes are pre-
vented from opening further, and the status line on the
ICVC indicates the reason for the override. Normal ca-
pacity control operation is restored when the value cross-
es back over the First Stage Set Point, leaving the Over-
ride Region. See Table 7.
2. When the value of interest is in the Override Region and
further crosses the Second Stage Set Point, the guide
vanes are closed until the value meets the Override Ter-
mination Condition. The PIC II controls resume normal
capacity control operation after the override termination
condition has been satisfied. (In the case of high dis-
charge superheat, there is an intermediate stage.)
Whenever the motor current demand limit set point
(
ACTIVE DEMAND LIMIT
) is reached, it activates a capacity
override, again, with a 2-step process. Exceeding 110% of the
rated load amps for more than 30 seconds will initiate a safety
shutdown.
The compressor high lift (surge prevention) set point will
cause a capacity override as well. When the surge prevention
set point is reached, the controller normally will only prevent
the guide vanes from opening. If so equipped, the hot gas by-
pass valve will open instead of holding the vanes. See the
Surge Prevention section, page 56.
If the chiller is VFD-equipped, the guide vanes will be al-
lowed to open during surge prevention if the VFD is at 100%
speed or forced and the chiller is in Ramp Loading or in Ramp-
down. Opening the vanes will assist in loading the compressor
to bring it out of the surge prevention range.
High Discharge Temperature Control —
If the
discharge temperature increases above 160 F (71.1 C), the
guide vanes are proportionally opened to increase gas flow
through the compressor. If the leaving chilled water tempera-
ture is then brought 5
F (2.8
C) below the control set point
temperature, the PIC II will bring the chiller into the recycle
mode.
Compressor Bearing Temperature —
The thrust
bearing temperature (MTRB) is a calculated value which is the
temperature of the oil leaving the bearing plus an internal incre-
ment calculated with the
THRUST BRG RESET FACTOR.
The
Comp Thrust Bearing Reset is calculated using the rate of
change of the oil leaving the bearing. If the oil temperature is
stable the
COMP THRUST BRG TEMP
equals the
COMP
THRUST LVG OIL TEMP
. As the oil temperature rises, the
COMP THRUST BRG RESET
is calculated to account for any
lag between actual bearing temperature and the temperature of
the leaving oil.
In the SETUP1 screen an adjustment called the
THRUST
BRG RESET FACTOR
is an adjustment to the
COMP THRUST
BRG TEMP
calculation. The default value is 1.4 and will nor-
mally be left at that value unless other wise advised by Carrier
Service Engineering.
Oil Sump Temperature and Pump Con-
trol —
The oil sump temperature control is regulated by the
PIC II, which uses the oil heater relay when the chiller is shut
down.
As part of the pre-start checks executed by the controls, the
oil sump temperature (
OIL SUMP TEMP
) is compared to the
cooler refrigerant temperature (
EVAPORATOR REFRIG
TEMP
). If the oil temperature is less than 150 F (65.6 C) and
the difference between these 2 temperatures is 50 F (27.8 C) or
less, the start-up will be delayed until either of these conditions
is no longer true. Once this temperature is confirmed, the start-
up continues.
The oil heater relay is energized whenever the chiller com-
pressor is off and the oil sump temperature is less than 140 F
(60.0 C) or the oil sump temperature is less than the evaporator
refrigerant temperature plus 53
F (11.7
C). The oil heater is
turned off when the oil sump temperature is either
• more than 152 F (66.7 C), or
• more than 142 F (61.1 C) and more than the evaporator
refrigerant temperature plus 55
F (12.8
C).
Summary of Contents for AquaEdge 19XR series
Page 69: ...69 Fig 33 19XR Leak Test Procedures a19 1625 ...
Page 154: ...154 Fig 64 Benshaw Inc Wye Delta Unit Mounted Starter Wiring Schematic Low Voltage a19 1873 ...
Page 161: ...161 Fig 69 Typical Low Voltage Variable Frequency Drive VFD Wiring Schematic 575 v ...
Page 162: ...162 Fig 69 Typical Low Voltage Variable Frequency Drive VFD Wiring Schematic 575 v cont ...
Page 186: ...186 APPENDIX B LEAD LAG WIRING 19XR Lead Lag Schematic Series Cooler Flow a19 1655 ...
Page 187: ...187 APPENDIX B LEAD LAG WIRING cont 19XR Lead Lag Schematic Parallel Cooler Flow a19 1717 ...