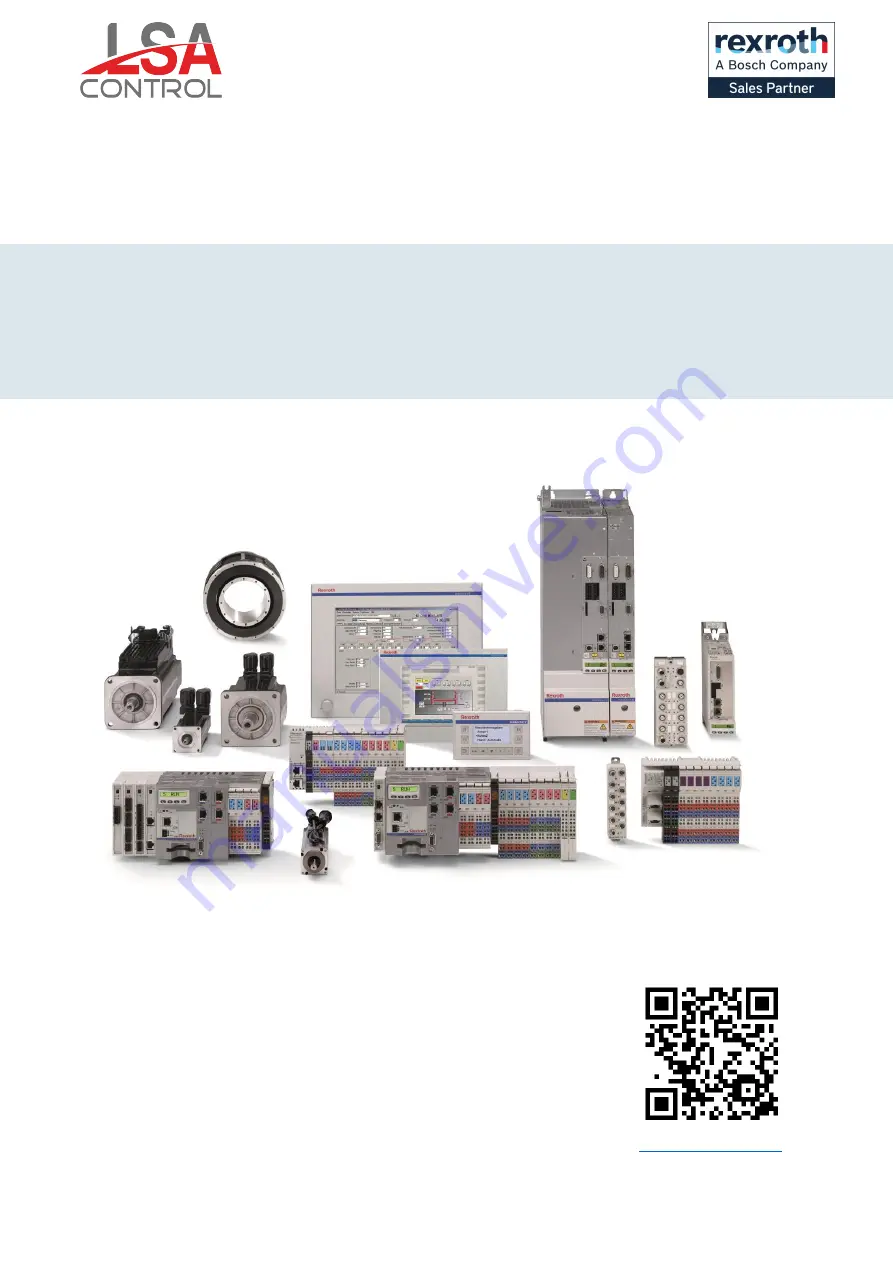
Levante Sistemas de
Automatización y Control S.L.
Catálogos
Distribuidor oficial Bosch Rexroth, Indramat, Bosch y Aventics.
LSA Control S.L. - Bosch Rexroth Sales Partner
Ronda Narciso Monturiol y Estarriol, 7-9
Edificio TecnoParQ Planta 1ª Derecha, Oficina 14
(Parque Tecnológico de Paterna)
46980 Paterna (Valencia)
www.lsa-control.com
www.boschrexroth.es